Meet your maker: Taylor's search for the ultimate maple guitar
We head to the mountains with Taylor's top brass
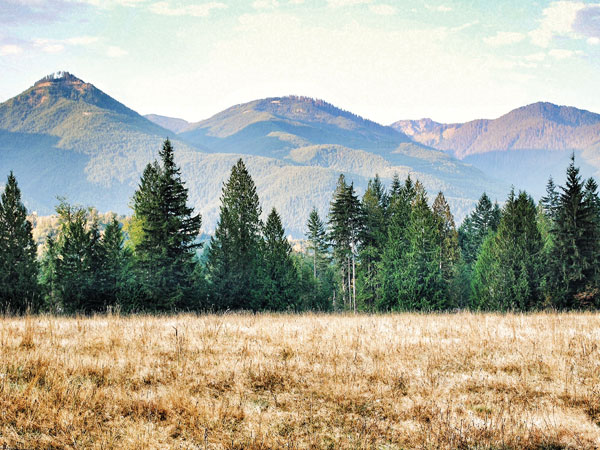
Introduction
With its new 600 Series, Taylor wants to persuade you that maple can sound as warm, well-balanced and sweet as any rosewood or mahogany guitar. But why? The answer concerns the future of guitar-making itself. We travel to America’s Cascade Mountains to find out more...
"Not many maple trees contain figured wood because, strictly speaking, it’s a growth defect"
Do you have straight or curly hair? Whichever it is, the reason your hair looks a certain way lies in your genes. If your parents both have curly hair - guess what, you probably have it, too.
But what has that got to do with guitars? Well, the figured maple that adorns many beautiful instruments is, like curly hair, a product of genetics. Split open the right kind of maple log lengthwise, and figuring is visible as an undulating ripple in the grain.
But not many maple trees contain figured wood because, strictly speaking, it’s a growth defect - albeit a harmless one that looks attractive when you make it into a guitar, where it manifests itself in subtle visual patterns, including the famous ‘flames’ seen on the maple tops of old sunburst Les Pauls.
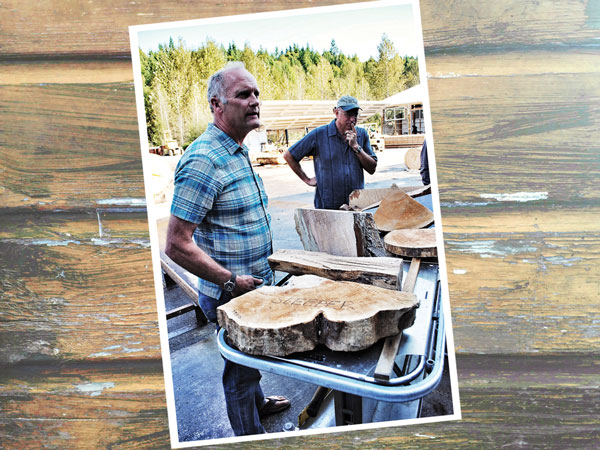
The problem with figured maple
Herein lies a problem - in fact, a series of problems - that Taylor would like to solve. The reason the Californian company is taking a fresh look at maple is because the supply of tonewoods traditionally used to make acoustic guitars is growing harder to obtain.
Mahogany, rosewood and ebony trees take many decades to mature and, when they are allowed to grow to full size, they become enormously valuable.
"Taylor thinks it might also be possible to make beautiful-sounding acoustic guitars from trees that aren’t under any logging pressure at all"
The sad reality is that in many of the tropical regions where such trees flourish, illegal logging, corruption and conflict all hamper the chances of harvesting old-growth trees in a responsible way.
Where there are no controls on logging, ancient forests tumble with frightening rapidity. The scarcer such trees become, the higher their value rises - making them ever-more tempting targets for illegal logging, keeping the whole vicious circle spinning like a sawblade.
Certainly, there are verifiable ways to obtain tropical hardwoods from sustainable sources, and increasing numbers of makers, such as Martin, Walden and Taylor, are making good use of them.
So it’s not the case that all such woods are ‘bad’, but Taylor thinks it might also be possible to make beautiful-sounding acoustic guitars from trees that aren’t under any logging pressure at all.
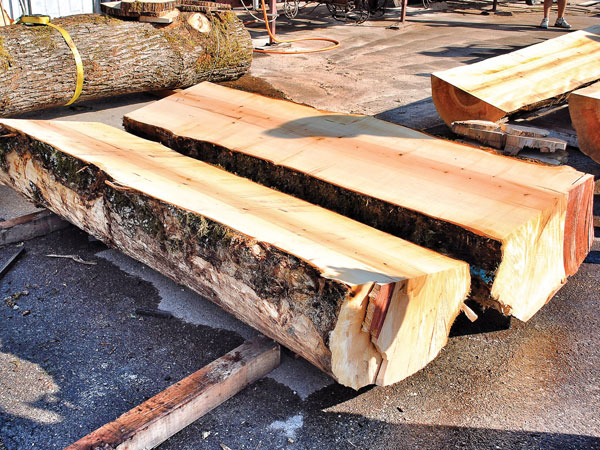
Make it with maple
Take maple, for example. In the Cascade Mountains of the Pacific Northwest of the United States, maple suitable for making guitars grows "like a weed" to quote Steve McMinn, founder of Pacific Rim Tonewoods, a forward-thinking company that provides sustainable timber to many top guitar makers, including Taylor.
It’s plentiful, not in much demand and grows all the way from California to Alaska, right on the back door of many revered guitar firms. The only trouble is, nobody quite believes you can make a good, all-round acoustic guitar from it. Taylor’s innovative master luthier, Andy Powers, explains the problem:
"In this case, I’ve treated maple more like I would if it were being used in a violin or an archtop guitar" - Andy Powers
"Maple has been, in a way, a ‘side dish’ kind of wood in the guitar world," he says. "In the past, you might see a maple jumbo: a big, boomy guitar that could work with a real bright, stiff-sounding wood. Well, that can be a fun maple guitar but it’s the only one that’s really ‘stuck’ and become accepted among players.
"I feel that’s because we’ve traditionally done the same things to maple that we would do with a rosewood or a mahogany guitar - and that’s not fair. Maple has its own personality. I’m not going to cook a steak the same way I cook a piece of salmon - they’re two different ingredients and you have to treat them in ways that suit their personalities."
It was the perception that acoustics with maple backs and sides must always sound stiff and bright that Andy most wanted to challenge with Taylor’s new 600 Series guitars, so he altered their internal design to allow maple to exhibit warmer, more balanced tones.
"In this case, I’ve treated maple more like I would if it were being used in a violin or an archtop guitar," he says. "One of the most notable details in this design is that if you look on the inside, the back braces don’t extend all the way to the rim of the instrument.
"That’s a critical point in these guitars. By doing this, I can help control the back of a maple guitar and allow it to move more like an archtop guitar. Out of these instruments, you’re not going to hear the same bright, almost nasal quality that a lot of us associate with maple flatop guitars."
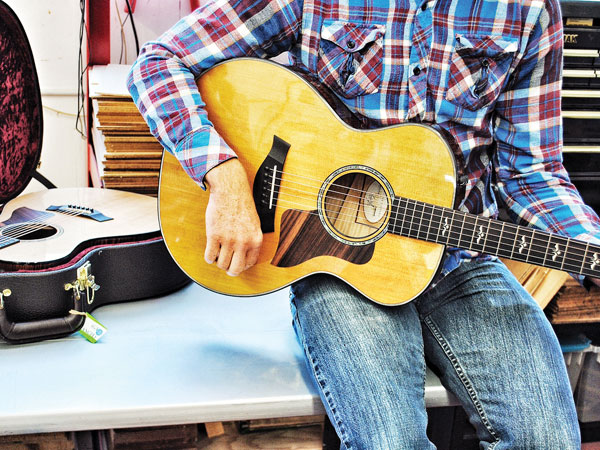
Going dark
Nonetheless, if you look at a typical maple acoustic guitar, with its shimmering blonde sides, it’s difficult not to think ‘bright’. It even looks trebly. So, even if you do succeed in designing acoustic guitars made of maple that sound well-balanced, open and warm, how do you convince people to give them a try?
"Less well-known is that not all ebony trees yield timber that is pure black. Many contain beautifully patterned wood with swirling amber and coffee-cream tints"
"Make them brown. Make them not so bright-sounding and make more of them," is Bob Taylor’s blunt assessment. Bob and co-founder Kurt Listug established Taylor Guitars in 1974. Now, 40 years on, he’s convinced that if guitar makers don’t become less dependent on a narrow selection of tropical hardwoods, the future won’t be very bright for conservation or guitar-making.
Half the battle, he argues, is in challenging players’ preconceptions. He cites the example of ebony: a scarce, slow-growing tropical hardwood that became a byword for the colour black itself in the 20th century due to its use on piano keys, among other things.
Less well-known is that not all ebony trees yield timber that is pure black. Many contain beautifully patterned wood with swirling amber and coffee-cream tints.
But because we all grew up expecting ebony to be a pure, deep black, that’s what most instrument makers have continued to use.
The only trouble is, you can’t tell which shade of ebony you’re going to get until you chop a tree down - often with the result that centuries-old trees were being felled, only for timber to be left to rot on the forest floor because it turned out not to be sufficiently black in hue, though otherwise perfectly suitable as tonewood.
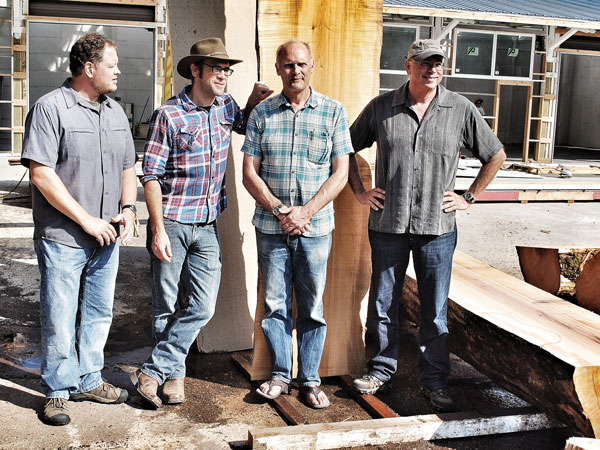
Sustainable ebony
So, instead of rejecting the lighter ebony, Taylor started making guitars with it, setting up its own sustainable ebony operation in Cameroon.
"We found that all we had to do is tell people that ebony doesn’t come pure black; that we didn’t want to throw away brown ebony and that we’re going to start using it," Bob Taylor explains.
"Having worked on players’ perceptions of ebony, Bob Taylor would like to do the same for maple"
"And customers would say ‘Nobody told us this before. But we’re happy to use that ebony’. And, in fact, we’ve seen a huge swing - it’s amazing the number of people who ask us for that now."
Having worked on players’ perceptions of ebony, Bob Taylor would like to do the same for maple - though in this case giving the maple backs and sides on the new 600 Series guitars a translucent auburn ‘Brown Sugar’ stain is the solution.
It seems that ‘dark wood’ equates to ‘darker tone’ for many of us, regardless of what our ears are hearing. So the new maple Taylor guitars not only sound well-balanced but look that way, too. Appearance, as it’s often said, counts for a lot.
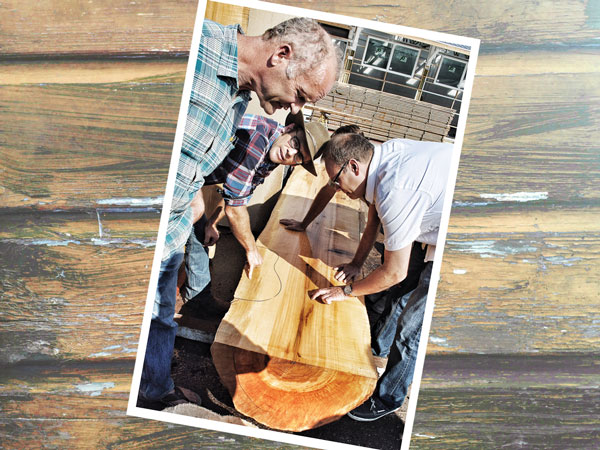
Popular figure
Which leads us to the second of Taylor’s problems. When maple is used on a guitar, most players like it to have attractive figuring. Steve McMinn, of Pacific Rim, explains the quandary:
"You can make a good guitar without figure; you can make it from just plain maple. But guess what? We all like to be charmed. All the same, it’s hard to find the maple tree that has figure in it. We are in the midst of a great forest where there’s a lot of it. But it is often found as by-catch [timber located while logging for other species of tree].
"It’s still a real challenge to get figured maple - but we have a couple of different strategies for that" - Steve McMinn
"So, usually, we’re able to find some in an area where alder and other hardwoods are growing. It’s still a real challenge to get it, though - but we have a couple of different strategies for that.
"One of them is, we’ll go to a big mill and look through their piles. And that works. We get some there and we pay them three times what they paid for it. But the problem with that is it’s often baked in the sun. This is fish country, so we know fish, and there’s one salmon called a pink, or a ‘humpy’, that starts to deteriorate almost in front of your eyes after you’ve caught it. And maple’s kind of that way, too. The sugars will turn colour and it will change."
Steve is working closely with Taylor on the new 600 Series guitars, and agrees that Western Big Leaf maple has good potential as a sustainable tonewood. But finding figured timber in tip-top condition remains challenging. Like ebony trees, it’s extremely difficult to find out if a maple tree will yield figured wood without cutting it down.
"We buy really nice alder logs and sell them to veneer slicers in the Midwest. But in the course of that, we go into the woods, and we see what’s being cut and get hold of [chance finds of figured maple] early.
"And then the third strategy is, it just comes to us. When you start paying enough for it, people will bring it in on a boat trailer or the back of a pickup or something. So we get a little bit that way as well."
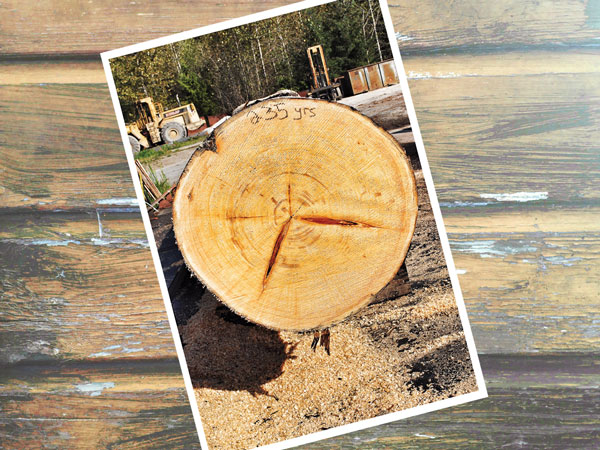
Clone theory
But although these methods will suffice for building maple guitars in relatively modest numbers, Taylor has big ambitions for using maple as a sustainable tonewood for acoustic guitars in the future, as Bob Taylor explains:
"At Taylor now, we design everything for the future. If there’s not a sustainable component or a sustainable reason for the choices that we’re making, then we feel like we’ve missed the mark. Not all the guitars are maple, but more need to be maple. And it’s a long, long game we’re talking about."
"Finding attractively figured maple is, currently, a needle-in-a-haystack job - yet building maple acoustic guitars in really large numbers will require lots of it"
The bottleneck is obvious. Finding attractively figured maple is, currently, a needle-in-a-haystack job - yet building maple acoustic guitars in really large numbers will require lots of it.
So Steve McMinn of Pacific Rim Tonewoods approached Professor Jim Mattsson at Simon Fraser University in Vancouver, who is a specialist in tree genetics. Their goal was to find a way to grow trees that will reliably yield figured maple.
The answer they’ve turned to is cloning. Although it sounds like the stuff of sinister science-fiction, plants have been cloned by farmers for the past 10,000 years - all the bananas we eat, for example, are clones, because they have been cultured over generations to contain lots of edible fruit but no seeds.
But, without seeds, how do you get more bananas? At the most basic level, all you need to do is take a cutting from a healthy plant, relocate it to a fertile environment where it can develop roots of its own, and then nurture it to maturity.
Genetically identical to the plant it was taken from, it will likely have the same characteristics as the donor plant, including - in the case of certain maple trees - a predisposition towards figuring.
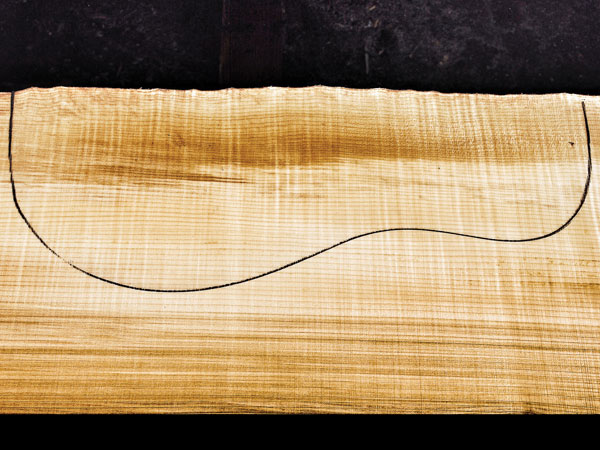
A growing trade
Just to be clear, this is not the same as genetically modifying plants, which involves directly altering the DNA of an organism in the laboratory. Instead, it’s more like taking a chip off the old block, as Professor Mattsson explains.
"It’s very similar to what your grandmother might do with an African Violet. You cut off the leaves, stick them in moist soil, you wait for a while and it will make roots. It’s a little bit more tricky in maple, though."
"There’s a tremendous amount known about Western Maple - but only how to kill it or get rid of it, because it’s regarded as a weed [by loggers]" - Steve McMinn
Professor Mattsson’s team take cuttings from maple trees known to possess good figuring, and these are carefully grown on under sterile lab conditions. At a certain height, further cuttings are taken from these young plants, from which yet more cloned plants can be grown.
Finally, the cloned saplings are introduced to soil, where they will mature into fully grown trees over a number of years. As they grow, the university team will examine tissue samples from their twigs to determine if the clones are developing figuring like the original donor tree. Along the way, they’ll be gathering scientific insights into why maple has figuring at all.
"We think it is due to defective transport of a plant hormone that is very important for keeping things straight," says Professor Mattsson. "When the cells divide, they should elongate and they should be straight. Here, we have cells that elongate - but they wiggle on the way."
"This is an interesting project, because there’s a tremendous amount known about Western Maple - but only how to kill it or get rid of it, because it’s regarded as a weed [by loggers] who are after alder or douglas fir," adds McMinn, "But we don’t yet know much about how to grow it."
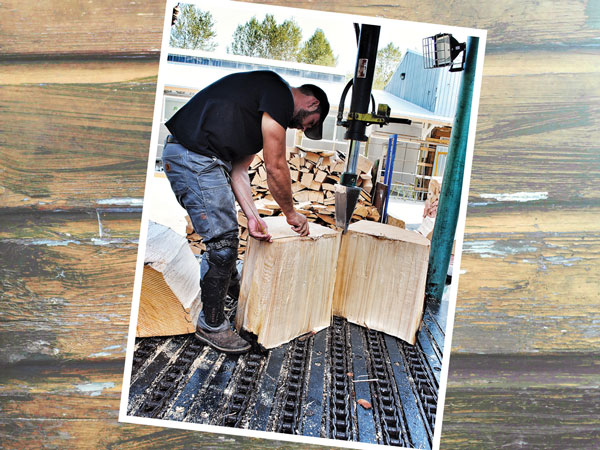
Pioneering project
But isn’t it a worry that figured maple that’s been cloned will all look the same? Professor Mattsson argues that, due to environmental factors, each cloned tree will each grow in a different way and produce quite different types of figuring - or even none at all.
"It’s not a given that if Steve finds a tree and we bring it to the lab, we clone it, put it in a nice field, that it will produce the same phenotype [figuring]," he says. Bob Taylor continues:
"The end goal is your kids, or maybe your grandkids, will be living in a world where more people play maple guitars" - Bob Taylor
"What we’re trying to do is get more trees that have figure. But there’s going to be variation because one of them is going to be blown in the wind and one of them is going to be behind the one that’s blowing in the wind, one of them is going to get more sun while another will be in the shade, and so on. Also, we might end up with 20 different ‘mother’ trees, so you would have a lot of variation."
Although the project is in its infancy, everyone involved hopes it will one day provide a lifeline of sustainable, figured tonewood that will relieve pressure on tropical forests decimated by uncontrolled logging.
To get even this far has required a fresh look at guitar design, pioneering science, extensive teamwork between companies and acceptance that achieving a sea-change in players’ use of maple guitars might take decades, with no absolute guarantee of success. All the same, Bob Taylor thinks it’s worth shooting for.
"The end goal is your kids, or maybe your grandkids, will be living in a world where more people play maple guitars.
"They like them, they’re used to them, they like the sound of them - and the whole industry has developed, from the laboratory to the sawmill, to the musician, to the factory, to the marketing - the whole thing - to where the world doesn’t even think twice about it. Because they just buy a maple guitar."
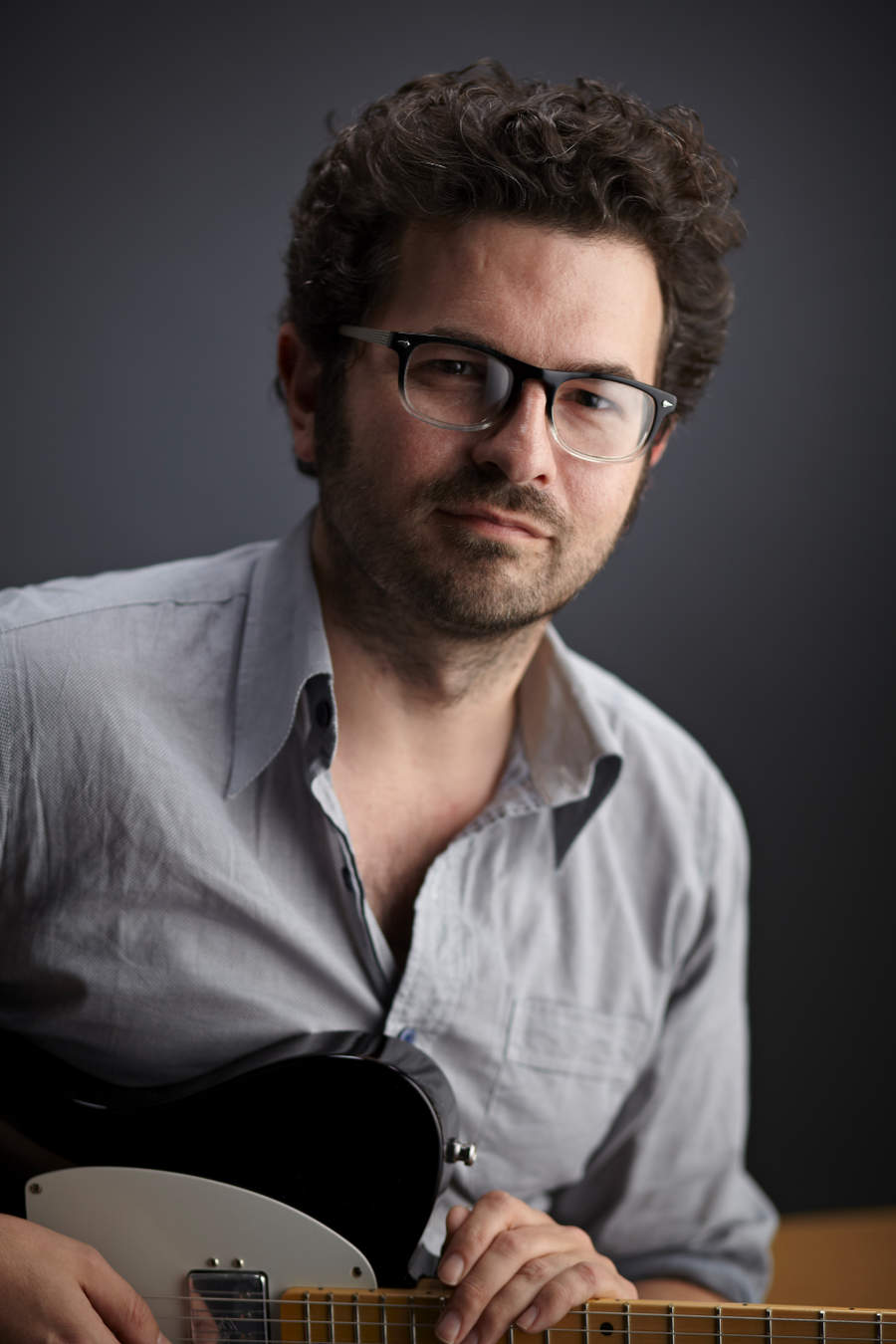
Jamie Dickson is Editor-in-Chief of Guitarist magazine, Britain's best-selling and longest-running monthly for guitar players. He started his career at the Daily Telegraph in London, where his first assignment was interviewing blue-eyed soul legend Robert Palmer, going on to become a full-time author on music, writing for benchmark references such as 1001 Albums You Must Hear Before You Die and Dorling Kindersley's How To Play Guitar Step By Step. He joined Guitarist in 2011 and since then it has been his privilege to interview everyone from B.B. King to St. Vincent for Guitarist's readers, while sharing insights into scores of historic guitars, from Rory Gallagher's '61 Strat to the first Martin D-28 ever made.