The anatomy of your drum kit
Under the hood of your kit
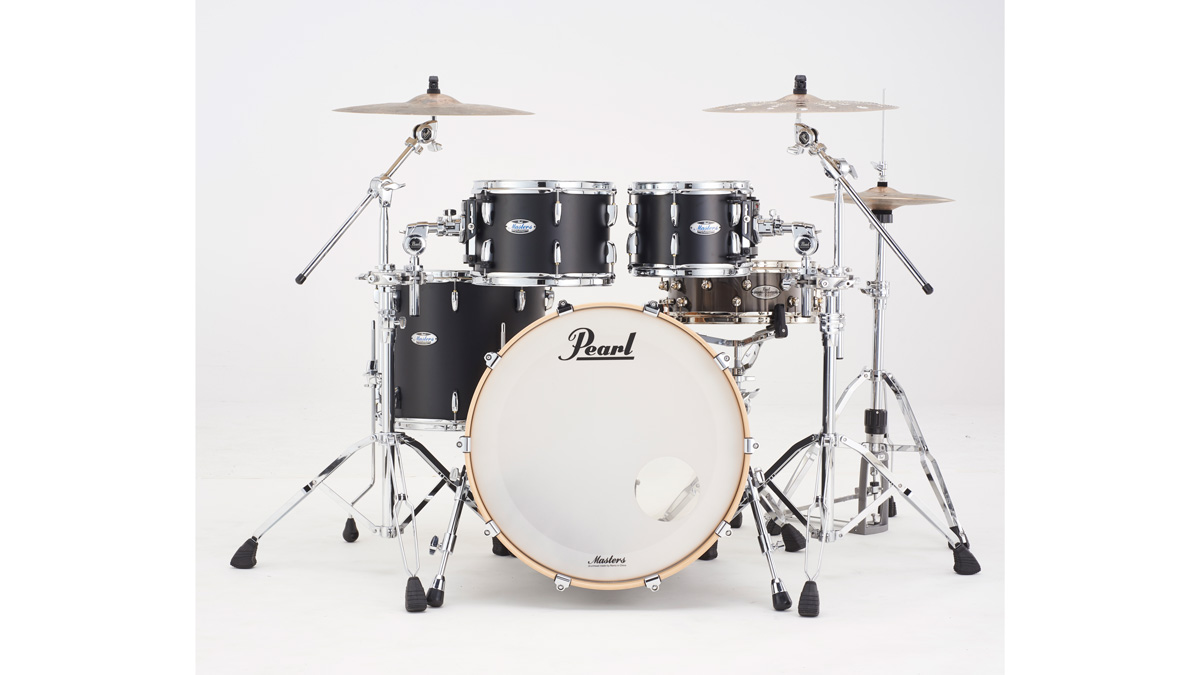
The Drums
The choices facing the prospective buyer of drum gear is staggering. Much depends on your budget, but basically the drum kit is a simple instrument made up of numerous components.
Knowing something of how these parts are constructed will help you to make informed choices when buying. Here we show you just what a drum kit is made of - how those well-crafted individual components make the sounds you love and how it all works together
Today’s drum kit has evolved over the past century from a rag-bag collection of individual percussion items appropriated from military, orchestral, theatre, world-ethnic and dance band sources, to the sleek, shiny wood-and-metal creations we all lust after. It remains though a relatively simple instrument and, truthfully, amazing value.
The Drums
The most obvious component of the drums is the shells. Aesthetically they impart the overriding look of the kit. A great deal of emphasis is therefore placed on them - the finish and the exact wood that lies beneath. Image is everything in the music world, so finish is undeniably important. Plastic wrap coverings are cheaper to apply and don’t require the underlying face wood to be perfect. They are therefore the province of cheaper kits. Top quality wraps though can also be applied to pro drums. There is a never-ending debate about what effect this has on the sound. If there is any, it is surely minuscule.
Every type of finish does the job of enhancing and protecting the wood, which often includes a veneer of precious, rare timber. Whether stained, waxed or painted/lacquered, a stunning finish requires numerous applications to achieve and is thus hugely labour intensive and expensive.
The finish is a major factor in drum choice. But the type of wood? Well, maybe rather less so. That may seem controversial, but actually, as long as the wood is good quality hardwood, there are many species that will serve. As we shall see, the really important factors in your sound are drum size, the actual quality of shell construction and the heads you choose. (And perhaps most important, how you tune and play them. But that is for another feature!)
Drum shells are traditionally made from wood, except for the snare drum which is equally often made from metal - steel, aluminium, brass, occasionally bronze or copper. Drum shells are also sometimes made from synthetic materials such as Plexiglas (Perspex) or fibreglass. Remo has what it calls an acousticon shell made from hardwood fibres impregnated with resin.
Wood shell construction
Virtually any species of wood can and has been used, from birch to bamboo. What matters is how conducive that wood is to forming into a circle and staying circular. The closer to round the shell, the easier it is to tension a plastic head evenly, which is necessary to get a reliable and musical response.
Accordingly, the better quality of timber - the harder it is, the more devoid of blemishes and knots - the easier it is to make a rigid cylinder. A large part of what you pay for in an expensive kit is superior shell integrity.
Most shells are made from plywood. This plywood is usually cross-laminated - that is, each succeeding single ply is laid at 90° (a right angle) to the preceding one (or occasionally diagonally, as in DW's ‘X’ shells). This makes the plywood vastly stronger and counteracts the wood’s natural tendency to want to straighten out.
Shell-makers sometimes construct shells one ply at a time. But more often they take a 2-ply or 3-ply sheet and, cut to the exact size so that the edge butts up, insert it into a circular mould. Then they take another ply sheet and glue that inside the first one. So now you have a 4-ply or 6-ply shell. Doing this successively you can see how multi-ply shells are built up.
As the thin plies are inserted into the mould, the join is crucial and some companies (for example Yamaha and the British Drum Company) cut that join on a diagonal, which makes it easier to butt up by sliding the ends down into the mould until they make a super-tight join.
Moreover, these joins are staggered around the shell. So, for example, a 9-ply shell made up of three sets of 3-ply veneers will have joins at three equi-distant positions around the shell.
Most big-time companies microwave the shells to harden them and to speed things along. Smaller companies construct the shells cold and leave them to cure. They claim this is better, but whether anyone can actually hear a difference is a moot point!
Either way you have a very strong shell indeed. Now if the veneers used are also of the finest and hardest timbers then that shell will be even more sturdy and round. In fact it’s possible to make a shell with as few as three or four thin plies and create a shell that will stay circular for life. This is important because a thinner shell resonates more freely than a thick shell and imparts a deeper, darker timbre to the drum.
These qualities are prized and this is why - generally speaking - expensive drums have thinner shells, and are made of favoured grade-one hardwoods, like maple, birch, ash, beech, oak and real mahogany, etc.
Correspondingly budget shells tend to be thicker. They employ timber of lesser quality/expense, maybe less consistent and softer. So it is necessary to make the shells (and plies) a little thicker to ensure roundness and stability. Pearl’s popular budget-leading Export has 6-ply 7.5mm shells, where the top range masterworks shells are 4-ply, 5mm thick.
Snare drums occasionally have much thicker shells, like Sonor’s artist with its 27-ply 28mm-thick beech shell. This is because, in contrast to toms, the snare drum suits less of a sustained note and more of a loud, penetrating, crisp clout.
In the past the construction of budget shells could be iffy - you’d see wood filler where the plies didn’t quite meet up. But today the budget shells reviewed on MusicRadar every month look almost as good as the impeccably finished top-enders.
And they sound almost as good too. The slight lack of quality and knock-’em-dead finish hardly impinges on the timbre. With high-end drums it’s a case of subtly diminishing returns in the sound department if not the looks!
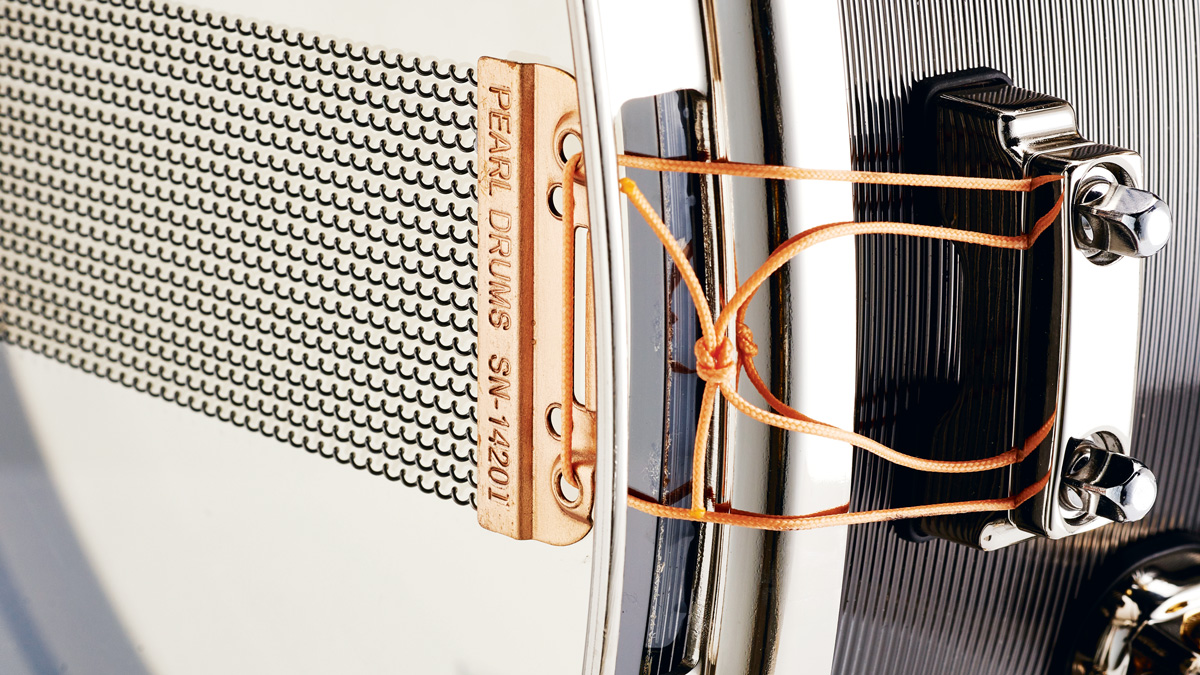
Bearing edges and snare beds
Tuning problems are more likely with poor bearing edges. Whatever the shell, the edge that makes contact with the head is crucial, acting like the bridge of a guitar or violin in making or breaking tuning ability.
Modern bearing edges are mostly cut quite sharp and routed at 45° to the inside, with a smaller single–ply 45° counter-cut or round-over to the outside. Occasionally the 45° peak will be right in the middle of the shell (as with Spaun drums). Gretsch edges are cut at 30°/60°.
What matters are that the edge is even and flat all round with no dips or inconsistencies, so that the head sits uniformly. drummers place great importance on the accuracy of the bearing edge. If it is poor then there will be dull spots or fruity overtones that can’t be ironed out.
Along with everything else in drum manufacture, tolerances have improved and today most drums, even cheap ones, have pretty decent edges. If a particular drum is giving you headaches though it is worth examining the edges carefully. Place the bare shell on a reliably flat surface, like a sheet of thick glass or kitchen worktop and shine a torch inside to see if any light creeps under the edge. A competent drum-craftsperson should be able to ‘true’ the edges if needed.
Along with everything else in drum manufacture, tolerances have improved and today most drums, even cheap ones, have pretty decent edges
Older drums up to the 1960s had rounded edges. Rounded edges soften the attack while allowing more of the head to contact the wood, imparting more woody timbre to the overall drum tone. They also shorten the sustain a tad so the sound is more thuddy. rounded edges have recently made a comeback on some new lines with vintage characteristics, such as Ludwig’s Legacy classics.
At the position either side of the snare drum shell bottom where the snare wires are attached by cord or tape there should be a shallow dip filed into the edge. This ‘snare bed’ may not be immediately obvious as it is quite gentle. On older drums it may be more obvious. The bed enables the snare wires to lie flatter against the bottom head which improves snare response and helps reduce snare buzz.
A word here though - snare buzz is impossible to eliminate entirely. You can tune the nearest small tom (say) to minimise sympathetic rattling, but at some stage something will set off your wires. It may well be your bass player! do what you have to if/when it becomes a problem, but live with it. Don’t feel guilty!
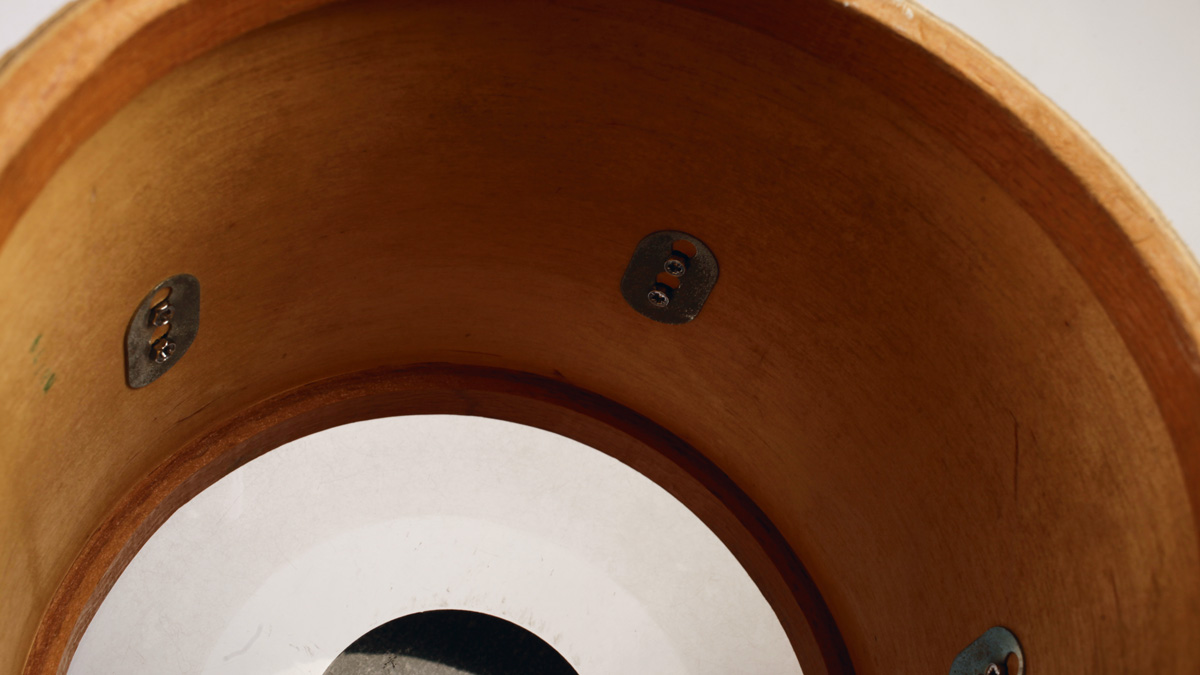
Bigger, smaller, shallower, deeper
You want a louder and deeper sound? Get a bigger drum - it’s that simple.
Since America is the home of the drum kit we still describe drum sizes (and cymbal sizes) in inches of diameter. hoorah! For example, a shell pack will be sold as 22"/13"/16", say. And in Europe an individual drum, logically, has its diameter quoted first. Thus we say 14"x5" (the Americans say 5"x14", which makes absolutely no sense to this writer.)
The greater the drum’s diameter the deeper its sound. With toms it’s an accepted practice that as the diameter increases so does the depth: 12"x8", 16"x14", etc. A deeper shell will also make the sound lower, simply by increasing the internal volume/capacity of the shell. If we want more attack and clarity we decrease the depth. we see this in snare drums where a standard 14"x5" is sharper than a broad fat rock ballad-style 14"x8".
Likewise, if we want the depth but at the same time the definition and immediacy of John Bonham we go for his 26"x14" bass drum. Big diameter, shallow depth. A deeper drum reacts more slowly than a shallow one as the air column has to travel further down the shell to resonate and reflect.
Bigger drum companies offer a choice of depths for each diameter in their top drum ranges, so you might choose, for example, shallower ‘fast’ or ‘hyper’ toms. Tama offers six depth variations in its Starclassic series, which must be a record! You can see that everything in drums is a compromise - playing off one factor against another to get the happy medium.
Drum heads
When we look at a drum kit it’s the gloriously finished shells and the gleaming chrome hardware that catches our eye, yet without the heads all this is useless! If you stretch a head over a metal rim - with no shell - it makes almost as much sound as a head stretched over a shell. Roto toms illustrate this perfectly. in fact it’s often stated that the head makes 80 percent of a drum’s sound and this is another reason why a budget drum kit can sound almost as good as an expensive one.
The top head is called the batter head, while the bottom head is the resonant head as it resonates in response to the sound waves generated by striking the batter. You can still get (expensive) real calfskin vellums, but most kit drummers use plastic heads made from polyester Mylar film. The principal head companies are all American: Remo, Evans, Aquarian and attack. These companies are dedicated to the specialist task of producing heads (although Remo is also big into percussion instruments).
Broadly speaking heads are either single-ply or double-ply, and coated (usually, though not always, white) or clear
Broadly speaking heads are either single-ply or double-ply, and coated (usually, though not always, white) or clear. Single-ply heads are the starting point and the industry standard is Remo’s Weatherking ambassador, made from 10-mil (0.01") or ‘1000 gauge’ Mylar film, coated or clear. All the other companies make equivalent single-ply general purpose heads, eg: Aquarian’s texture coated and classic clear.
You can play your whole career with just these, but maybe you’re really heavy and want something more durable, or you’re a light player who wants something more sensitive. No problem, everyone makes thicker heads - which are mostly twin-ply - and thinner heads, like Remo’s diplomat, which is 7.5-mil. incidentally, snare side heads are usually much thinner, like Remo and Evans’ clear or hazy 3-mil heads. These maximise the snare response, but you need to be careful if you strike such a thin head as it will pit.
Double-ply heads are significantly stronger and create a darker, more focused sound with fewer overtones. Remo’s Emperor is two plies of 7-mil Mylar, as is Evans’ G2, both significantly tougher than a single ply of 14-mil film.
Besides these staples there are many specialist heads which often have inbuilt damping rings of one design or another. Remo’s Pinstripe and Aquarian’s Performance II have twin plies bonded around the perimeter, allowing really deep and dark tuning with great attack. Remo’s controlled sound (CS) is a single-ply with a black dot bonded to the centre, for reinforcement rather than damping.
Perimeter damping really goes to town on bass drum heads where Evans’ Emad incorporates perimeter trays with interchangeable foam rings, and Aquarian’s SuperKicks have bonded felt ring dampers for a warm and funky slap. Front heads on bass drums are regularly seen with small 4" to 6" circular holes cut into them (often off-centre), which allow the large volume of air to expel, increasing impact while lessening boom and providing a handy portal for microphones.
Even more specialist heads are available for marching bands who go for extreme high tensions, leading to Remo’s Falam heads which incorporate bullet-proof Kevlar material. while at the opposite extreme, vintage kit enthusiasts can buy calf-style heads such as Evans’ calftones, Aquarian’s Vintage and Remo’s Fibreskyns and renaissance.
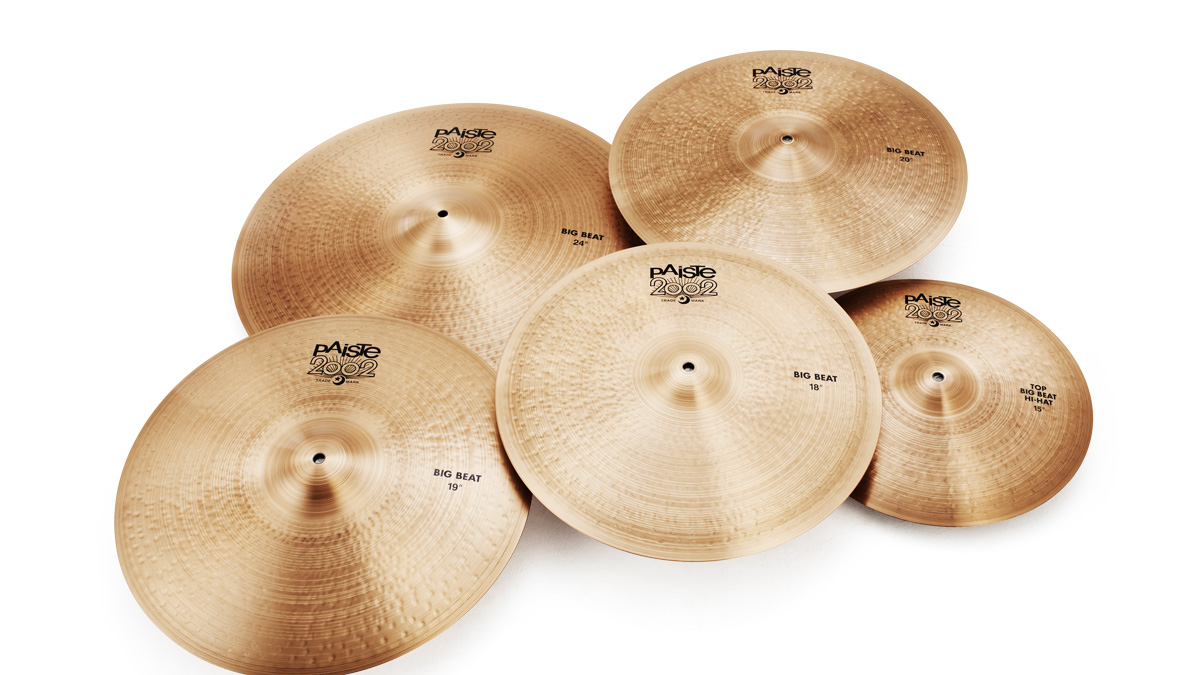
Cymbals
An average set of drums with good heads and a decent player can sound a million dollars. Not so much with budget cymbals. a cheap cymbal will set your teeth on edge played next to an expensive one.
But, there’s plenty to consider when it comes to cymbals…
Bronze alloys
Most cymbals are made from bronze, which is an alloy of copper and tin. The most commonly used allow is B20 bronze, which combines 80% copper and 20% tin.
The other common alloy is B8 (92% copper, 8% tin). This is most commonly used with less expensive cymbals. All the cymbal companies now make B8s, although Sabian’s and Zildjian’s remain budget lines, whereas Paiste and the German Meinl have professional quality lines using B8. Paiste is justifiably proud of its pioneering B8 heritage and calls it ‘2002 alloy’, or cusn8.
Professional spec
What makes a cymbal special is the amount of work that has gone into producing it. This applies not just to B20 bronze cymbals but to some B8s, and other alloy variations like Meinl’s B10, B12 and Paiste’s signature B15. Whatever the alloy there are a host of processes involved in turning a flat raw disc into a shapely, shimmering platter with attractive musical tone. These include multiple reheating and rolling, stamping the bell, tempering, forming the overall profile, hammering, lathing, smoothing the edges, maturing or ageing, polishing and applying a finish.
All these processes affect the final sound. In the past much was done manually and the image of the ancient skilled artisan hand-hammering individual cymbals conjured a great mystique. But to produce a consistent product under conditions that satisfy modern health and safety standards means that cymbal workplaces have (largely) moved on from the sweaty, deafening, dangerous Turkish foundries to clean and efficient factories.
What makes a cymbal special is the amount of work that has gone into producing it
It’s still a brutal, labour-intensive, complex process, but what drummers really need to know is at least something of how these multiple operations impact on the sound they are looking for.
At its simplest, the sound a cymbal makes is a trade-off between many parameters. For example, the larger the diameter the deeper the sound. But the thicker and weightier the metal the higher the pitch and greater the sustain. A thin cymbal will have a deeper sound, but a shorter sustain. Crash cymbals are usually thinner and lighter than ride cymbals so that they respond faster (less energy required to energise them). Heavy cymbals are often better for riding as the greater mass requires more energy to galvanise, thus the stick response is more ting-y and distinct. If you crash a heavy ride cymbal it will take longer to respond, but will sustain forever.
All this is simple laws-of-physics logic. And added to these considerations are the shape and size of bell and the overall profile of the cymbal. Large bells increase a cymbal’s power and spread, which is why a flat cymbal with no bell is soft, almost delicate, with an ultra-clean stick response more difficult to fathom are the effects of the many ways a cymbal can be lathed and hammered. Videos of cymbals being lathed are magical as the dull disc is brought to luminous life by shaving away metal. this makes the cymbal lighter, opens it up and deepens the sound. Thicker, un-lathed - or ‘raw’ - cymbals are often deployed in louder styles of music as they are more clangy and harsh.
Crash cymbals are usually thinner and lighter than ride cymbals so that they respond faster (less energy required to energise them)
Hammering compresses the metal, making the sound more complex by disrupting vibrations, shortening sustain and darkening the tone. Cymbalsmiths have endless fun experimenting with top and underside combinations of large and small hammering, broad and thin lathing, resulting in the vast number of cymbals on the market.
Cymbals can now be ‘designed’ utilising comprehension of all these parameters and there are ever more categories to salivate over. Buying online is fine if you really know what you’re after. But cymbals need to be played and heard in context. Drop by your local drum store and take your own cymbals along for a known comparison. Try out alternatives and build up a relationship with the shop staff. then buy from the store! For much more check out Rhythm magazine and Geoff Nicholls’ The Drum Handbook.