Inside the workshop: Orange Amps' Adrian Emsley
Poke around the amp designer's playground!
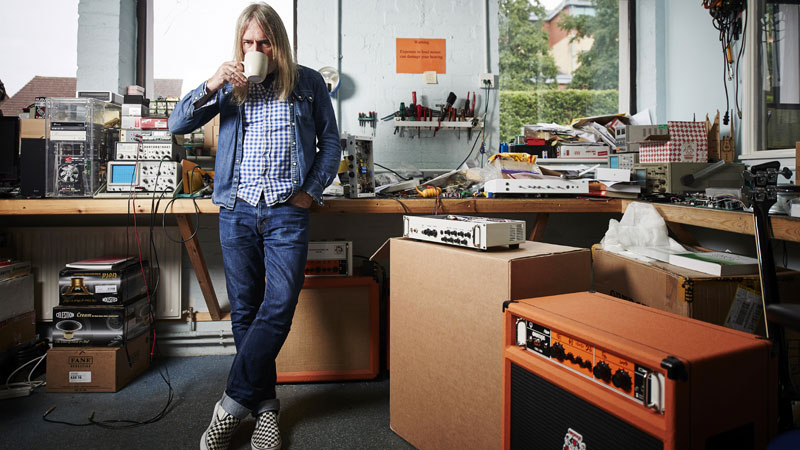
Introduction
Adrian Emsley is Orange’s amp-design wizard. We take a look round his R&D workshop to find out how solder, instinct and software help him conjure up stunning tone…
It takes a special sort of engineer to build a great guitar amplifier. They must have a sure scientific knowledge of circuit design - but also a great set of ears and a certain gut feel for what will sound great. And, as if that isn’t enough, they need to be gigging guitarists, too, so they understand what players want from amps and pedals and how they can build pro-grade amps to survive the road.
Adrian Emsley of Orange is the walking, riffing embodiment of all those virtues and it shows in the line of hellacious-sounding and thoughtful amp designs he’s worked on, from the brutal Rockerverb MKIII to quality entry-level combos such as the Orange Crush 35RT.
I never design by committee. I just think. ‘What would be a good amp for Orange to have at this moment in time?’
As he ushers us into his lair, Orange’s R&D workshop in Hertfordshire, he explains that solder runs in his veins, so to speak.
“My dad actually taught me the basics of electronics and fixing valve stuff when I was a kid,” he says. “So I was kind of brought up with valves. I started off modding guitar amps back in the 80s, primarily to get more gain. And then I went into restoring vintage pieces - getting them back to their original condition in terms of components… then just got into building one-off pieces for players and then just started working for Orange, really.”
According to Adrian, the R&D process behind building a new Orange amplifier, whether it’s a high-end hand-wired head or an entry-level combo, is a blend of engineering rigour and instinct, ultimately based on experience.
“I just follow my gut, he says. “I never design by committee. I just think. ‘What would be a good amp for Orange to have at this moment in time?’ And I’ll set about building a point-to-point prototype of it once I’ve got the topology in my head of what I’m going to do, then I’ll shoot all the bugs in the circuit at that stage, so it’ll be fully working.
“And then I’ll try to lay out a PCB that sounds as close to that as possible. But sometimes it won’t be on a PCB, even, when it goes into production: sometimes, it’ll be a point-to-point model, in which case we just get the factory to copy the prototype.”
So what are the most important elements of good amp design, in his view?
“Start off with good transformers and a good circuit design,” he says. “PCB layout is a fundamental thing. I don’t use any right angles - everything’s curved, because it sounds better. We use two-ounce copper instead of one-ounce on the UK-built stuff, too.
“When the lead-free [solder] legislation came in about 10 years ago, that helped serviceability and it actually sounded better. But transformers are the heart of the amp: if you’ve got rubbish transformers, it’s never going to be a great amp. It might sound okay in the bedroom, but when you push it, it’s going to blow up, so it’s never going to be a great amp,” he adds.
We try to just make them honest, properly built amps. And then we try to keep making them even better, really
He also has to make careful choices in terms of tone and reliability about which valves to fit in production amps - especially as they’re not always made to a standard, established spec.
“There are some good valves available - although Svetlana closed down a few weeks ago in St Petersburg - and at the moment, the Chinese EL34 is the best one. But it was made wrong for 15 years,” Adrian says.
“What they did was, they wired the cathode via the suppressor grid - so the entire current of the valve was going through the suppressor grid. And there were still certain applications it wouldn’t like. It wouldn’t like to run Class A: stick them in a Matchless and they’d be like frontline soldiers. So, me and a couple of guys identified this and got it fixed. And now they’re really good.”
It’s clear that attention to detail is important, as far as Orange amps and effects go. All the same, fairly simple values underpin the whole enterprise of getting great tone.
“We try to just make them honest, properly built amps,” Adrian concludes. “And then we try to keep making them even better, really.” And with that, he takes us to his workbench to show us the tools of the trade he couldn’t live without...
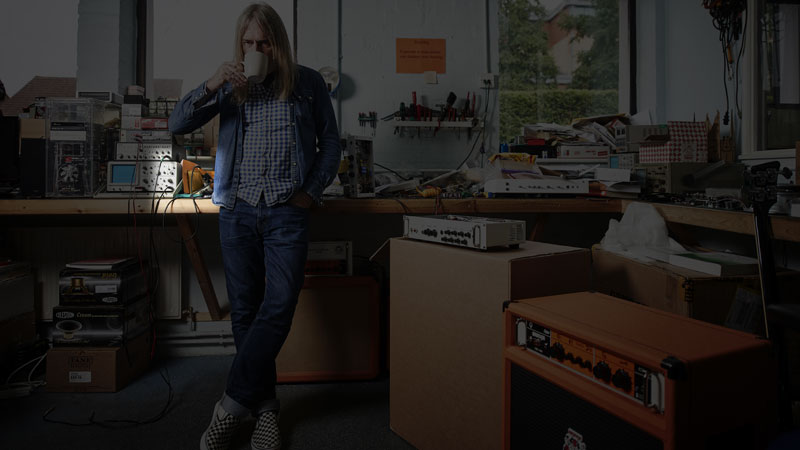
Soldering Iron
“I’ve got a couple of solder stations, one for leaded solder, one for unleaded. I keep them separate so they don’t get inter-contaminated.
If you’re prototyping or doing intricate stuff that might have to be re-worked, there’s no point in using lead-free solder
“The one for unleaded solder runs at a higher temperature. If you’re prototyping or doing intricate stuff that might have to be re-worked, there’s no point in using lead-free solder [as it’s harder to work]. But if you’re building a pre-production amp, it’s got to be leadfree. Or if you’re repairing an amp that was made later than 2006, it’s got to be lead-free as well.
“I use mainly lead-free these days, but having said that, this week, I’ve been using leaded because I’ve been designing discrete op amps, which are very small - and sometimes you want to re-work or change components. And you don’t want to be using leadfree for that, because you’re more likely to lift a pad.”
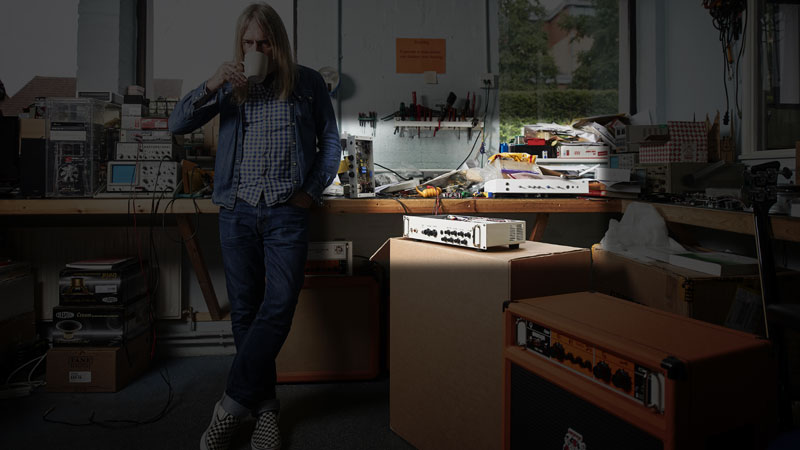
Prototype Amps
“There are always a few prototype amps kicking about that have just been built. We hang on to all of the prototypes after we’ve built them, though.
Ones that aren’t on my shelf behind me are on a pallet in the warehouse, sealed up
“Ones that aren’t on my shelf behind me are on a pallet in the warehouse, sealed up. Occasionally, you’ll have to unwrap that pallet because you’ll think: I need to have another look at this, because it might help you develop an idea. Which is a pain in the arse if it’s been palletised, because it’s, like, 20 feet up in the air!”
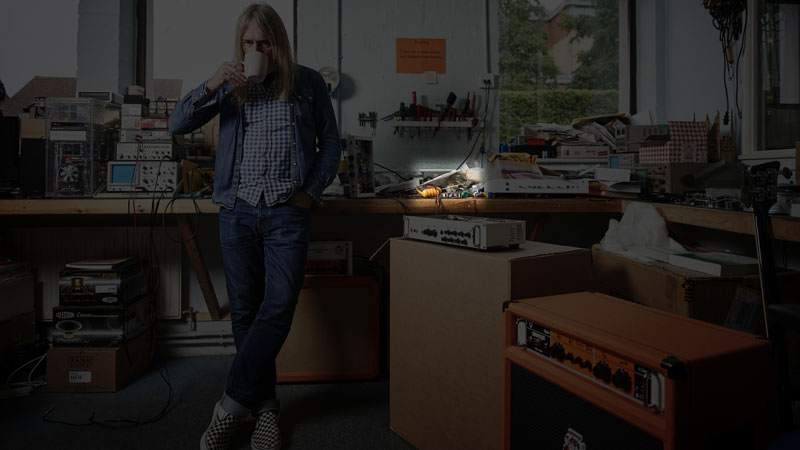
Enamelled Copper Wire
“This is a bit of a tip: enamelled copper wire is a good way of getting components out [that have previously been soldered in place].
“You sort of hook it round and you can remove stuff a lot quicker and less destructively that way. Especially for components you might want to use again: you don’t want to scrape all the enamel off a resistor trying to tear it out with pliers or something.”
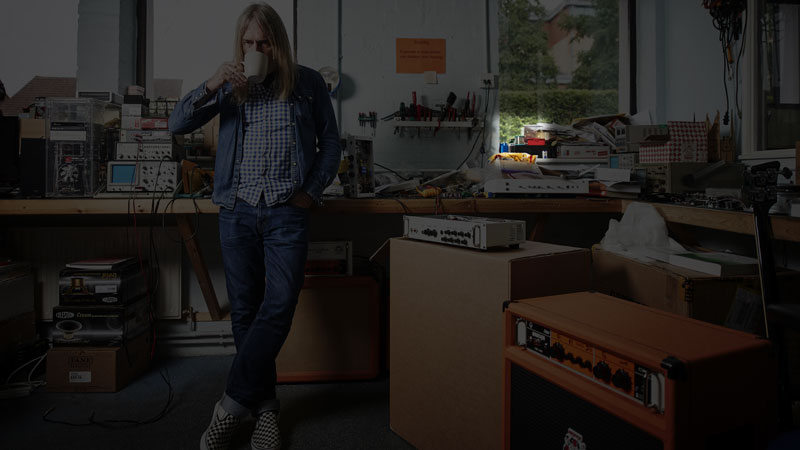
Warton Metals Lead-free Solder
“We use lead-free solder that’s got quite a lot of silver in, and it tends to flow better than most and doesn’t bubble or get honeycombed like a lot of stuff does. We use one from Warton Metals, which is really good.
It’s good to have a service technician go over it with a clean toothbrush occasionally
“It actually gets nice solder joints: it’s harder than the lead stuff and it has a higher melting point, but actually, you can get nicely finished joints on it. The big enemy with lead-free solder is ‘tin whiskers’ [conductive crystalline growths]. There’s not a lot you can do to stop that from happening over a period of time, so you do sometimes have to clean joints.
“It’s good to have a service technician go over it with a clean toothbrush occasionally. But this solder we use is less prone to that than a lot of the stuff out there. When it fi rst came out, lead-free solder was dreadful. It’s taken us a while to fi nd one we like to work with.”
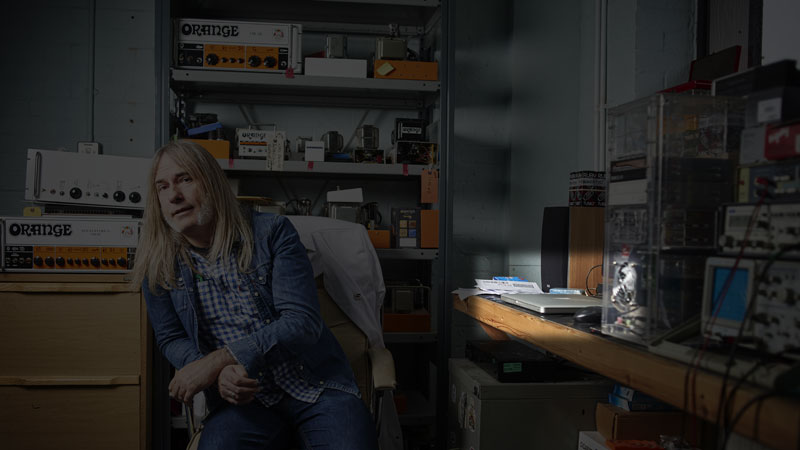
Computer
“I do a lot of stuff on Spice, which saves me a lot of time working out amp topologies and impedances and stuff.
I use Spice circuit-simulation software, so it’s got parameters of components in there and you can build the circuit up quickly
“It’s circuit-simulation software, so it’s got parameters of components in there and you can build the circuit up really quickly in there and then run a ‘current’ through it and so judge all your output levels and impedances.
“I normally do that first. I do a lot of pedals with Spice as well: it’s great for that. I can get things working roughly how I want them, then lay out the pedal’s PCB and go for it, really.
“But with valve amps, it’s always a point-to-point prototype first, because I can change components. And my OCD kicks in, because I don’t want it to look really untidy if I have to change something. I want it to look like it was built like that on purpose!
“With PCB, if you have to do a re-work or totally change something, it’s gonna look bad. So it’s horses for courses, really.”
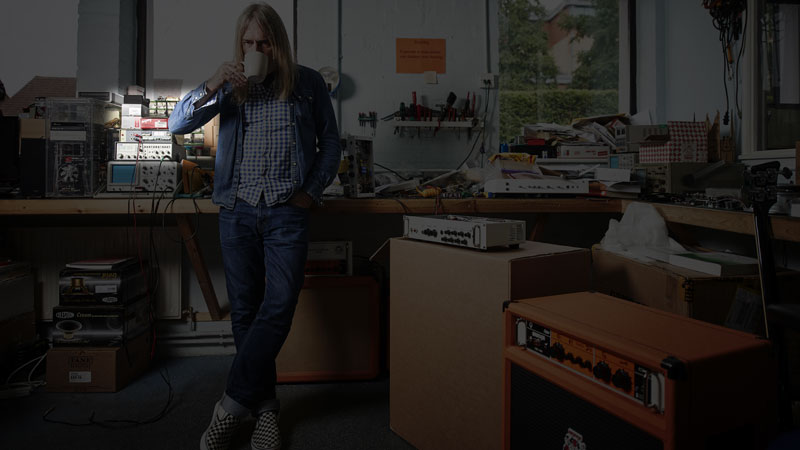
Component Racks
“I’ve got R&D racks that hold various parts: I’ve got pedal racks, racks for amps that use different voltages: there’s stuff for everything.
“My end of the workshop is more of an R&D place but next door, we’ve got the service shop as well.”
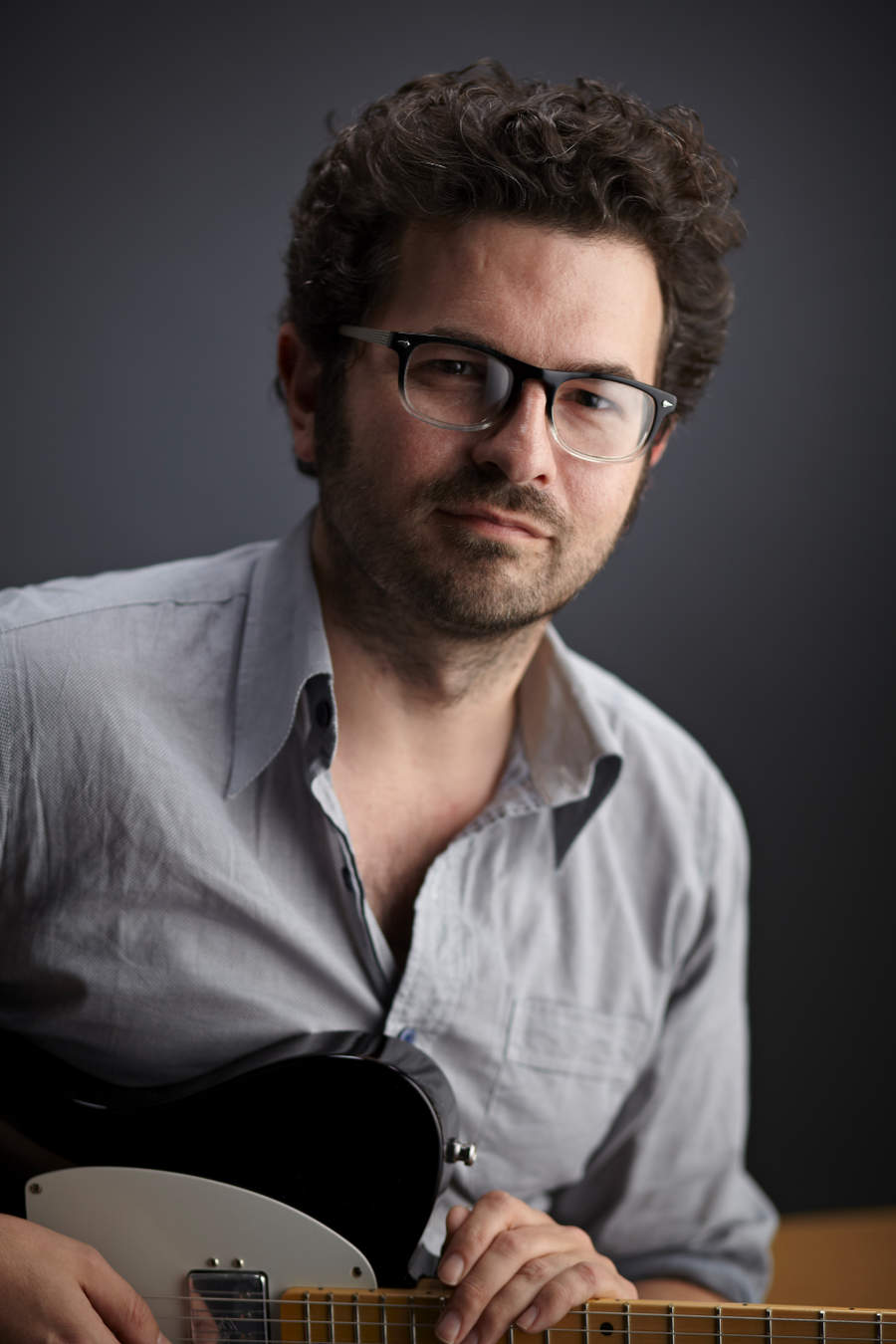
Jamie Dickson is Editor-in-Chief of Guitarist magazine, Britain's best-selling and longest-running monthly for guitar players. He started his career at the Daily Telegraph in London, where his first assignment was interviewing blue-eyed soul legend Robert Palmer, going on to become a full-time author on music, writing for benchmark references such as 1001 Albums You Must Hear Before You Die and Dorling Kindersley's How To Play Guitar Step By Step. He joined Guitarist in 2011 and since then it has been his privilege to interview everyone from B.B. King to St. Vincent for Guitarist's readers, while sharing insights into scores of historic guitars, from Rory Gallagher's '61 Strat to the first Martin D-28 ever made.