Why has DIY gear become so popular?
Click-together synths and controllers, 3D printing and crowdfunding discussed
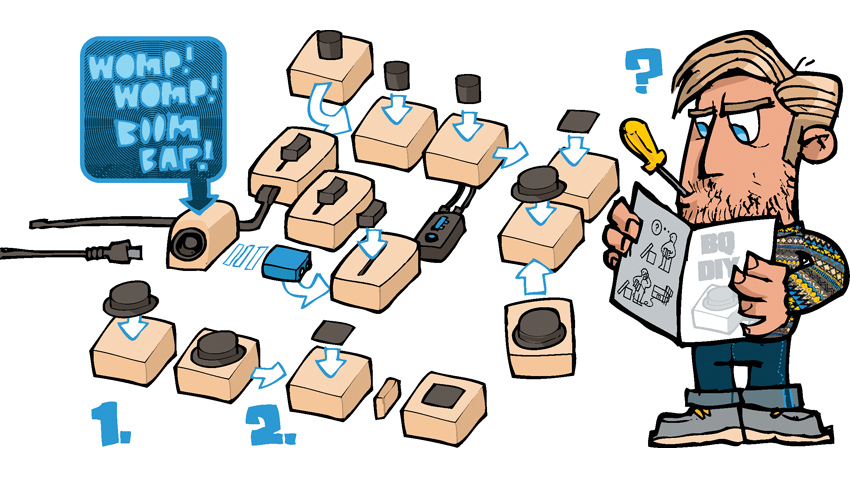
Doing "a spot of DIY" at the weekend is as English a tradition as a morning cup of tea or a chat about the weather, but for most people, it usually consists of putting down some new gravel in the garden or re-doing the grout on the bathroom tiles.
In high-tech music-making circles, however, the term 'DIY' has recently taken on rather more exciting connotations. Recent months have seen a slew of products being launched by small companies and individuals who've taken it upon themselves to bring their creations to market. And in a nice piece of symmetry, many of these products are designed to help users come up with their own controllers, synths or other devices.
Of course, it's been possible for pretty much anyone to have a go at building their own music software creations for a long time (via platforms such as Max, Reaktor, SynthMaker and SynthEdit), but as far as hardware goes, the game definitely seems to have changed.
So what's going on? Why is everyone suddenly looking to build their own gear - whether they're handy with a soldering iron or not - and what effect might this DIY boom have on your music making?
If you're a computer musician, arguably the most notable area to be hit by the DIY juggernaut is that of the MIDI controller. We're seeing homebrewed designs leaking onto the internet on what seems like a daily basis, so you may have started wondering if it's worth taking the plunge and coming up with your own.
"Why is everyone suddenly looking to build their own gear - whether they're handy with a soldering iron or not - and what effect might this DIY boom have on your music making?"
Given how many off-the-shelf controllers are available, however, is there really anything to be gained by doing this? We spoke to Dave Cross, Head of Research & Development for Dubspot, Inc, and a custom controller expert.
Just for you
"The key benefit is choice," he tells us. "Off-the- shelf products must, by their very nature, cater to multiple usage scenarios. It's inherent to the economics of manufacturing. But a device that caters to multiple users' wants cannot cater to a single user's needs without that person also making concessions to their workflow. So 'choice' actually represents pain towards the status quo: custom is a reasonable option if your frustration with the existing market of MIDI controllers is extraordinary."
Get the MusicRadar Newsletter
Want all the hottest music and gear news, reviews, deals, features and more, direct to your inbox? Sign up here.
Note the word "extraordinary" here - unless you're really unhappy with what's on offer, a custom controller might not be worth the effort and expense. But if you don't have any previous electronics experience, how easy - or difficult - is it to go about designing and building one?
"It has gotten quite easy to wire up a knob or a slider to a circuit board and have it send MIDI," explains Dave Cross. "At the end of the day, it's just a bit of wiring. What remains difficult are the non-electronics challenges of designing enclosures, creating faceplates and sourcing parts. This second layer of detail is what turns a jumble of wires into an instrument."
Perhaps in recognition of this last point - that a load of wires and components does not a functional item make - the last few months have seen a boom in products based on hardware modules that can be clipped together. We've seen littleBits and Korg's Synth Kit, which enables you to build your own analogue synth; the similarly themed Patchworks system, which should be available soon; and Palette, which offers a way for you to buy a MIDI controller in kit form (as a box full of individual knobs, faders and buttons) and then stick it together as you wish. Solutions like this, somewhere between building your own gear and buying it ready- made, seem to have struck a chord with consumers. Why are they so popular?
"The products you mention combine two themes: our insatiable fascination with building things, plus technology that turns a physical connection into a specialised electrical connection," reckons Dave Cross. "This is a recipe for creating 'quick wins' - a framework that allows someone to succeed with only a novice understanding of the system. Children's museum exhibits employ this technique extensively; it's a genius way to teach and to encourage creativity. That said, these products struggle with their toy-like perception."
This is an interesting point; although these Lego-style platforms are proving popular with consumers, it's hard to know whether people are attracted to them because they think they're going to be able to build something genuinely useful with them, or just because they like the idea of going through the building process itself. A click-together controller might sound like a great idea, but is it really going to be something that you'll use in your studio, or will it turn out to be yet another distraction?
A new dimension
That said, it seems likely that modular platforms that ease the DIY process are going to become increasingly popular, not least because it's going to get easier and easier for people to create them. No longer can would-be manufacturers simply design products - thanks to 3D printing, they can create them, too.
"I would bet my first-born that home fabrication will significantly disrupt existing models of production and distribution," says Dave Cross. "But I can't be sure which major industry will be disrupted first because right now, the most well-known market for 3D printed designs is filled with novelty items. 3D printing is a revolution for tinkerers with 3D CAD expertise. It won't be a revolution for the masses until there's a library of useful 3D files to print from."
True enough, but if 3D printing is one buzzphrase that's associated with small-scale hardware production, crowdfunding is most certainly the other. When a DIY project is launched, it almost feels inevitable now that it'll have a Kickstarter (or similar) campaign behind it, so are these platforms making it easier for newcomers to get into the market?
"The 3D printing and Kickstarter revolutions go hand-in-hand: both have the potential to disrupt the existing models of producing and distributing goods," believes Dave Cross. "3D Printing will do it by eliminating the need for quantity, and crowdfunding will do it by tipping the scales away from distributors and towards manufacturers.
"The 3D printing and Kickstarter revolutions go hand-in-hand: both have the potential to disrupt the existing models of producing and distributing goods." Dave Cross, Dubspot
"Crowdfunding can solve a prickly chicken/ egg problem inherent to manufacturing. Your widget may cost £50, but it will cost £30,000 upfront to prepare the machines for your product. Crowdfunding that initial investment turns a major gamble into a surefire bet.
"That said, many manufacturers seem more than willing to take that gamble with their own funds after they've achieved initial success. In other words, how many companies have put their 'second' product up for crowdfunding? What does that say about the current value of crowdfunding to an established manufacturer?"
It's an interesting point, but it does seem that a serendipitous set of circumstances has made it easier than ever for would-be manufacturers to bring their products to market. This has the potential to affect not just the types of products that we buy in the future, but also our ability to create things ourselves.
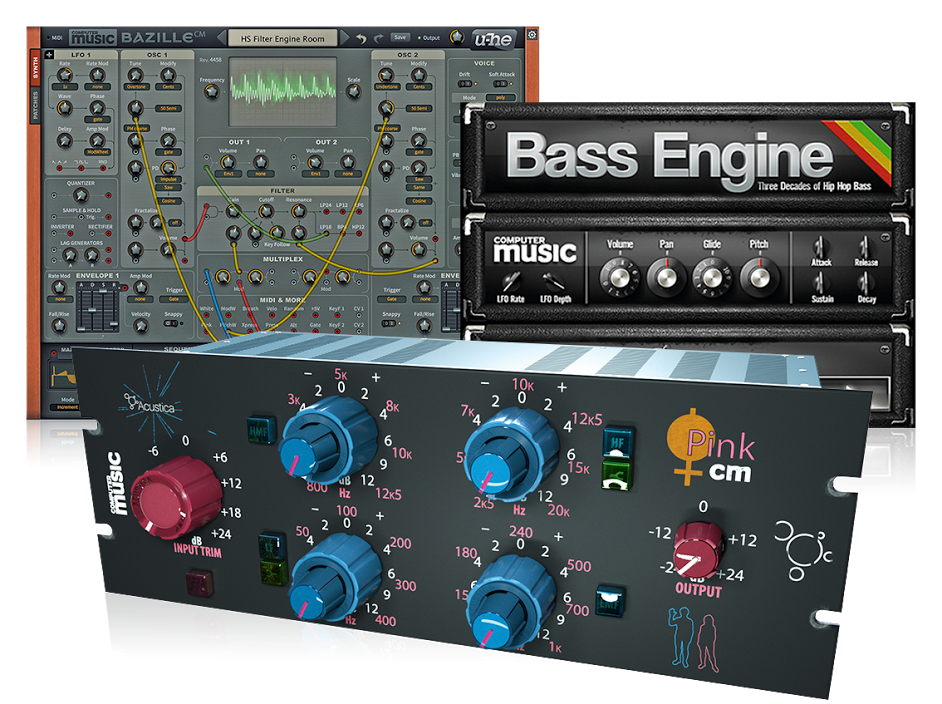
Computer Music magazine is the world’s best selling publication dedicated solely to making great music with your Mac or PC computer. Each issue it brings its lucky readers the best in cutting-edge tutorials, need-to-know, expert software reviews and even all the tools you actually need to make great music today, courtesy of our legendary CM Plugin Suite.