How to fix tuning problems on your guitar
Our guitar guide shows you how to stay in tune
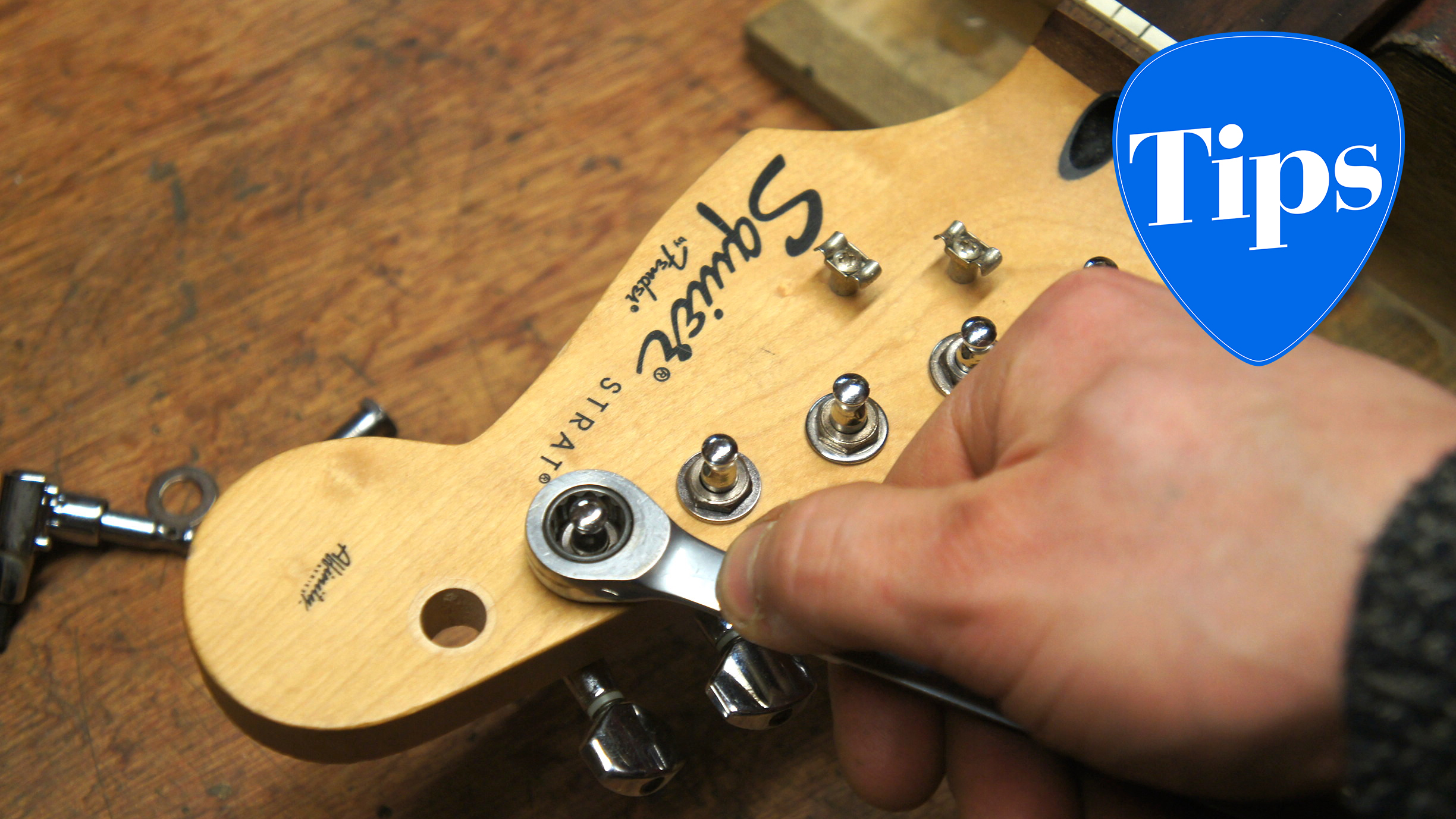
Guitar maintenance: We’ve teamed up with Jack Ellis from Manchester's Jack’s Instrument Services to solve common guitar issues and mod your instrument with simple tools and a DIY approach. This time we're looking at an essential for all players; how to squeeze better tuning stability from your guitar and stay in tune for longer!
Jack Ellis and his team run an independent Manchester guitar setup and guitar repair service from their Cheetham Hill based workshop, serving the musicians of the Northwest England's electric guitars, bass guitars, acoustic guitars and much more, including custom pedals.
He also offers a custom guitar pickguard-making service called Tiny Tone.
Let’s first think about how a string is tuned. It’s held at a very particular pitch, so when you change that tension the pitch rises. Of course, us guitarists will go and mess with that deliberately though by battering the strings, doing string bends and going nuts on the tremolo…
We’ll show you how to logically trace through common problem areas to eliminate friction and also some good fastening tips where it counts. Stay tuned…
Tools you will need
- PH2, PH1, Flathead screwdrivers
- Needle Nose Pliers
- Flush cut wire cutters
- String Cutter pliers
- Bradawl
- Thin Superglue
- Fresh Strings
- String Winder
- Cocktail Sticks
- Big Bends Nut Sauce (or similar)
Making sure tuners are properly fastened
Firstly, our strings need to stay stable at least to have any hope of staying at the same tension, loose tuners are totally useless!
There are generally two types out there, ones that screw from the rear and ones that bolt through from the front. With the Bolt through tuner types, you simply tighten up the 10mm nut on the front - it’s usually loose….
Our Gretsch here has tiny wee screws that fasten it to the rear of the headstock, as such the diddy screws have a very important job to do.
The timber underneath the super hard finish is not as tough as you think as these screw holes can slip very easily. If you notice they're loose, it's straightforward to address the issue.
Get the MusicRadar Newsletter
Want all the hottest music and gear news, reviews, deals, features and more, direct to your inbox? Sign up here.
Pop off the tuners and we’ll repair the holes.
Using cocktail sticks (made from hardwood or bamboo) you can fill the holes. Audition a couple of different cocktail stick as they're all different sizes in the pack, trim slightly under the length that you need to fill the hole then push in.
Getting these cocktail sticks to be strong and stable requires a dab of ultra low viscosity cyanoacrylate – AKA thin superglue. This soaks in nice and deep.
With all the holes filled and solidified we suggest you simply use a bradawl to jab a nice hole to receive the screws.
Try it out without a pilot hole, if when re-screwing in they feel too tight then pop a small pilot hole in with a drill; tight is nice.
Reinstall those tuners!
Wrap locking strings
Fitting your strings the right way is essential for stable tuning. We’ve got an awesome technique to show you for wrap-locking your strings on, it self traps the tail of the string without making it a pain to remove when it’s time to restring.
See a full in-depth in-depth guide on how to restring a guitar.
Post the string though and kink the rear.
Wrap the tail backward and under the string.
Pulling the tail sharply up, create a kink under what will be the start-wind.
Wind the string underneath by turning the tuning key, to keep it super neat, apply some string tension with your hand while winding.
Stretch those strings in, by stretching in your strings you help clamp the windings down onto the tuner capstan which is vital to performance. Pull up each string a touch then re tune, you’ll be surprised at how much the pitch drops!
Friction Points: Attention to the nut
The nut is really a key player when it comes to guitar tuning issues as it’s a friction point; the string is meant to slide through it cleanly when tuning and of course when bending strings too.
Nuts can cause issues for a number of reasons, but here’s an easy one for you to spot; is there grime in the bottom of the slot?
With some nuts, they simply will not work without slight modification. Working on nuts is actually very technical and requires a professional. Nuts guide your string spacing, string height, action at this end of the neck and of course can affect tuning stability if too tight.
For a glance at how one is created, see our guide on making a guitar nut from bone.
Rusty, nasty grime builds up in the bottom of the slots.
One drag with a nut file cleans these out great, you must be careful not to accidentally lower the bottom of the string slot.
Finish up with some specialised lubricant, Big Bend’s Nut Sauce or similar!
Honourable mention: Floyd Rose Locking Nuts
Friction points: string retainers / trees
If your guitar has string retainers then those little guys are friction points with string travel too, a healthy but tidy blob of Nut Sauce will really help out there too for lubrication.
Friction points: bridges
This is a big deal on this Gretsch and seems to be very common on many Gretsch Electromatic models. We need the string to slide over the saddles smoothly with relative ease - just like the nut.
When you dump the tremolo arm down, the strings slide through right? When you let go in theory they should return to exactly where they were, in practise this rarely happens correctly.
You can help out your bridge by lubricating the saddle slots to ease the string through.
Tremolo tuning test tip
And finally, for those of you to check tuning stability with the tremolo on your guitar; tune the guitar, pull the arm up and release gently, observe the pitch. Now tap the arm downwards so that the pitch drops, when you let go of it the pitch should be the same as our first observation.
The best tremolos have a tiny pitch deviation, ones with excessive friction have much more pitch deviation: something is stopping the tremolo returning to its neutral position properly.
If your tremolo comes up short in this test then you should lubricate the friction points and the fulcrum points.
Getting the best out of the myriad of tremolo types can be elusive but a good rule of thumb is keep them clean, lubricated with attention to the fulcrums and friction points.
Here's some specific tips:
• On a Bigsby, the frame could be warped due to uneven pressure, this bends the U shaped frame and can pinch the bearings. Otherwise they're very well made!
• On a blade-style tremolo EG Floyd Rose or modern two-point Strat bridges it could be dull blade edges or springs rubbing in the back cavity, disassemble to inspect.
• If you have a Stratocaster six-point vintage-style tremolo, a modern two-point tremolo upgrade will certainly help – this is because there's less friction at only two fulcrum points instead of six. Floyd Rose tremolos use this idea too.
Find out more about how to set up a guitar tremolo.
And how to setup up a Floyd Rose tremolo.
• Jazzmaster and Jaguar tremolos are technically a blade edge but it's hidden underneath, a bit of lubrication wouldn't hurt!
• Mustang tremolos are a two-point tremolo so you can lubricate the two fulcrum points with ease.
Jazzmaster, Jaguar and Mustang tremolos are all usually paired with the rocking bridge too. Get to grips with those with our in depth article here.
How to set up your guitar: a DIY guide to intonation, truss rod, bridge and fretboard maintenance
Jack runs an independent guitar setup and guitar repair service in Manchester, England. He serves the musicians of the Northwest of England, working on electric guitars, bass guitars, acoustic guitars and more. Jack has been writing the Fix Your Guitar column in Total Guitar Magazine since 2017.