The story behind the unstoppable rise of PRS's SE guitars
How the premium US firm went about building its Asian-made SE line
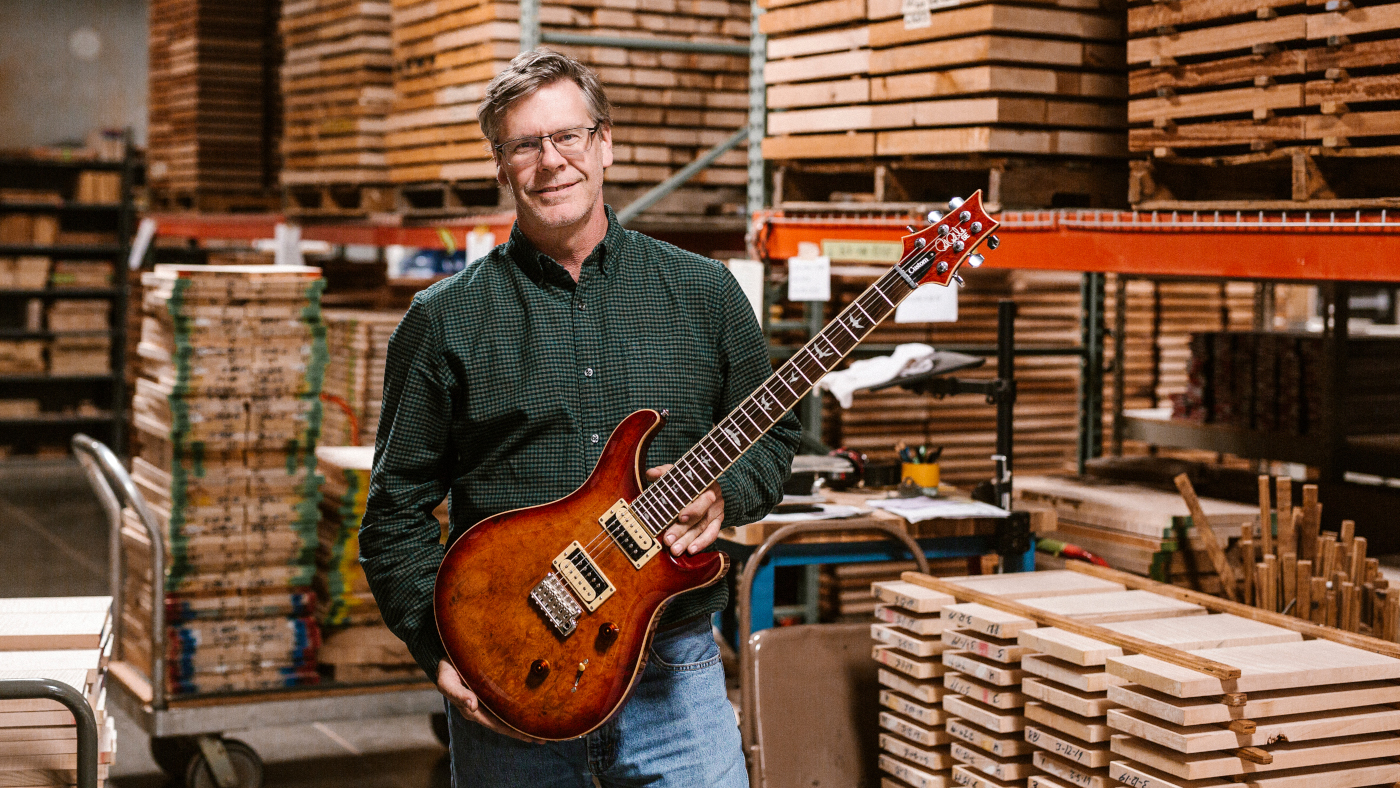
It’s been 18 years since the first ‘offshore’ SE was introduced to the PRS range. Making guitars in Asia, however, hasn’t always been as straightforward as it might seem...
The Student Edition was originally a slab-body, no-maple zone because Paul Reed Smith believed those features would impact on the sales of USA models, yet the range’s latest is the closest so far to a ‘copy’ of PRS’s core models.
“It’s a fine‐line process,” states Jack Higginbotham, PRS COO (and prime mover behind both the SE and S2 lines), diplomatically.
“It started with the new headstock logo [originally seen on the 2017 SE models]. I wanted to say we’re the same company. We’re not a different company, so I wanted the Paul Reed Smith logo with the SE as a suffix. But, you have to be careful not to get too close.
It’s about inspiring the player and I think you can do that without compromising the business
“Yet the other side of that line is that if you make an excellent guitar that’s an inspirational instrument and allow a new guitar player, or a new-to-PRS guitar player, to experience what we’re about, then I believe they’ll be more inclined to become part of our family. I don’t think that’s worth a lot of risk, but it is worth a lot of effort. It’s about inspiring the player and I think you can do that without compromising the business.”
Historically, Paul has been very protective of many hallmarks of the PRS design. It took until 2005 before an SE with a flat maple top, faced with a figured maple veneer, was allowed. Slowly, a thicker maple top with a camber around the edges became the favoured style, but the SE Paul’s Guitar takes it closer to the core.
“I took an SE Standard home to my ’shop and, using a sander, resculptured the top while keeping the same overall body thickness,” says Jack. “It sort of blends between the shaping of an SE and the current CE 24. It was something I wanted to do to make the guitar visually speak to Paul’s original design without getting too close to home. You have the headstock, the birds [from 2007] and now the body... it just speaks to the whole package.”
Get the MusicRadar Newsletter
Want all the hottest music and gear news, reviews, deals, features and more, direct to your inbox? Sign up here.
Even in the colour options, the SE Paul’s Guitar harks back in time to the 1985 full- colour catalogue, which featured a trio of yellow, red and blue Customs. “Yes,” laughs Jack. “That was intentional. It’s from the original catalogue - I have it in my ’shop at home and it’s almost like this is take two - the next generation.”
New Horizon
Aside from the changes to the guitar itself, the location of the SE’s manufacture is changing, too. Originally, the entire line was made by World Musical Instrument Co in Incheon, Korea. Recently, we’ve seen a move to an increasing number of models to Indonesia, initially PT Wildwood, and now it seems production has settled with Cor‐Tek (Cort).
We now have a focus on our guitars that previously was never able to happen
“For the first time we have a facility, in Indonesia, that is PRS Guitars,” states Jack. “There is nothing else running in that new building, just PRS. So the future is having a focused partner in manufacturing on our behalf - without crossing that line we were talking about, without getting too close to home or devaluing what we’re doing in Maryland. It’s not just a ‘I’m gonna beat you down on price’ arrangement; this is a ’shop where I know the management and have meetings with them all the time and we are discovering how to make very inspirational instruments at a very reasonable price.
“It’s still a blend from Korea. It’s simple economics: the neighbourhood got too expensive. You either increase the price or find a new way of making it affordable. Indonesia is the new Korea.
“For us, our management team is Korean. I spend time with these people, we go to dinner, I know their families - it’s an extension of PRS. And to have our own building where I know the guy who makes the necks or the bodies, I know the guy who sets the neck angles and glues them together and they’re going to do that every day - they’re not going to switch to making a Hagstrom the next day, or an ESP, or whatever. We now have a focus on our guitars that previously was never able to happen. We still have some SE guitars made in Korea, but will it always be that way? Economics say probably not.
Not where but how
“But it’s not where, it’s how it’s made and how much care is taken. That’s what we’re focusing on now - the process, the quality assurance. Doug Shive [PRS veteran and the spiritual heart of the SE line] and John Walker, who used to be with Fender and worked with Eddie Van Halen to make the EVH stuff - well, the three of us are there every month as teachers and it seems to be going well.
What Paul wants to share... is the thing that he’s in love with at this moment and with very few compromises
“So, Paul’s Guitar is exclusively made in Indonesia, yes. Carlos Santana’s new SE is also exclusively made there, but a SE Custom 24? Well, I can make that in Indonesia or Korea. But is the future Indonesia? We obviously think it is.”
Getting back to Paul’s Guitar, he can’t have been an easy ‘artist’ to work with?
“Put it in print! He’s the most difficult artist I’ve ever worked with! He is so particular and so demanding and has that tone in his head. He knows the end game before he’s even started.
“An artist model is always a particularly poignant thing to do, but this is an artist model with Paul. And what Paul wants to share with as many people as possible is the thing that he’s in love with at this moment and with very few compromises. So the trick was, how do you have the personality of a very esoteric guitar with a very special set of features that doesn’t cross the line of what SEs should be? It was a very interesting exercise for me.
“The truth is it would never be done unless you set a launch date. The key is to start the development with enough time but to also put a stake in the ground and say, ‘This is the launch date and you have to work backwards from there,’ otherwise it would never get done.
“I think you have to be satisfied that, effectively, this is version one and be done with it, otherwise - obviously - you’d never make anything. In the US, we have the ability to change on the fly to a certain degree. With the SE, it’s a more set‐in‐stone set of processes.”
So, when is the John Mayer Silver Sky coming over to the SE line, we ask? Jack laughs and says: “I like the way you did that: ‘When?’ Maybe you’d better turn off your voice recorder...”
Dave Burrluck is one of the world’s most experienced guitar journalists, who started writing back in the '80s for International Musician and Recording World, co-founded The Guitar Magazine and has been the Gear Reviews Editor of Guitarist magazine for the past two decades. Along the way, Dave has been the sole author of The PRS Guitar Book and The Player's Guide to Guitar Maintenance as well as contributing to numerous other books on the electric guitar. Dave is an active gigging and recording musician and still finds time to make, repair and mod guitars, not least for Guitarist’s The Mod Squad.
“These guitars travel around the world and they need to be road ready”: Jackson gives Misha Mansoor’s Juggernaut a new lick of paint, an ebony fingerboard and upgrades to stainless steel frets in signature model refresh
“It’s about delivering the most in-demand mods straight from the factory”: Fender hot-rods itself as the Player II Modified Series rolls out the upgrades – and it got IDLES to demo them