In pictures: Warwick & Framus Factory Tour
We take a trip behind the scenes at Warwick HQ
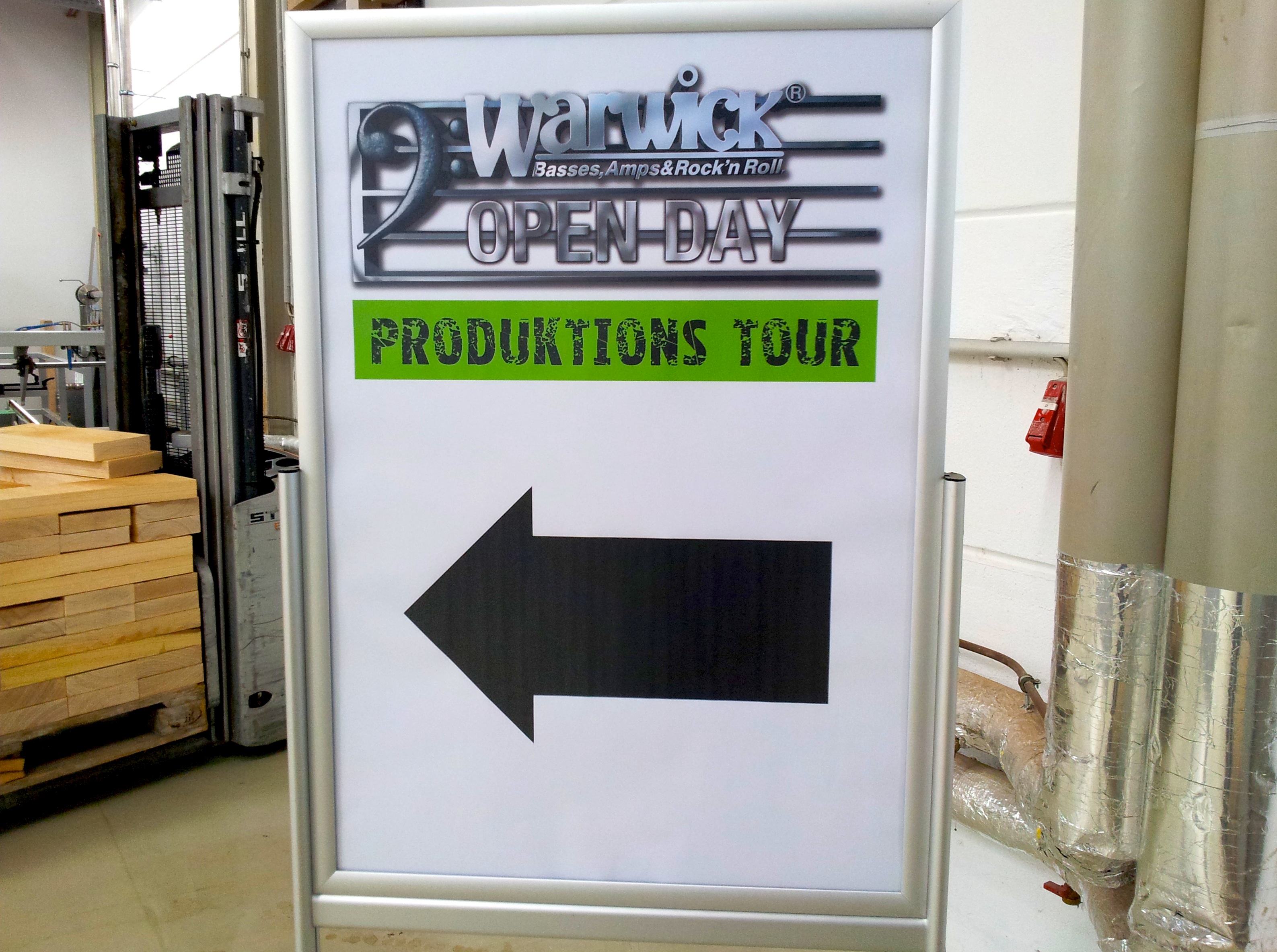
Warwick & Framus Factory Tour
We were beyond thrilled when the guys at Warwick & Framus invited us over to their headquarters in Markneukirchen, Germany, and we took the opportunity to get some undercover snaps of the company’s unique production process.
So, join us as we explore the journey from wood to instrument with our shots of the coolest parts of the process…
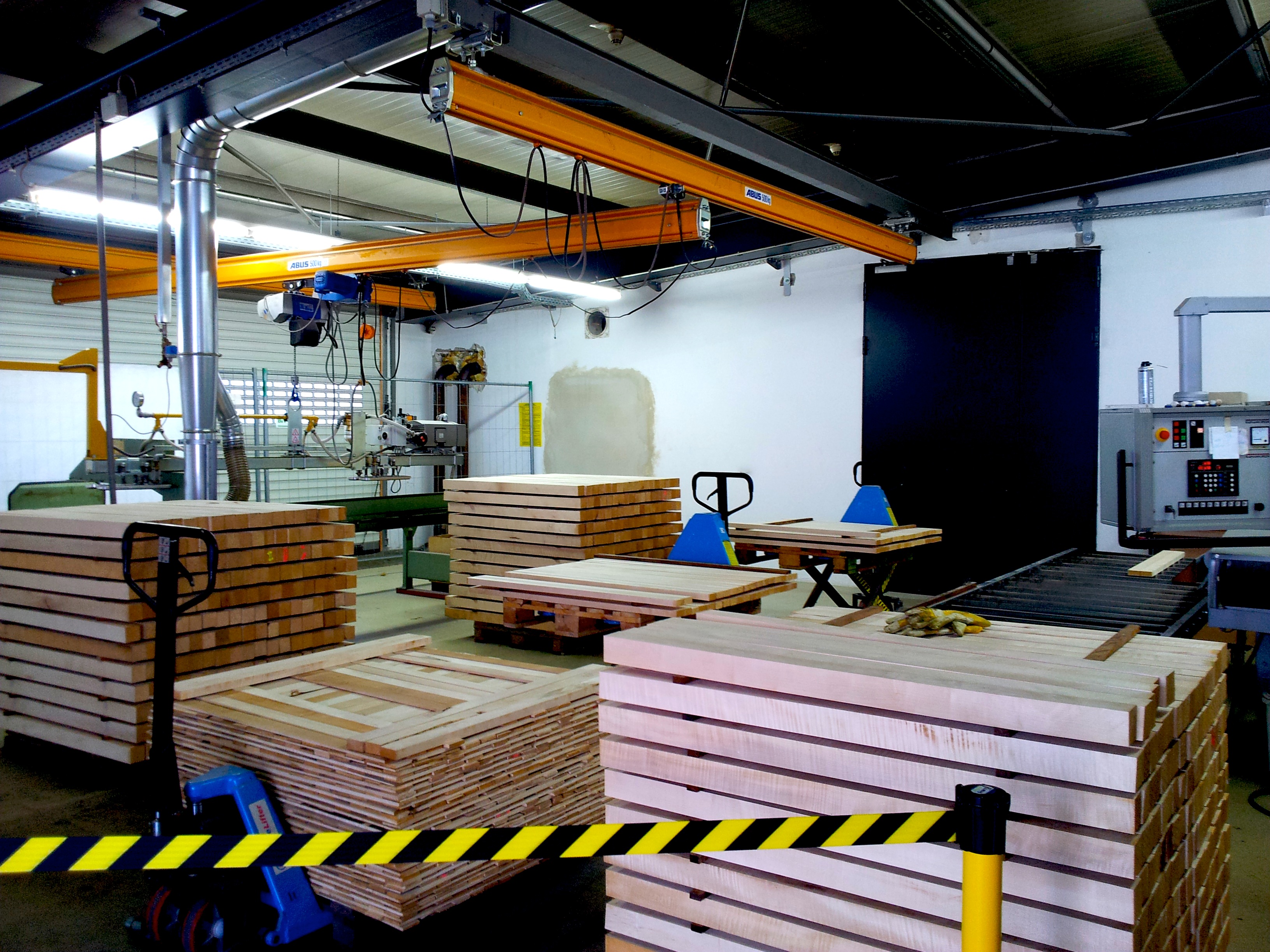
Warwick & Framus Factory Tour
First, the slabs of wood are cut into smaller pieces, then sent to this rip-saw machine, which uses lasers to cut them into more precise sizes
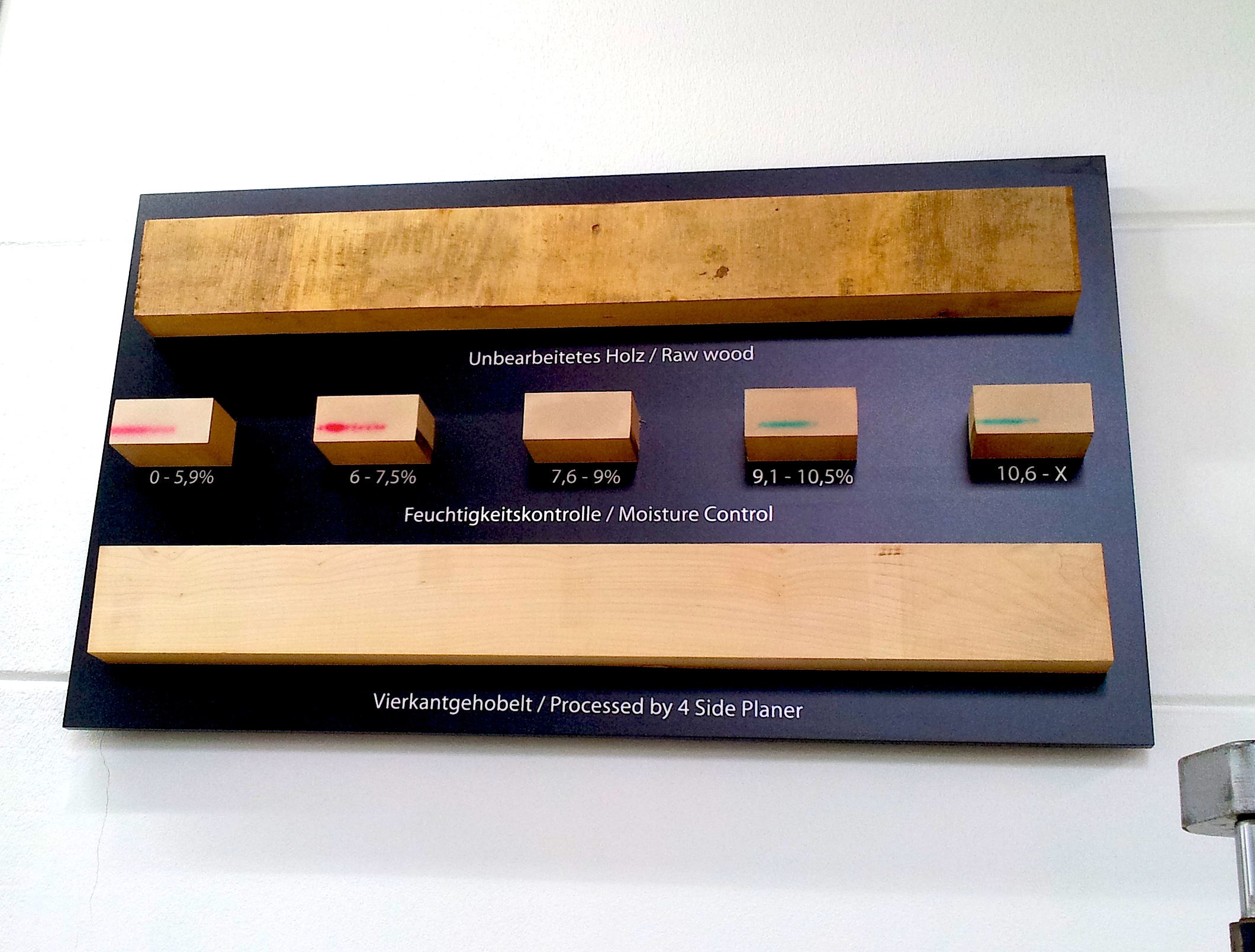
Warwick & Framus Factory Tour
The instrument-proportioned slabs of wood are then taken to the drying chamber, before being checked for moisture
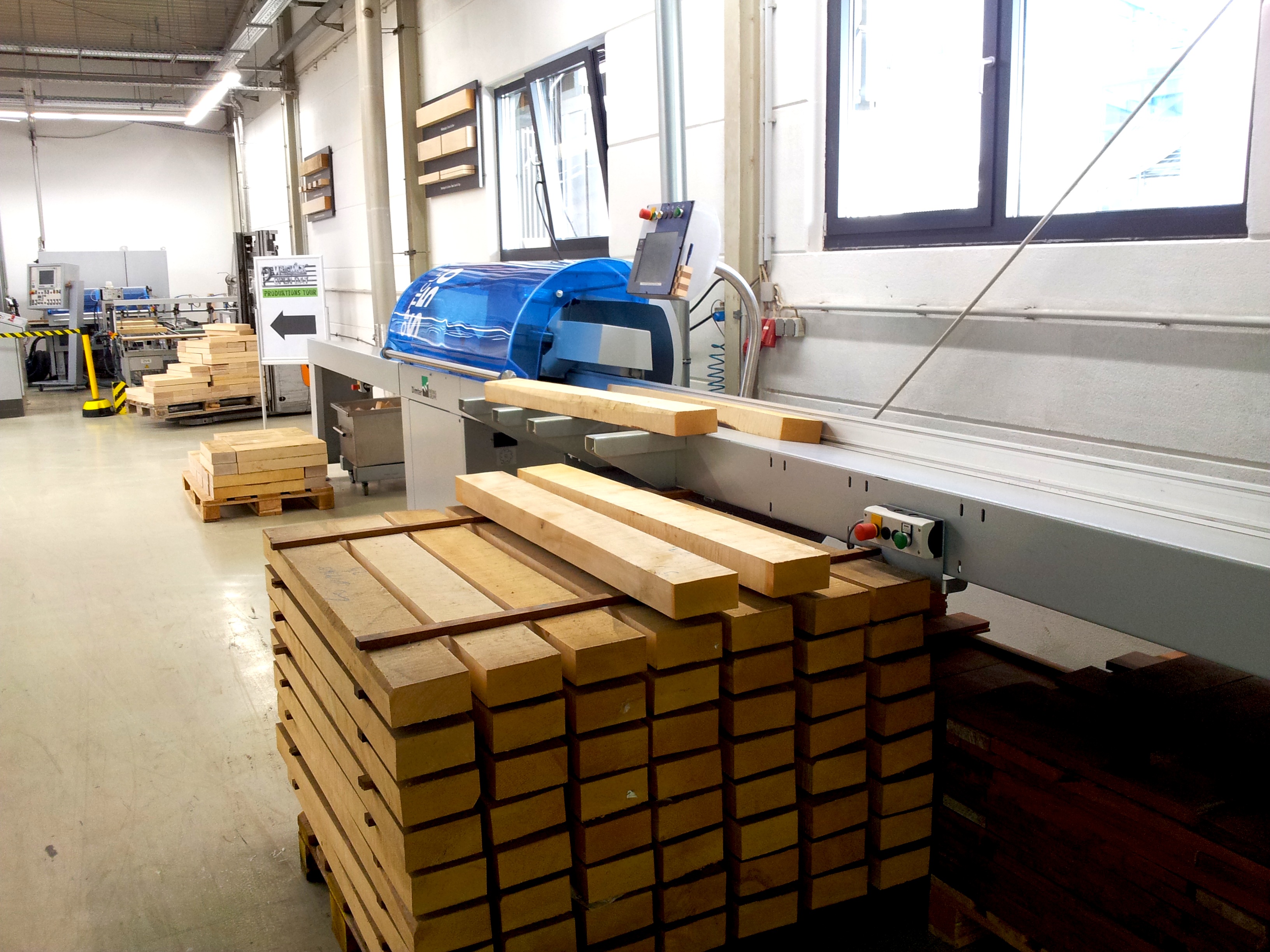
Warwick & Framus Factory Tour
Now, the necks are cut using another of those cutting machines – we’ll see more of those later…
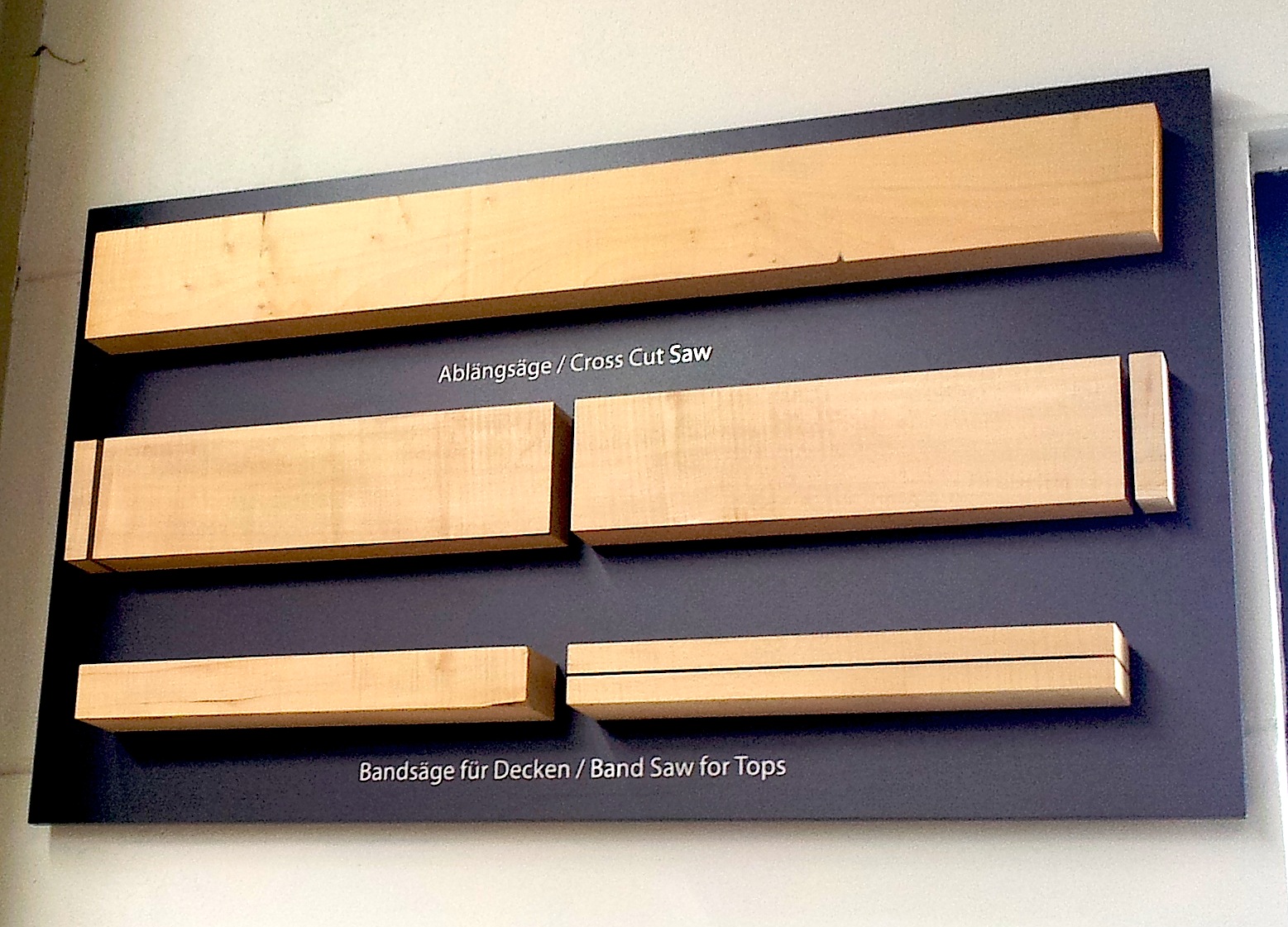
Warwick & Framus Factory Tour
There are different ways of cutting depending on what the wood will be used for – the band saw is used for tops, for example
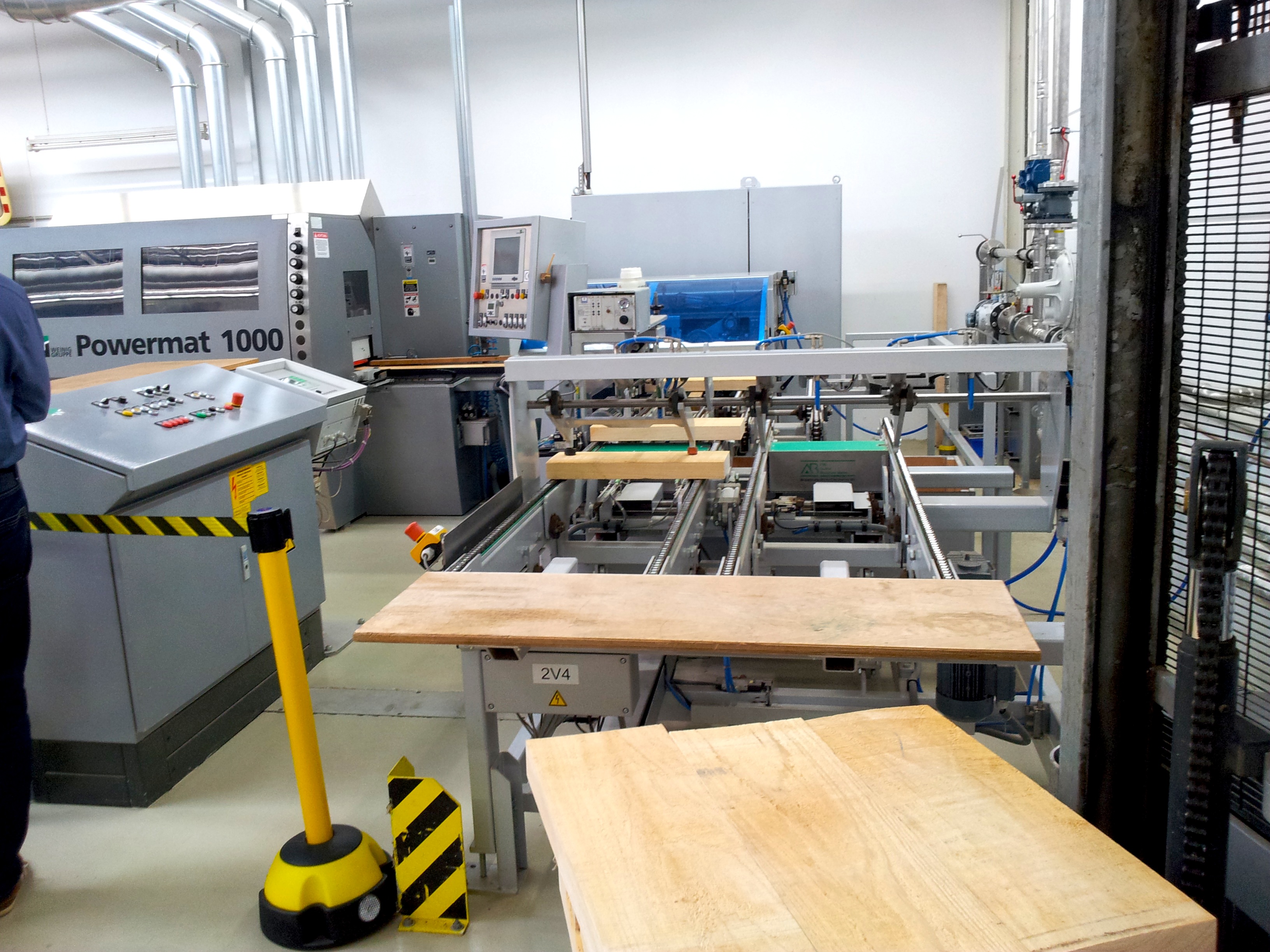
Warwick & Framus Factory Tour
More cross cutting going on over here
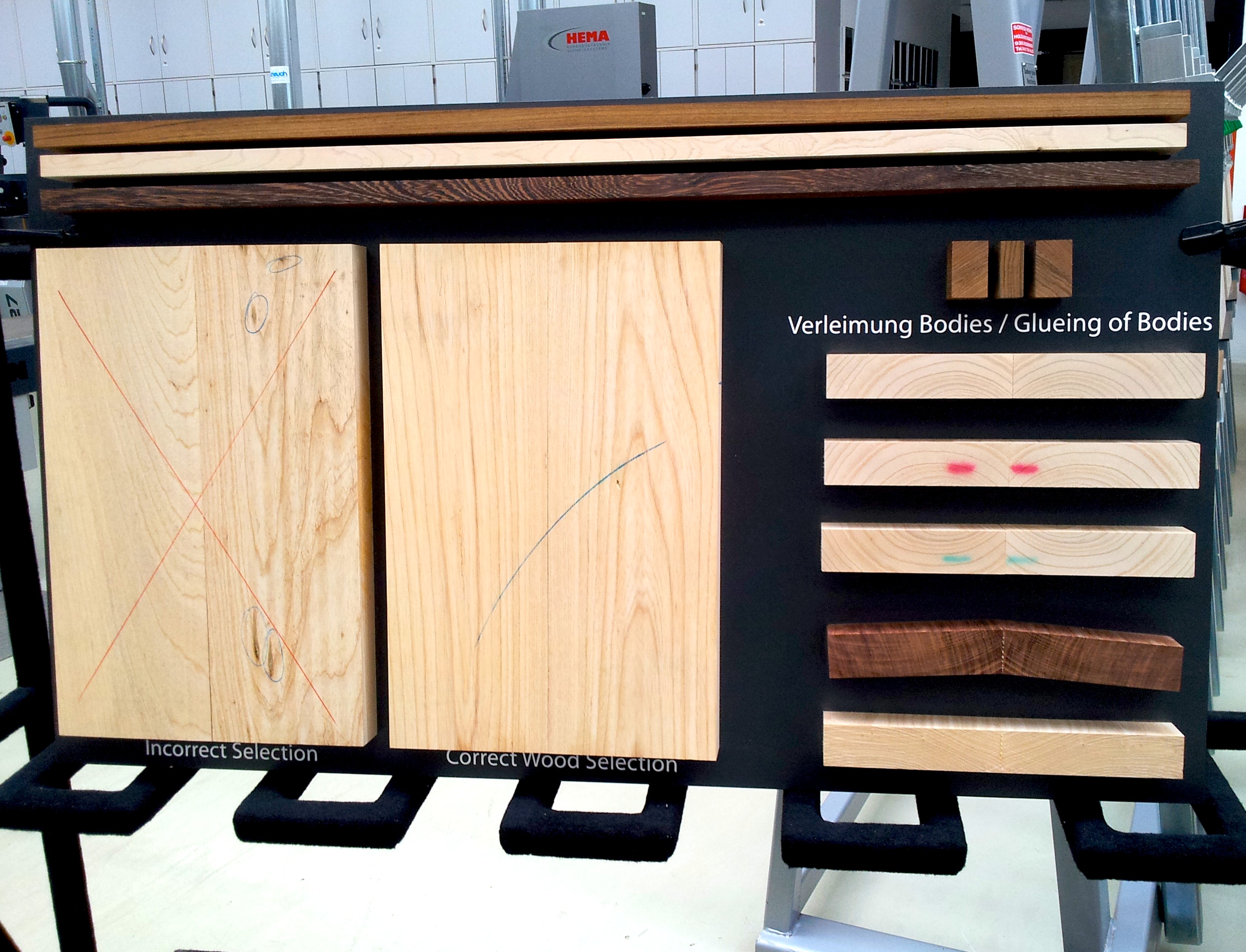
Warwick & Framus Factory Tour
Slabs of wood are hand selected and glued together, based on their wood grain and colour
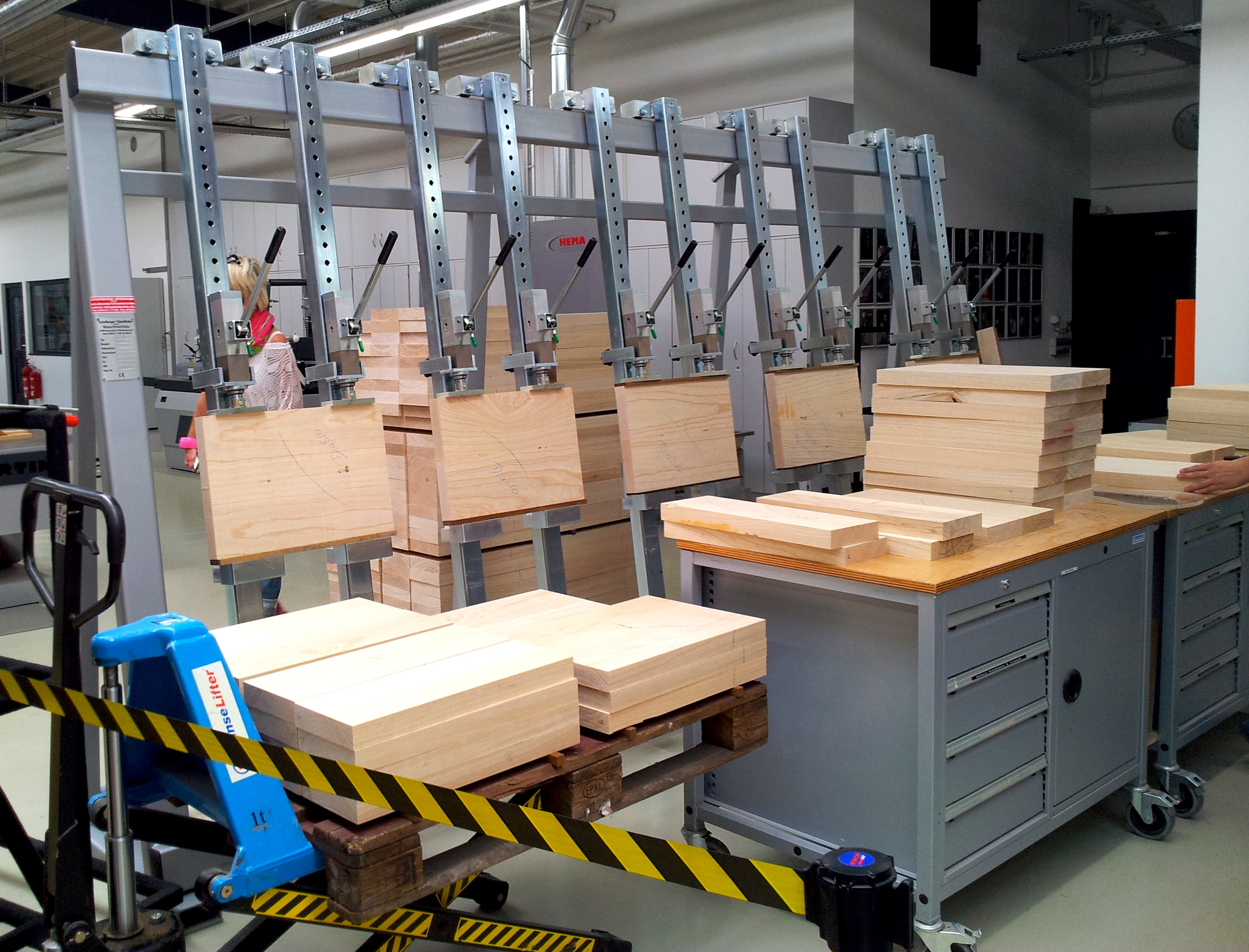
Warwick & Framus Factory Tour
And here’s the gluing in action
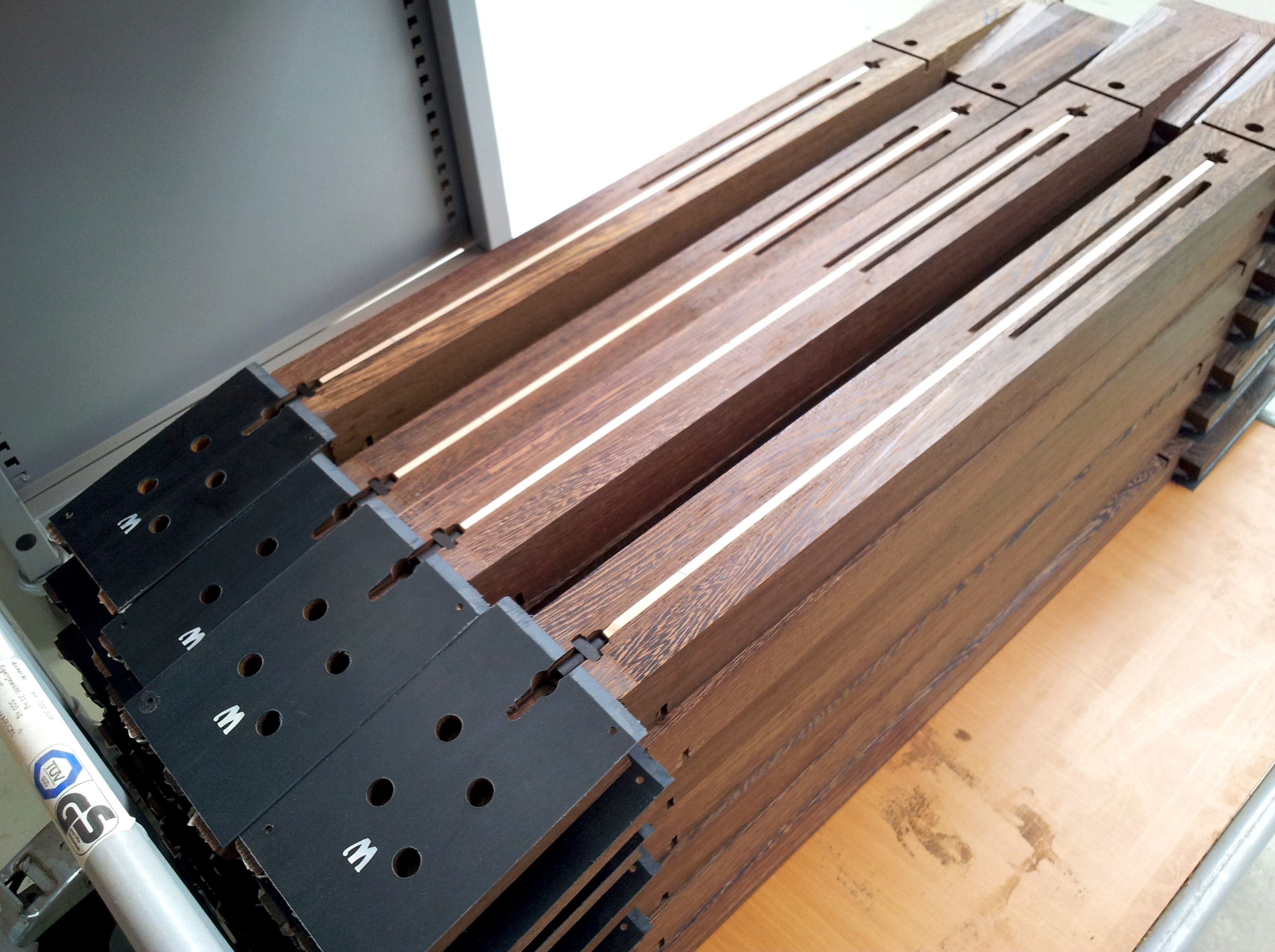
Warwick & Framus Factory Tour
There are those necks again, headstocks attached, and truss rods installed
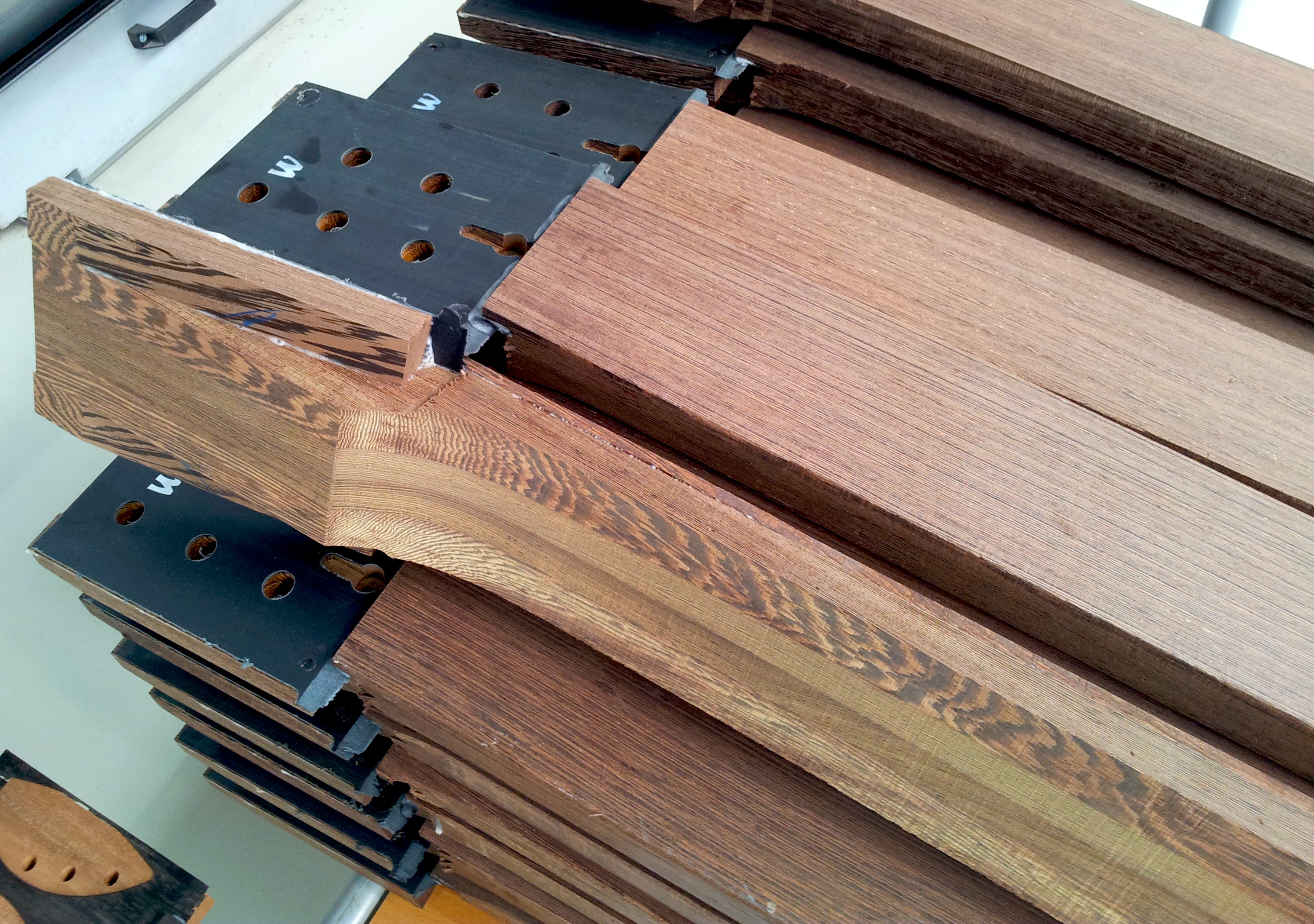
Warwick & Framus Factory Tour
Each of those slabs of wood from earlier gets cut to form two necks, as you can see here
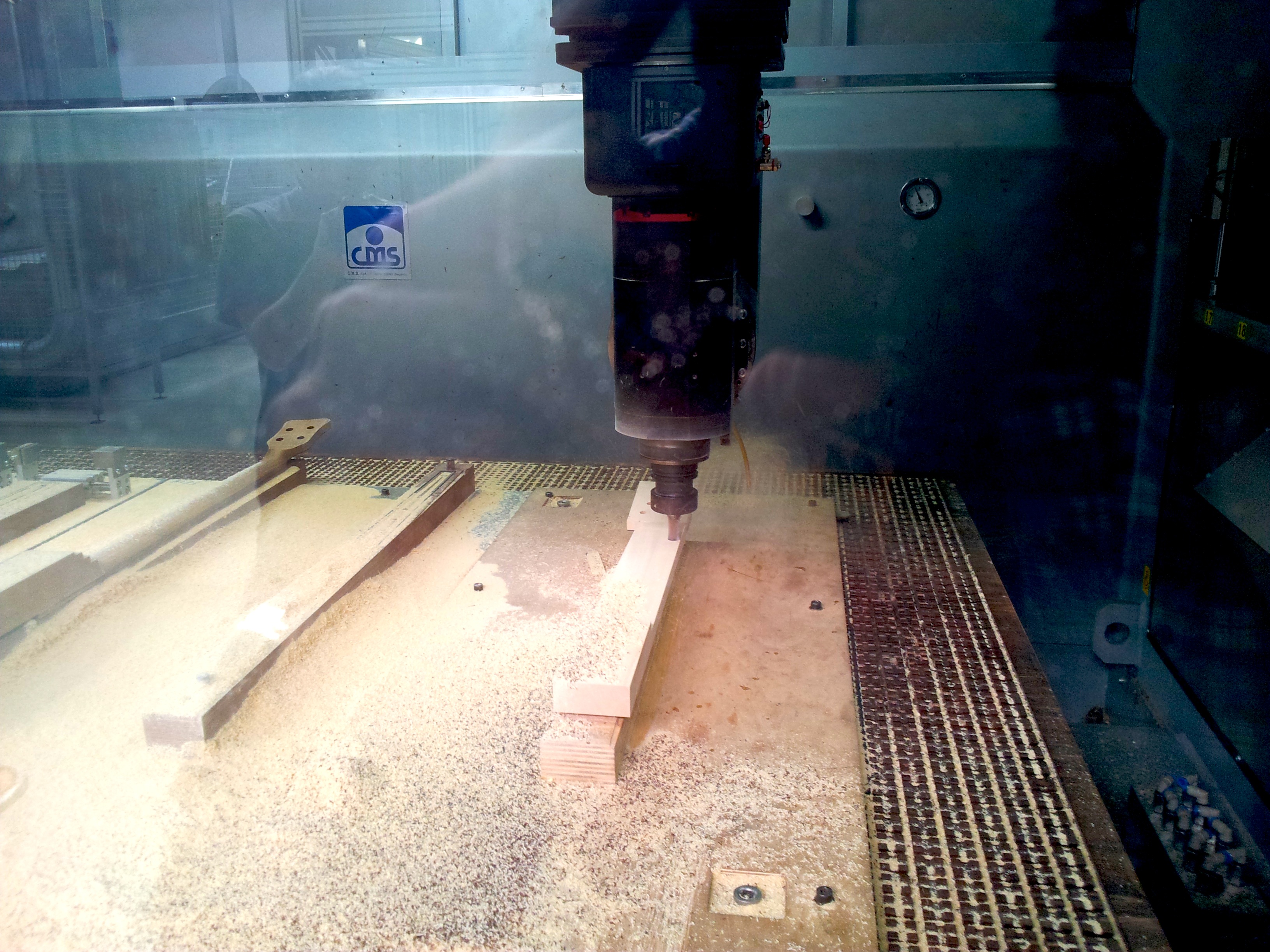
Warwick & Framus Factory Tour
Now, those necks head over to these CNC router machines, which follow a set program to precisely cut the neck and headstock to size…
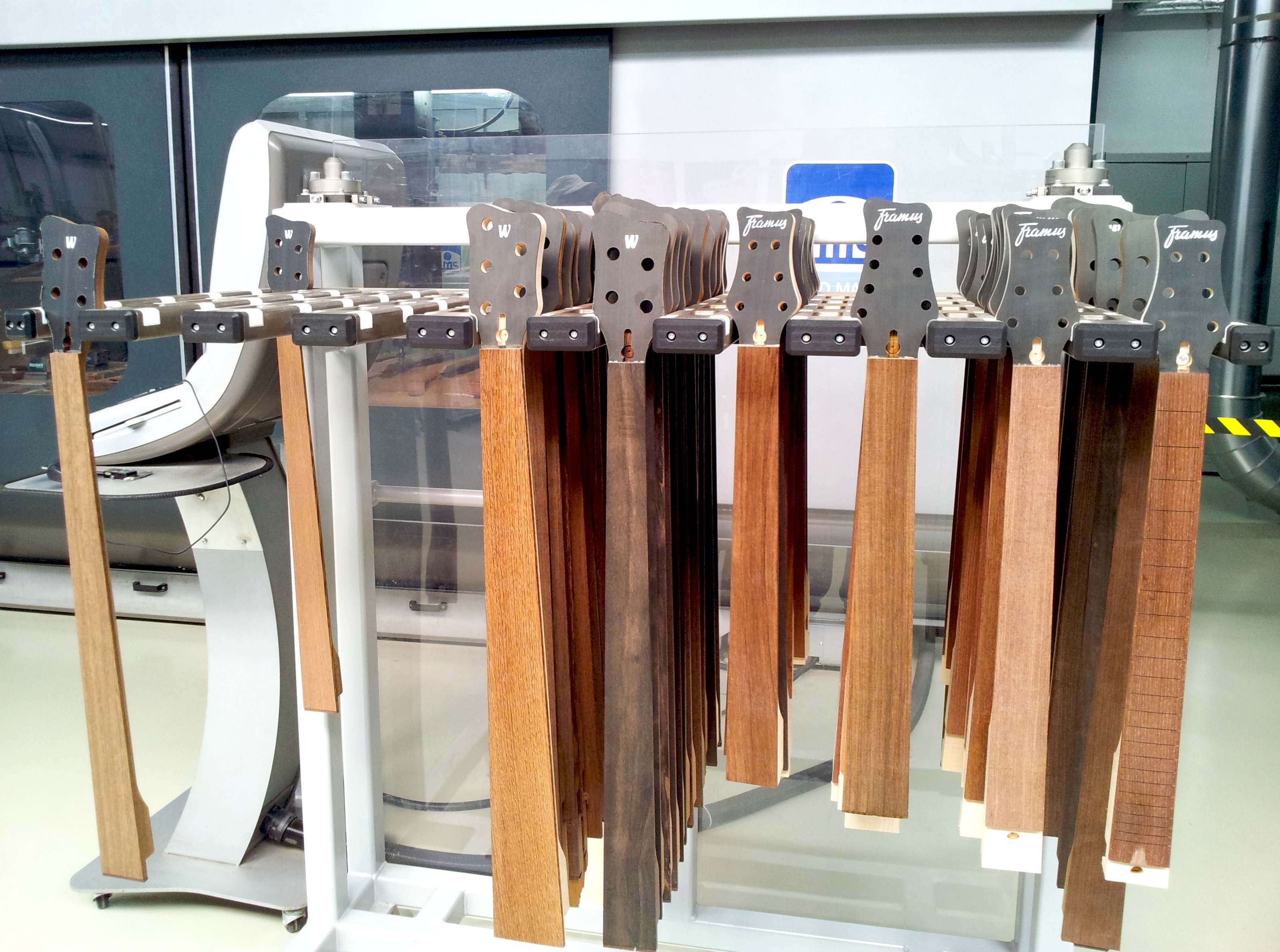
Warwick & Framus Factory Tour
…resulting in the lovely finished Warwick and Framus necks you see here
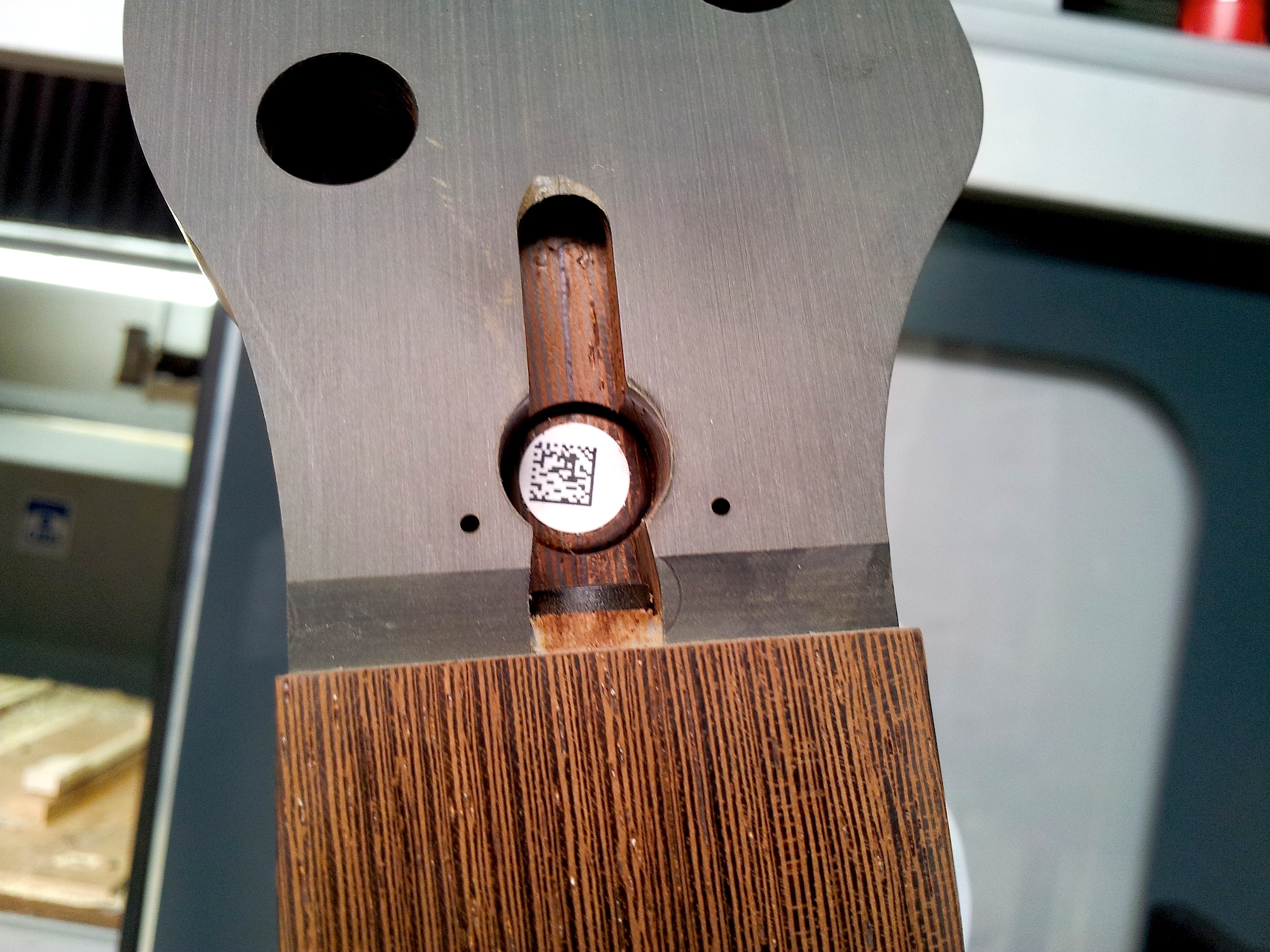
Warwick & Framus Factory Tour
See that lil’ QR code? That tells the next machine exactly what scale and radius the neck has, and what size frets it needs
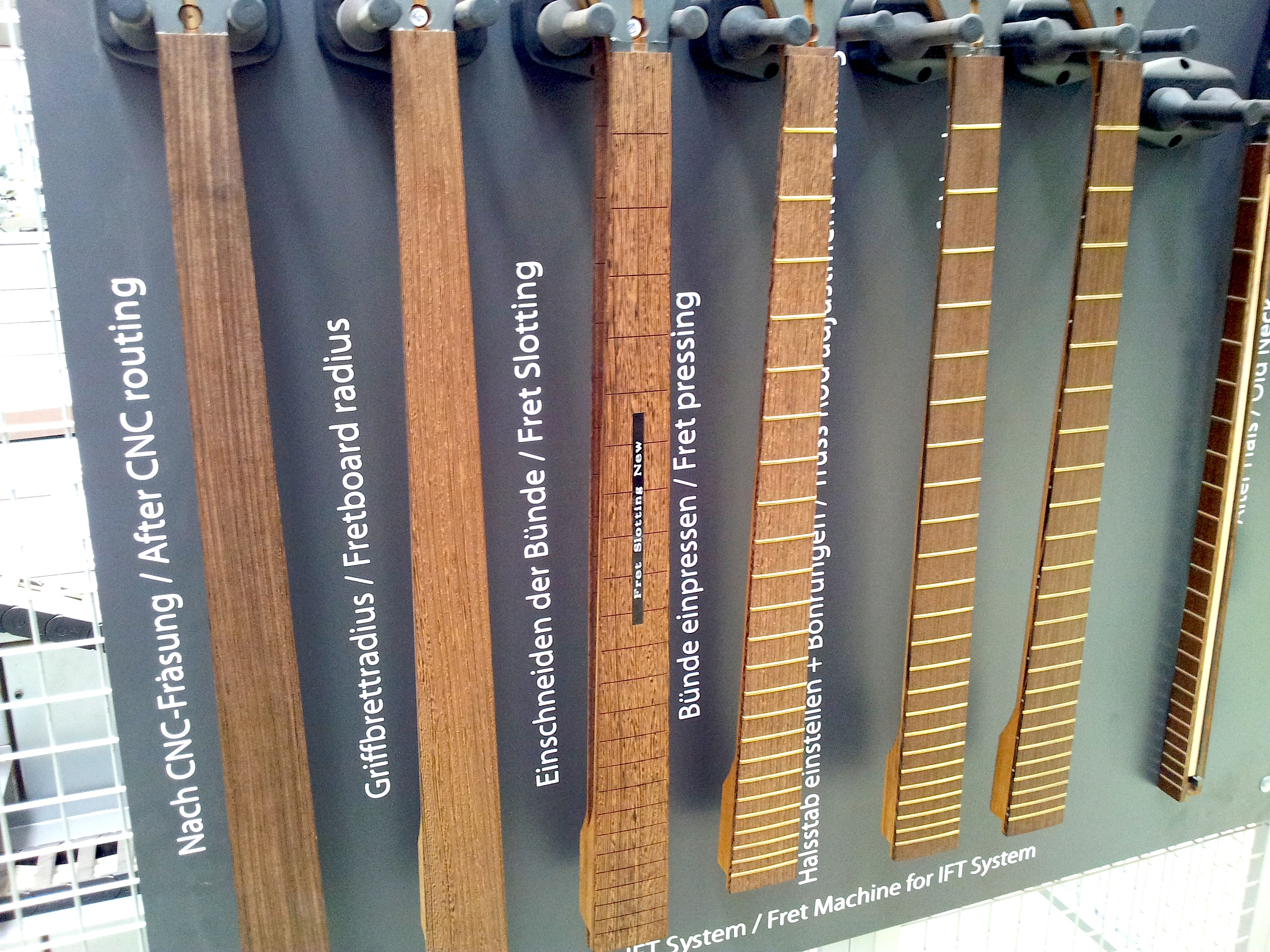
Warwick & Framus Factory Tour
Warwick's Fretboard Processing Unit is the only one in the world, and it handles fretboard radius, fret slotting, fret pressing, truss rod adjustment and drilling, and fret levelling. Phew!
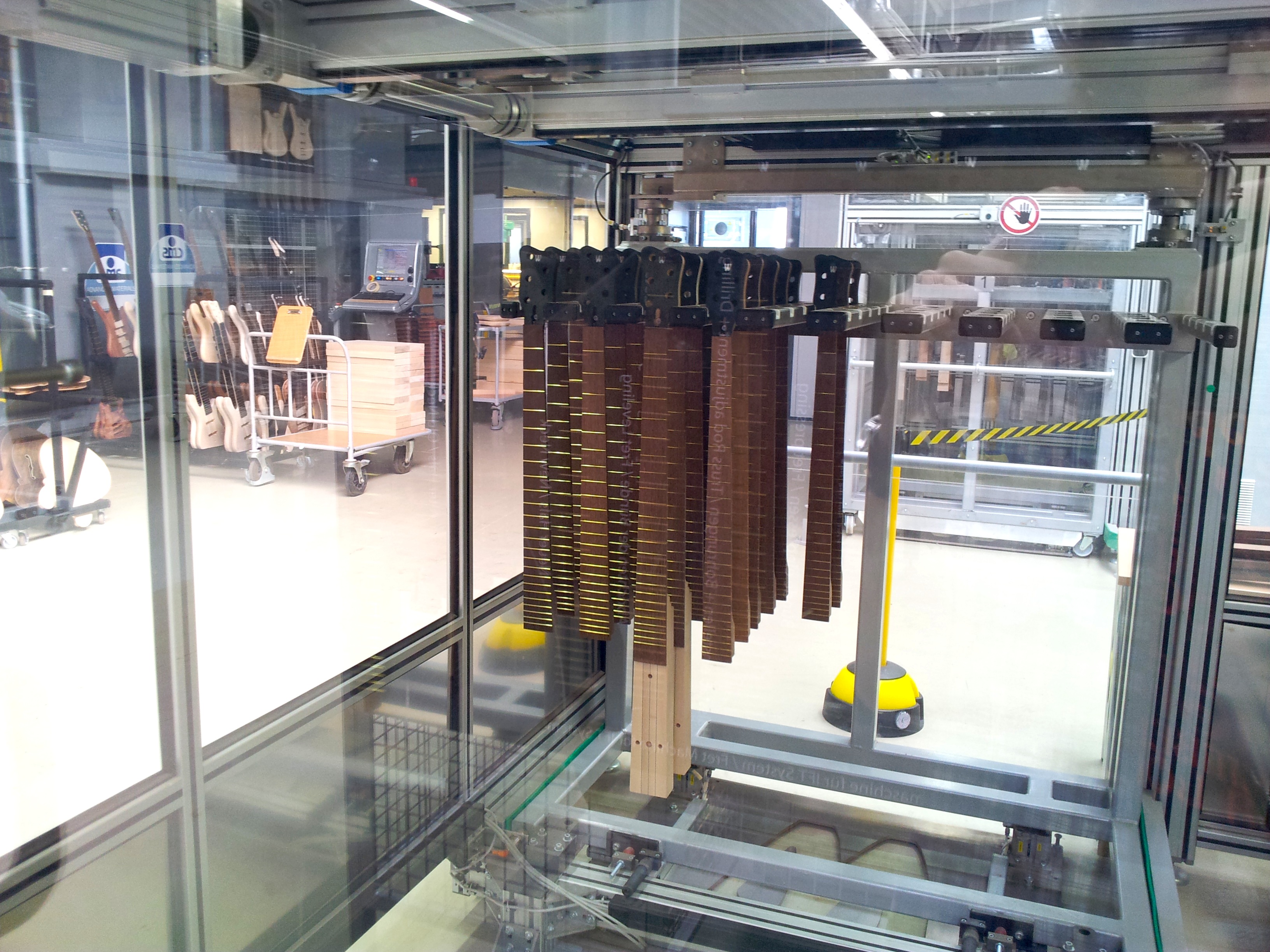
Warwick & Framus Factory Tour
And here are a few necks, ready to undergo the aforementioned process
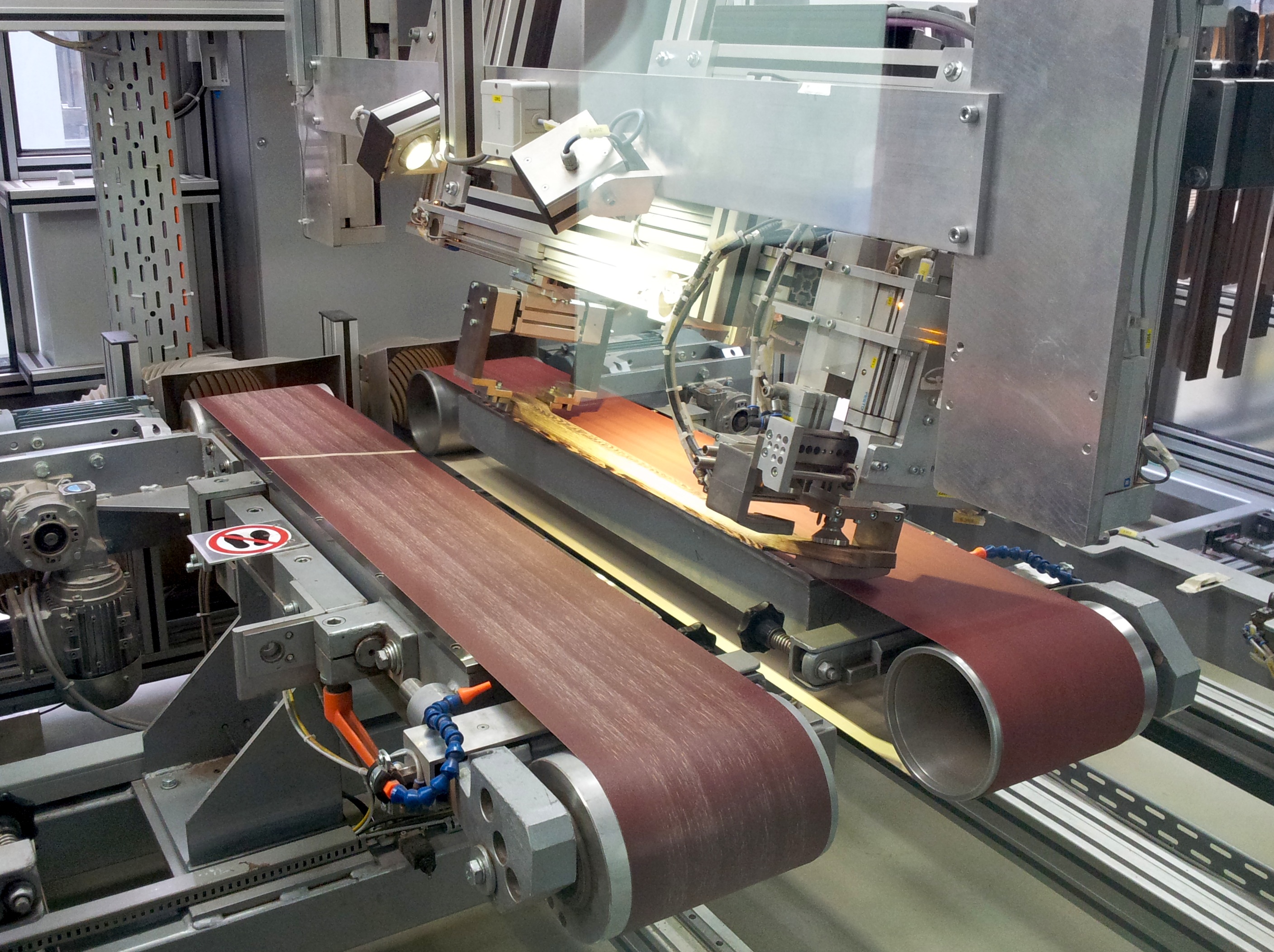
Warwick & Framus Factory Tour
In this shot, we’ve caught the machine in the middle of sanding a neck
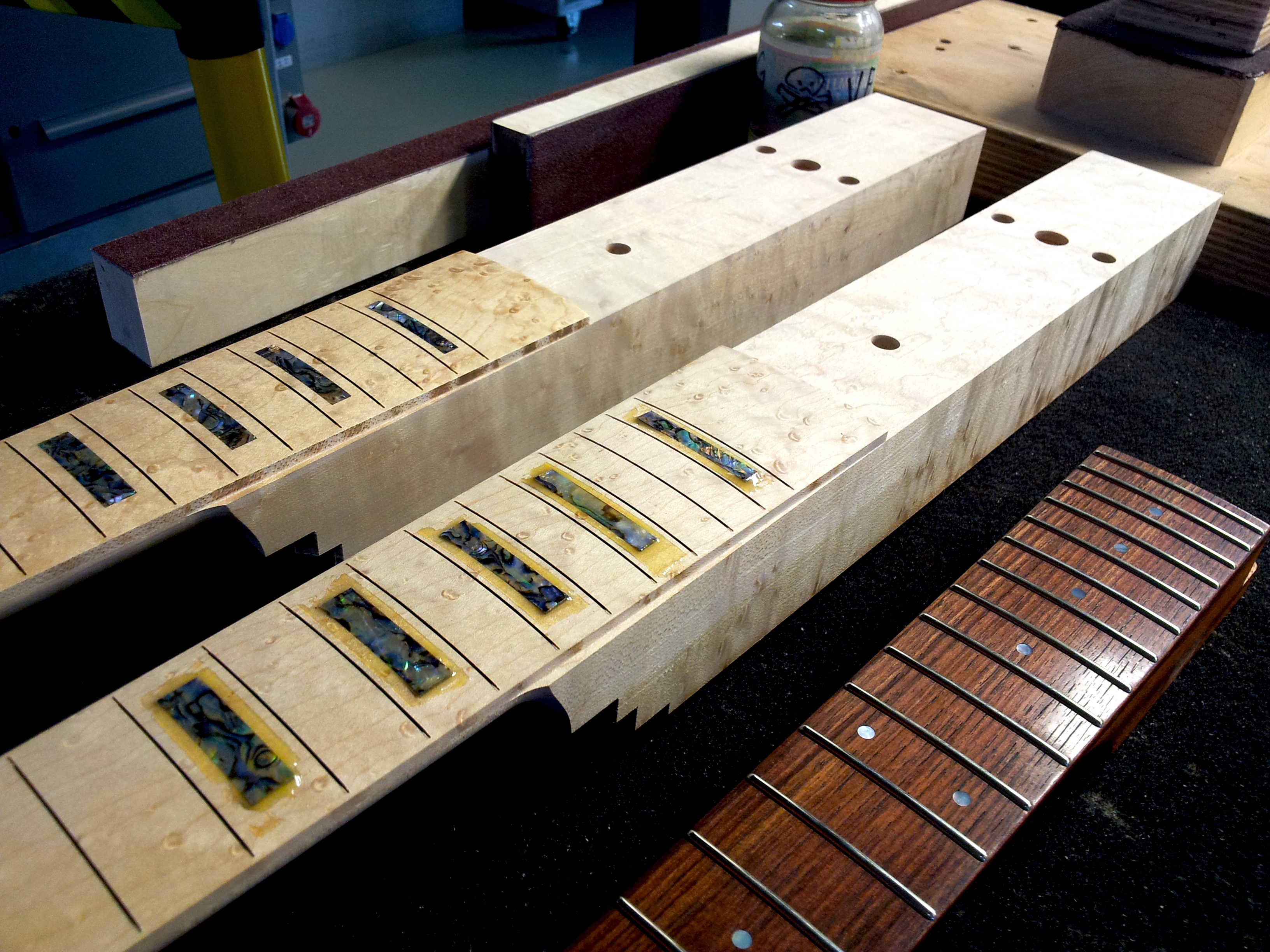
Warwick & Framus Factory Tour
Here are some fretboards in the process of receiving some tasty-looking inlays
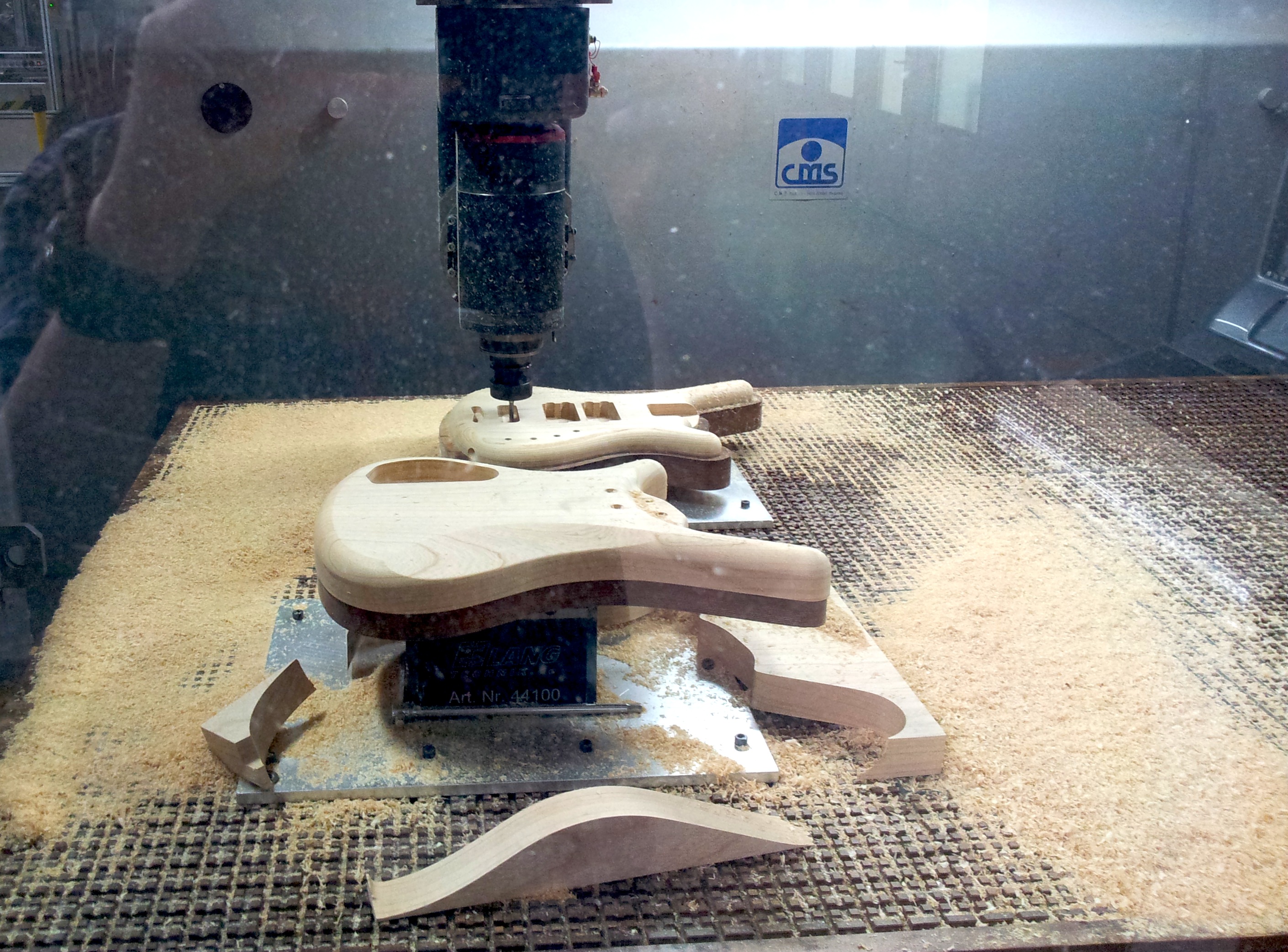
Warwick & Framus Factory Tour
Now, back to that CNC routing machine, where guitar and bass bodies are also routed
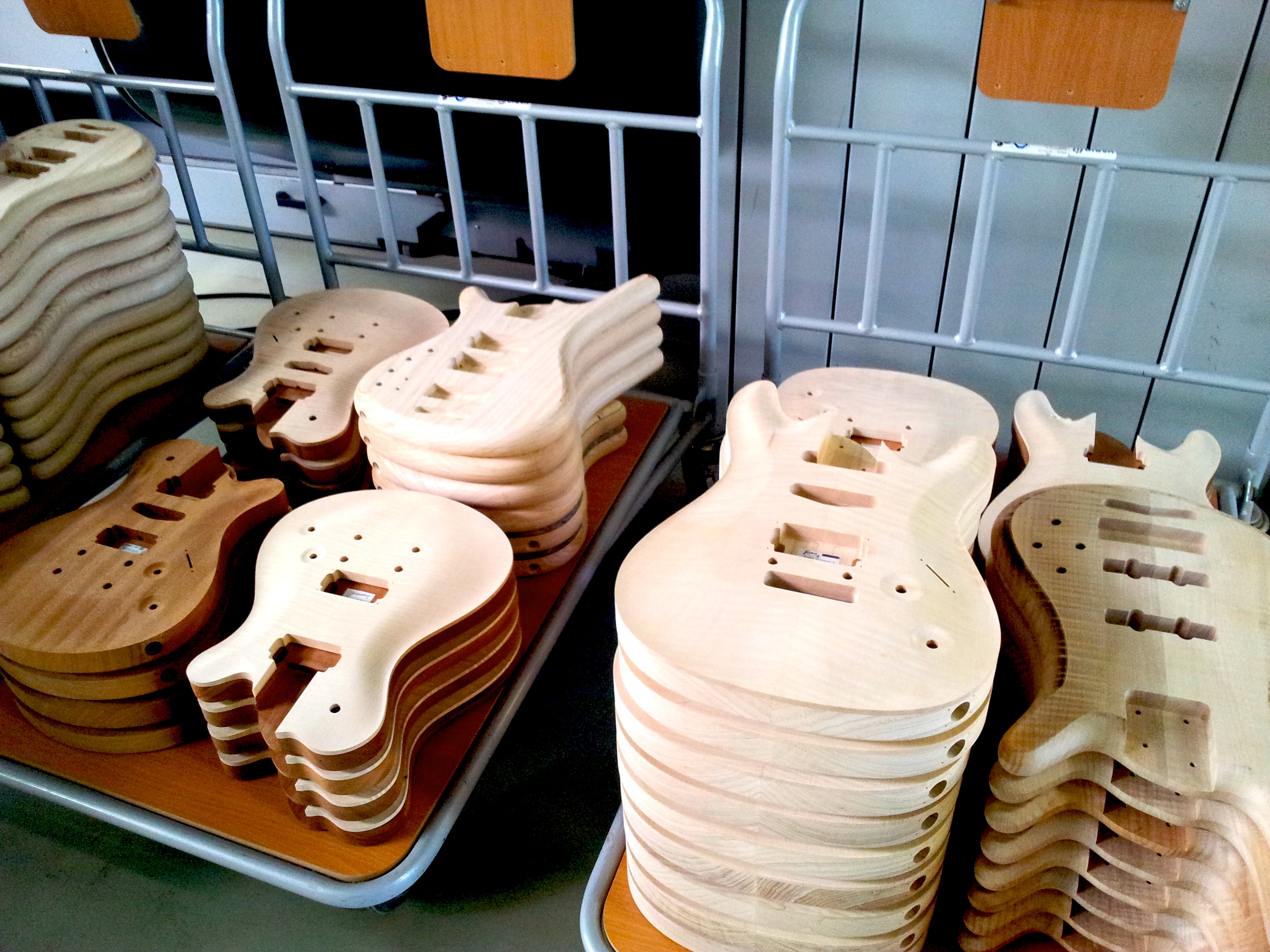
Warwick & Framus Factory Tour
That leaves us with a big ol’ pile of bodies, ready for necks, hardware and electronics
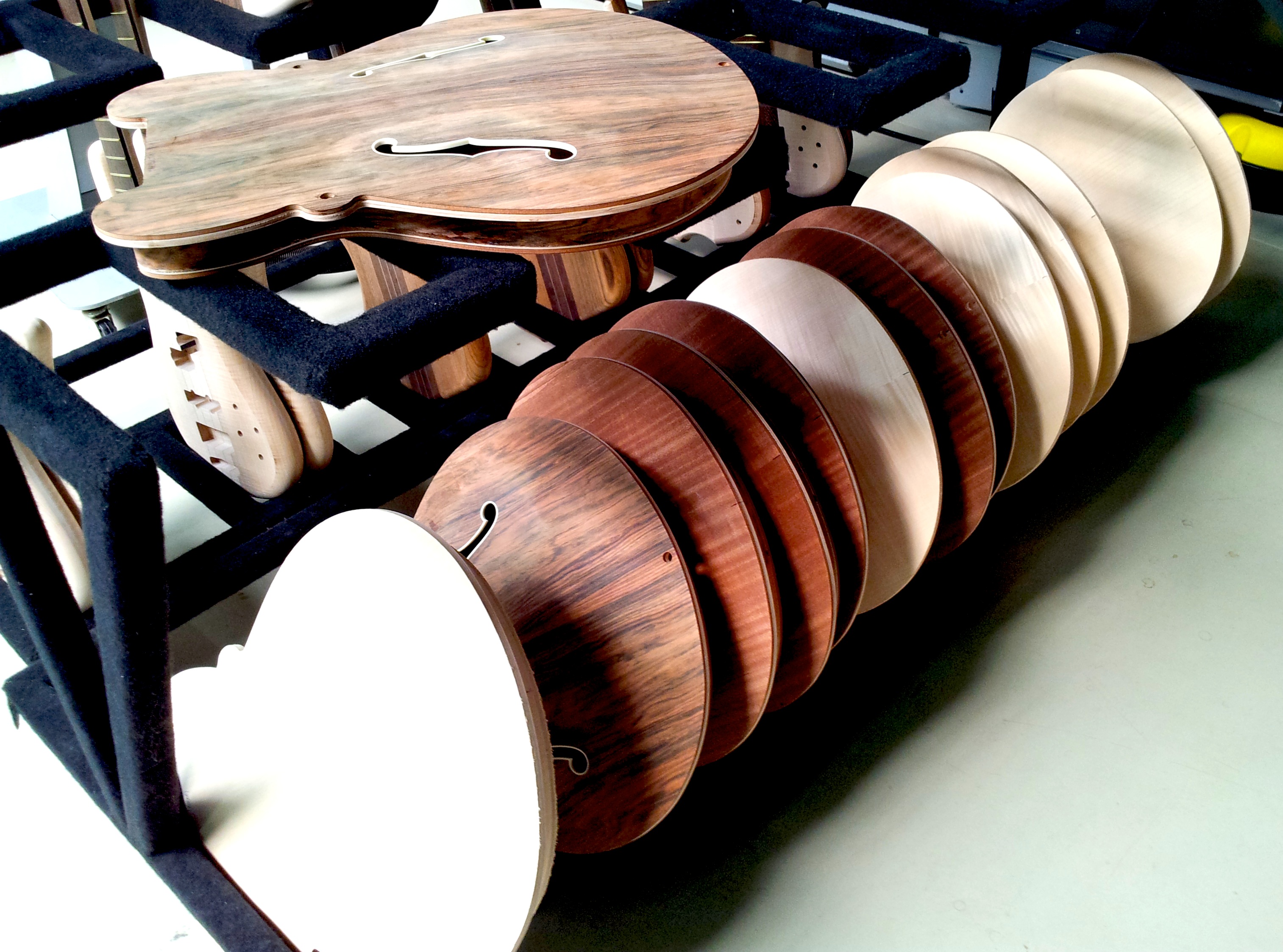
Warwick & Framus Factory Tour
Tops for semi-hollow instruments are also crafted here
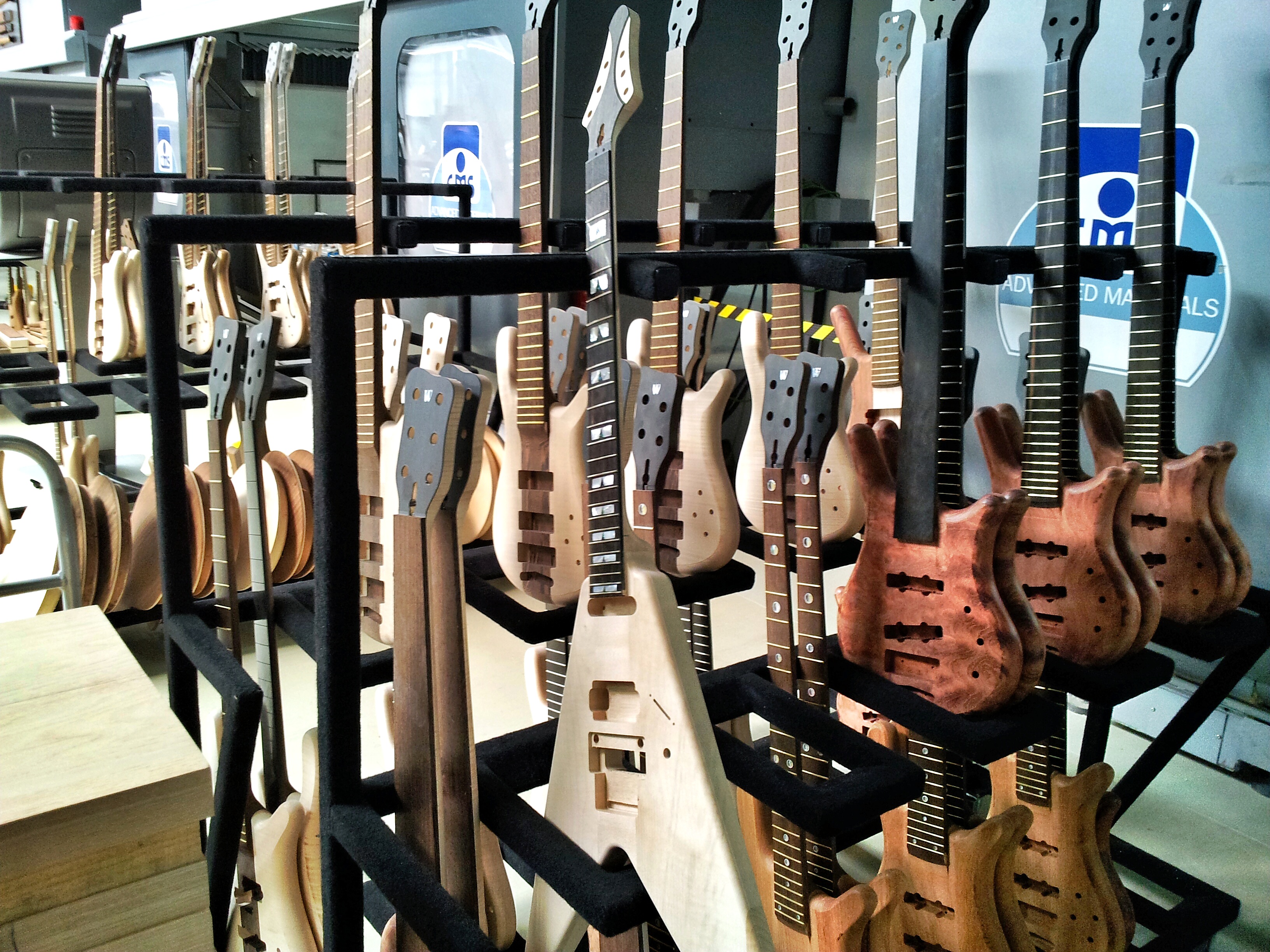
Warwick & Framus Factory Tour
Necks are then bolted on to bodies, or neck-through designs have their wood sides glued on
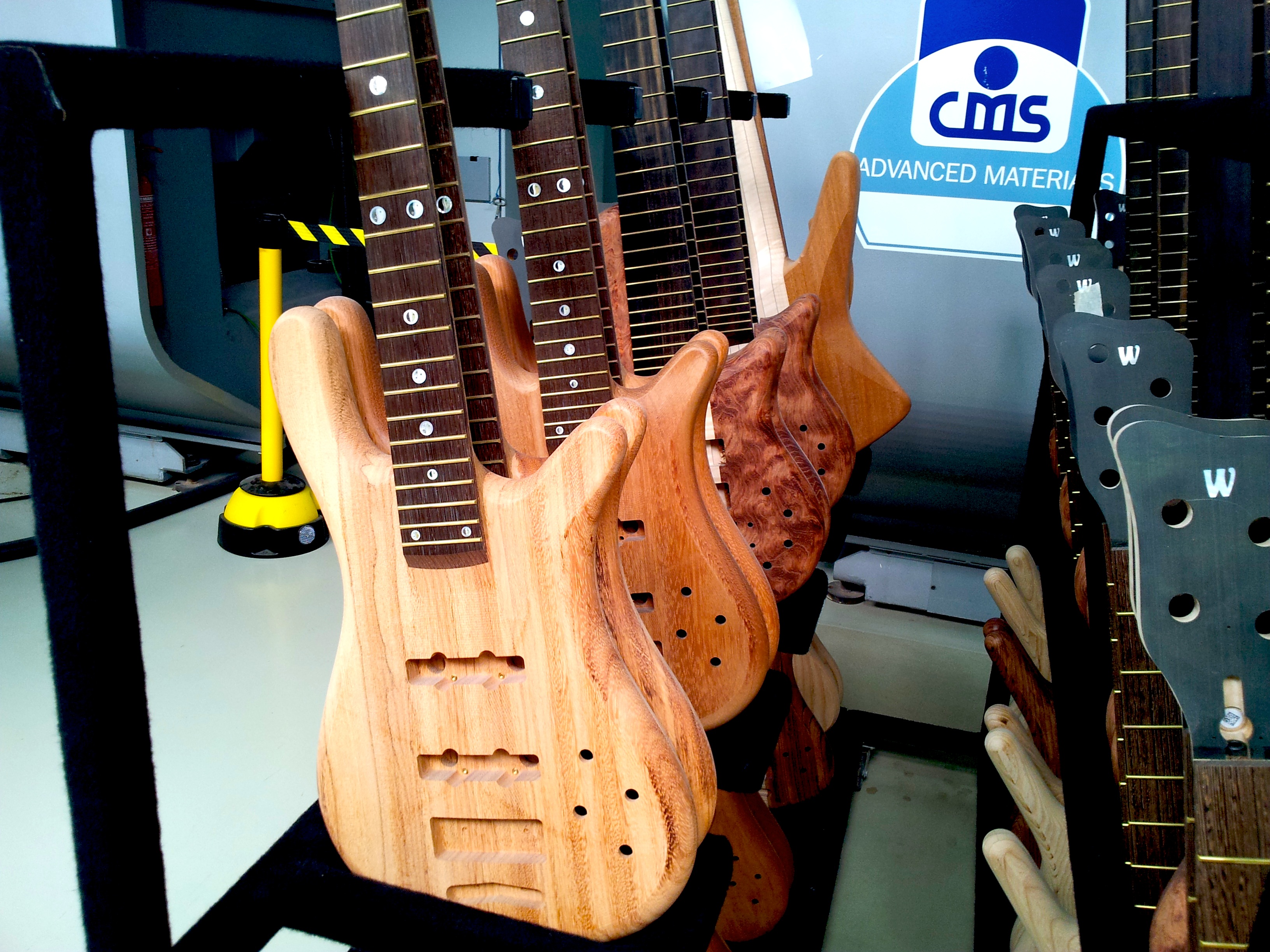
Warwick & Framus Factory Tour
Some Warwick basses looking good, even before they get their finishes
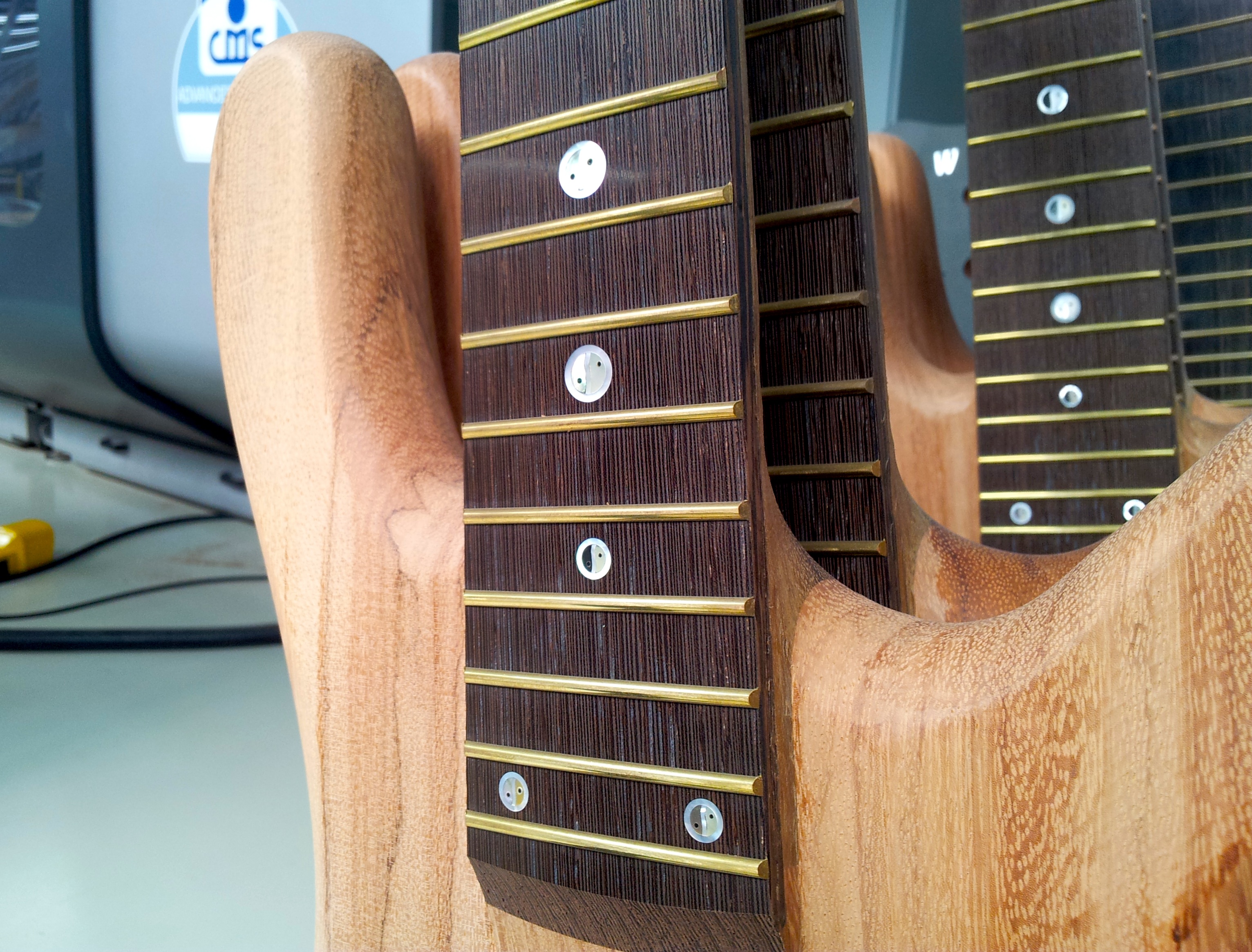
Warwick & Framus Factory Tour
This fingerboard has a tasty fingerboard grain and yin-yang inlays
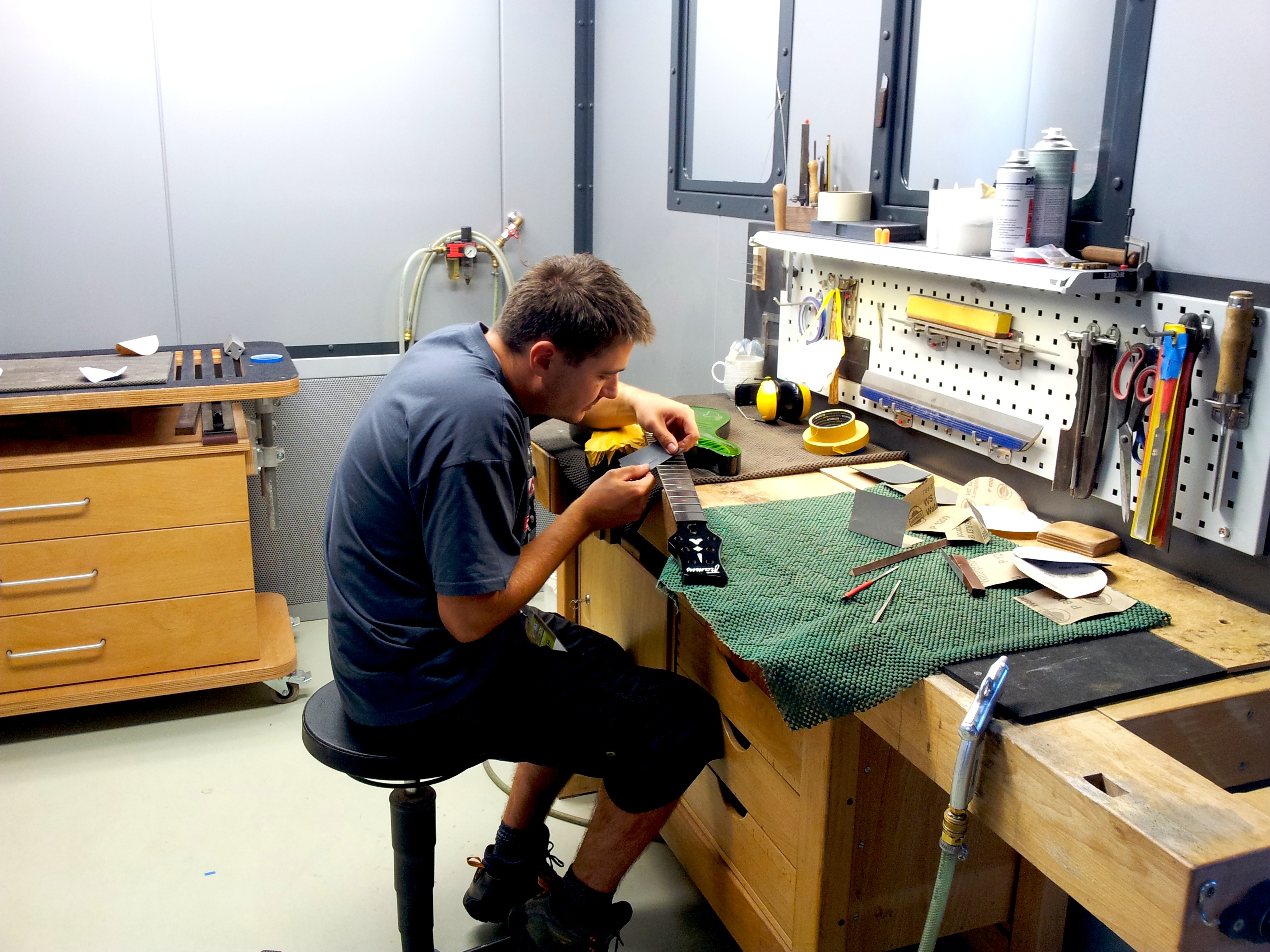
Warwick & Framus Factory Tour
The bodies and necks are hand-sanded for a comfortable feel
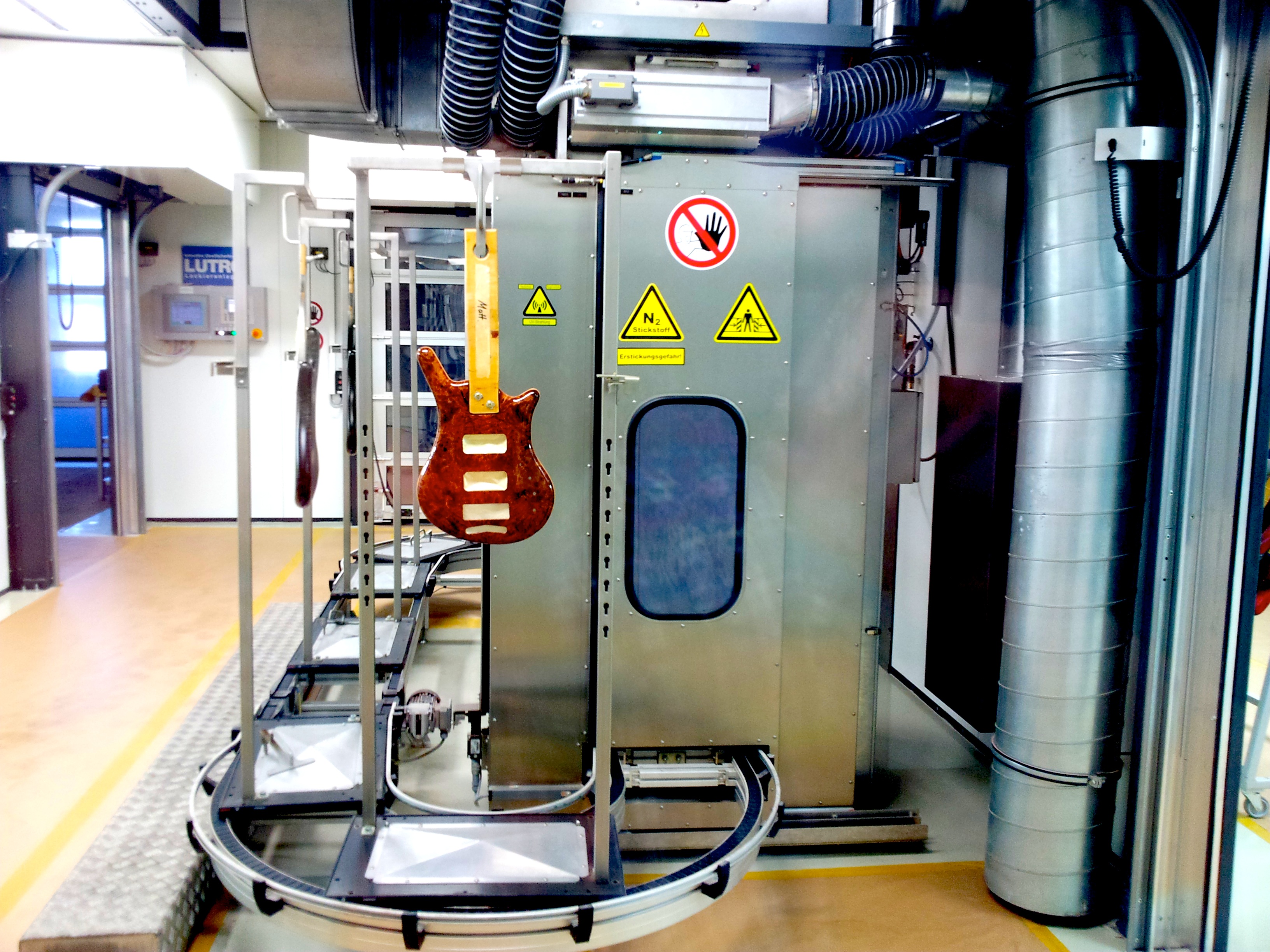
Warwick & Framus Factory Tour
After a quick spray with lacquer, each instrument heads to the UV drying chamber…
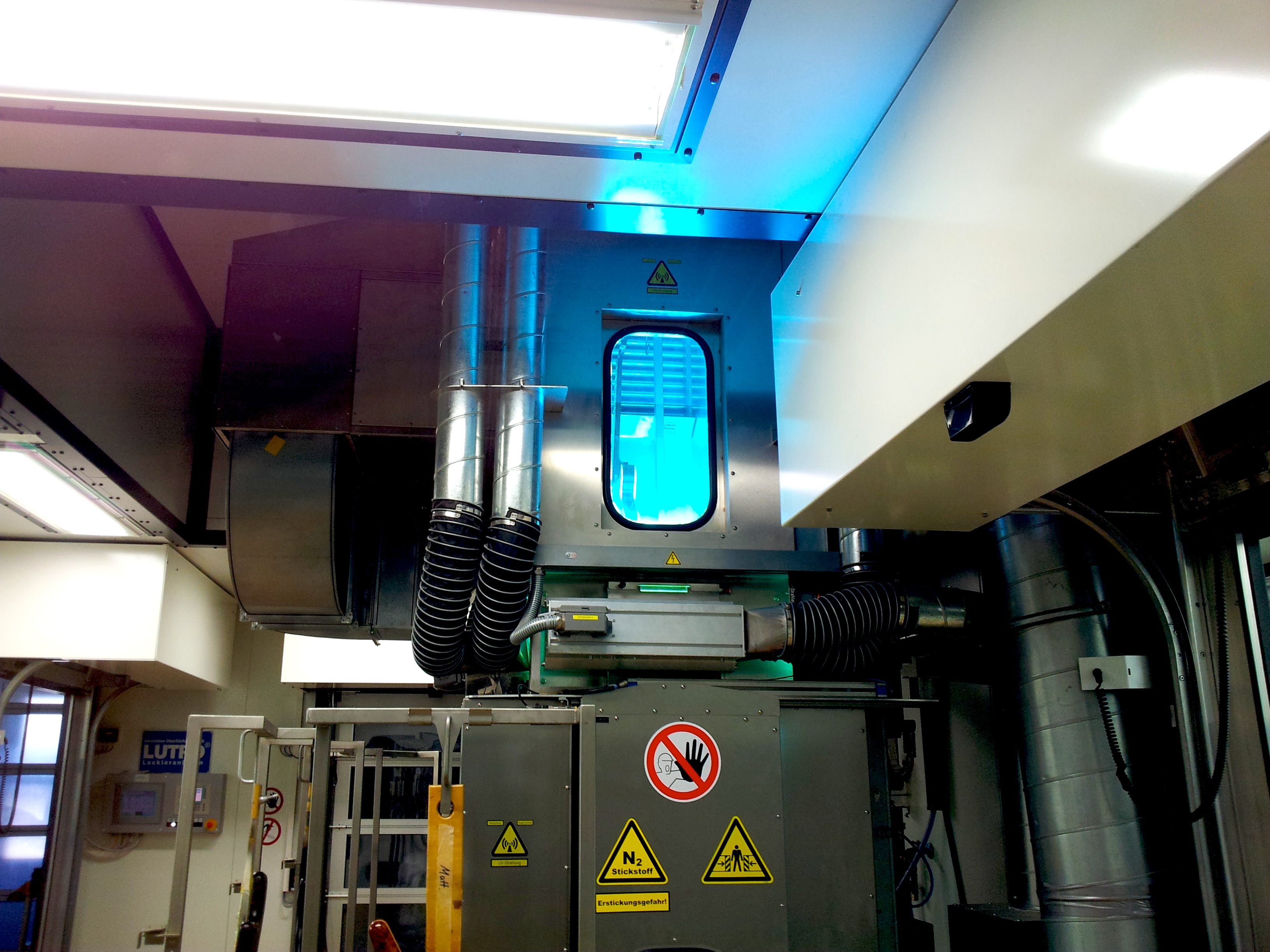
Warwick & Framus Factory Tour
A guitar or bass is only up there for 10 seconds, after which the lacquer is completely dry – speedy!
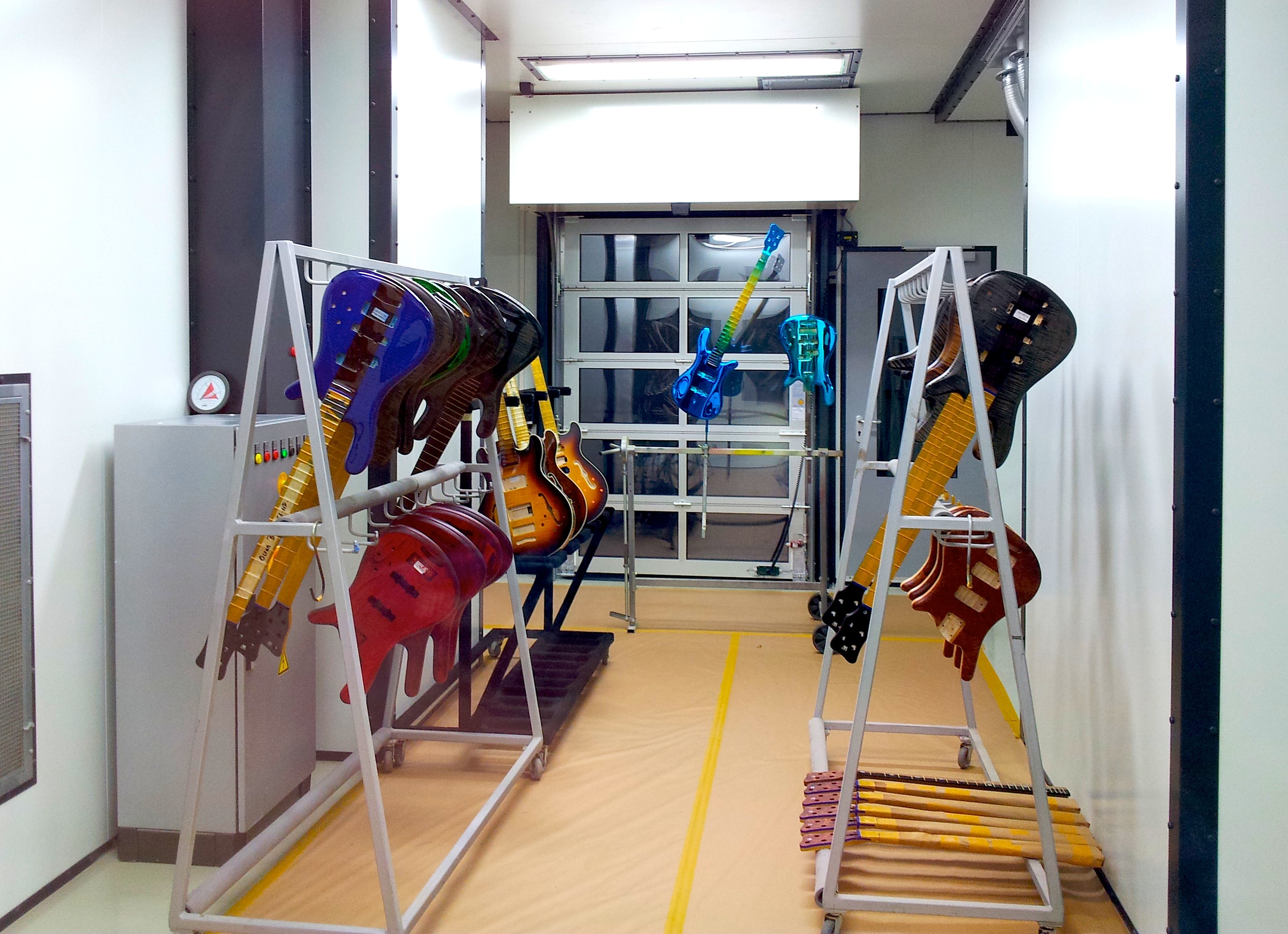
Warwick & Framus Factory Tour
Here we have a few guitars, waiting for the next stage – note the awesome chrome finish at the back
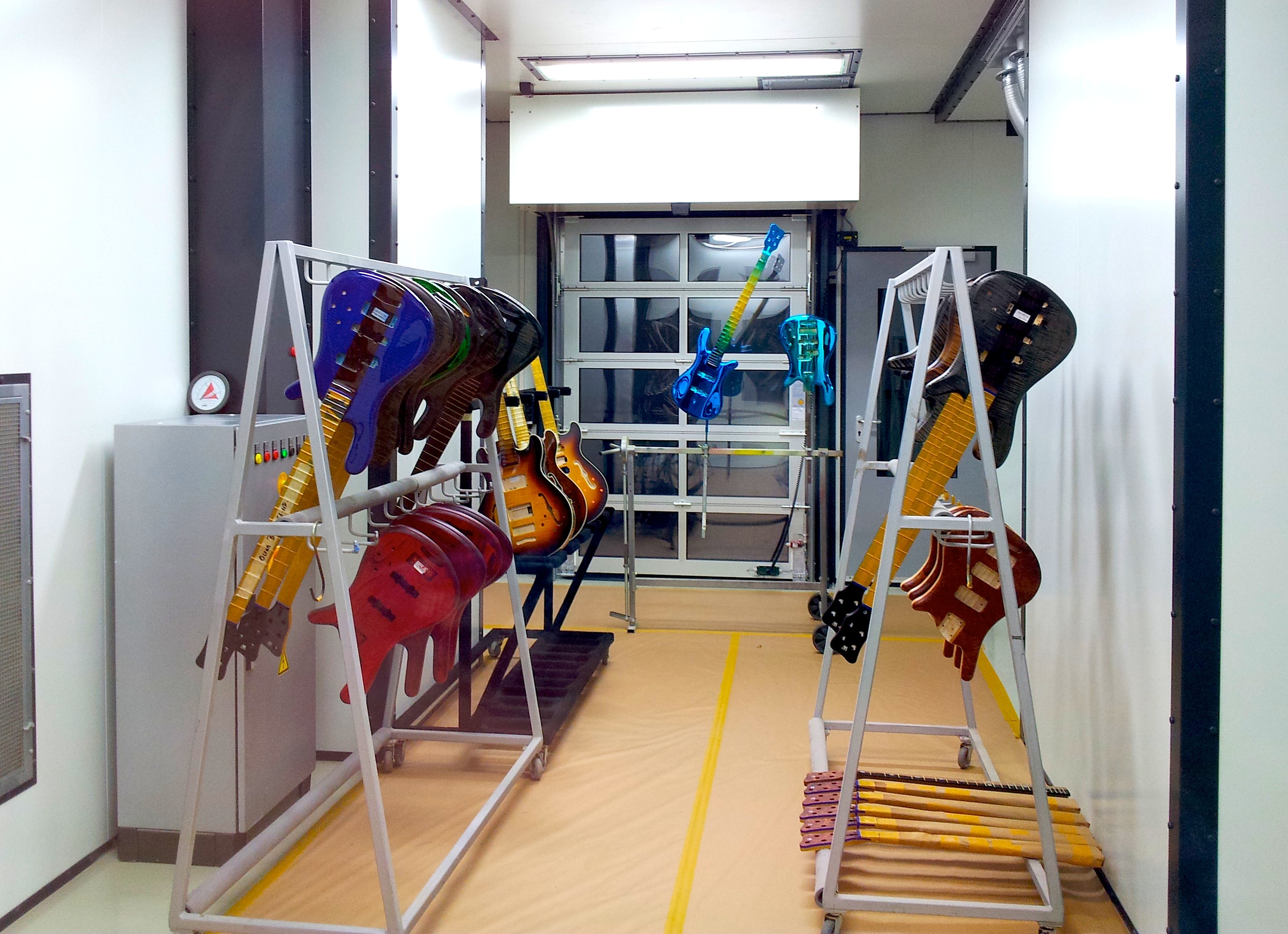
Warwick & Framus Factory Tour
Here we have a few guitars, waiting for the next stage – note the awesome chrome finish at the back
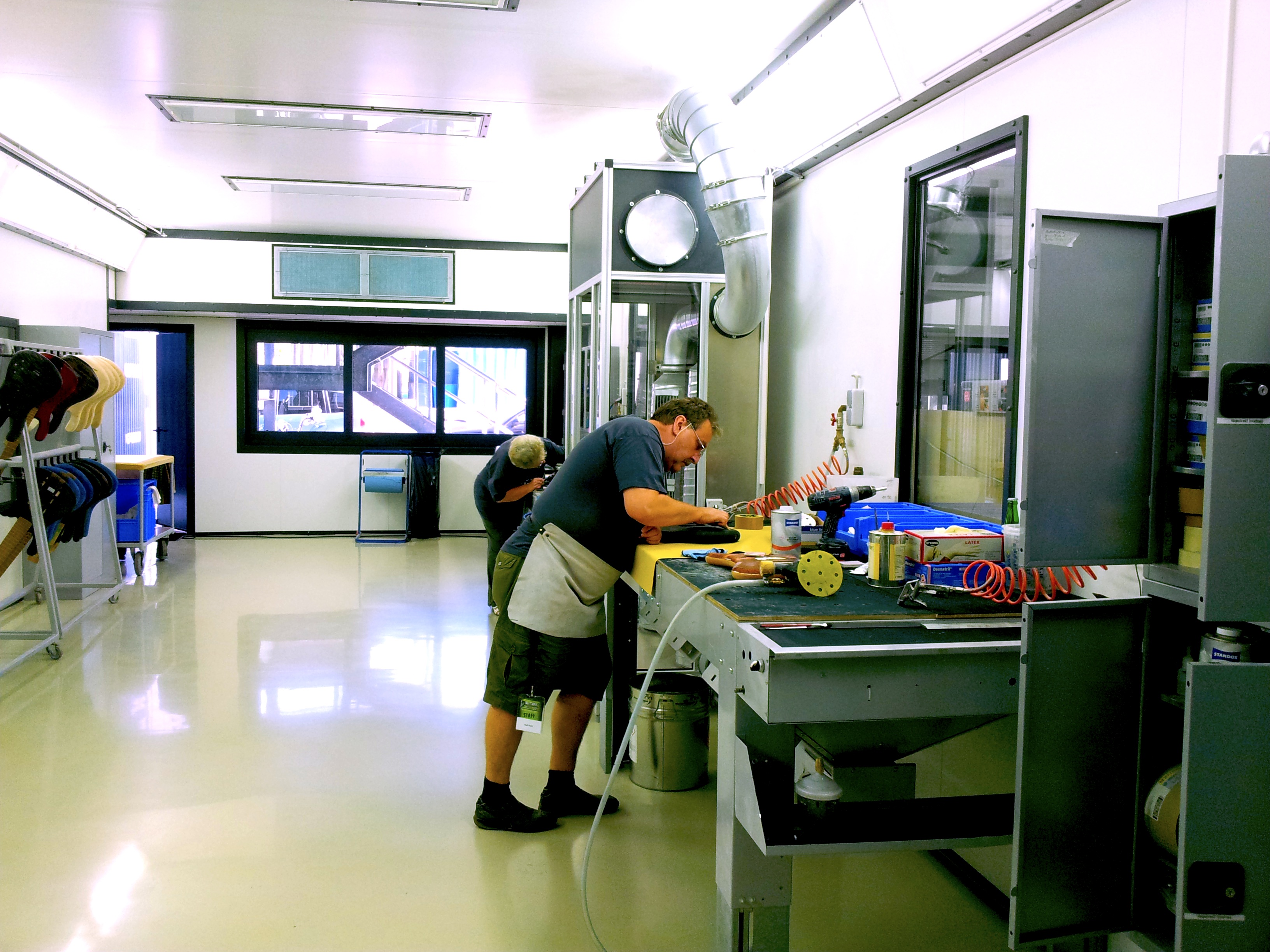
Warwick & Framus Factory Tour
Some finishes require multiple sanding and lacquering stages – this is the sanding station
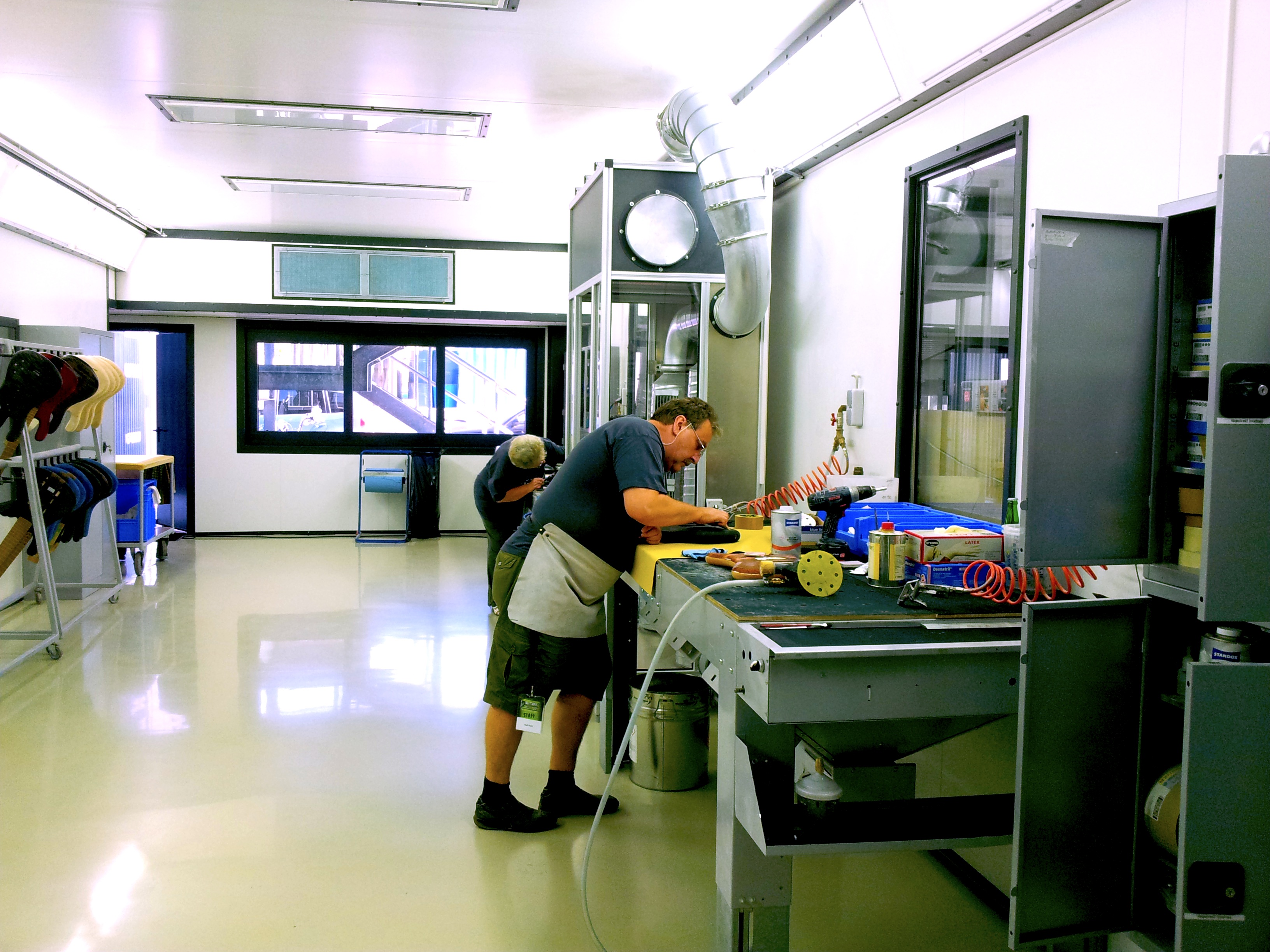
Warwick & Framus Factory Tour
Some finishes require multiple sanding and lacquering stages – this is the sanding station
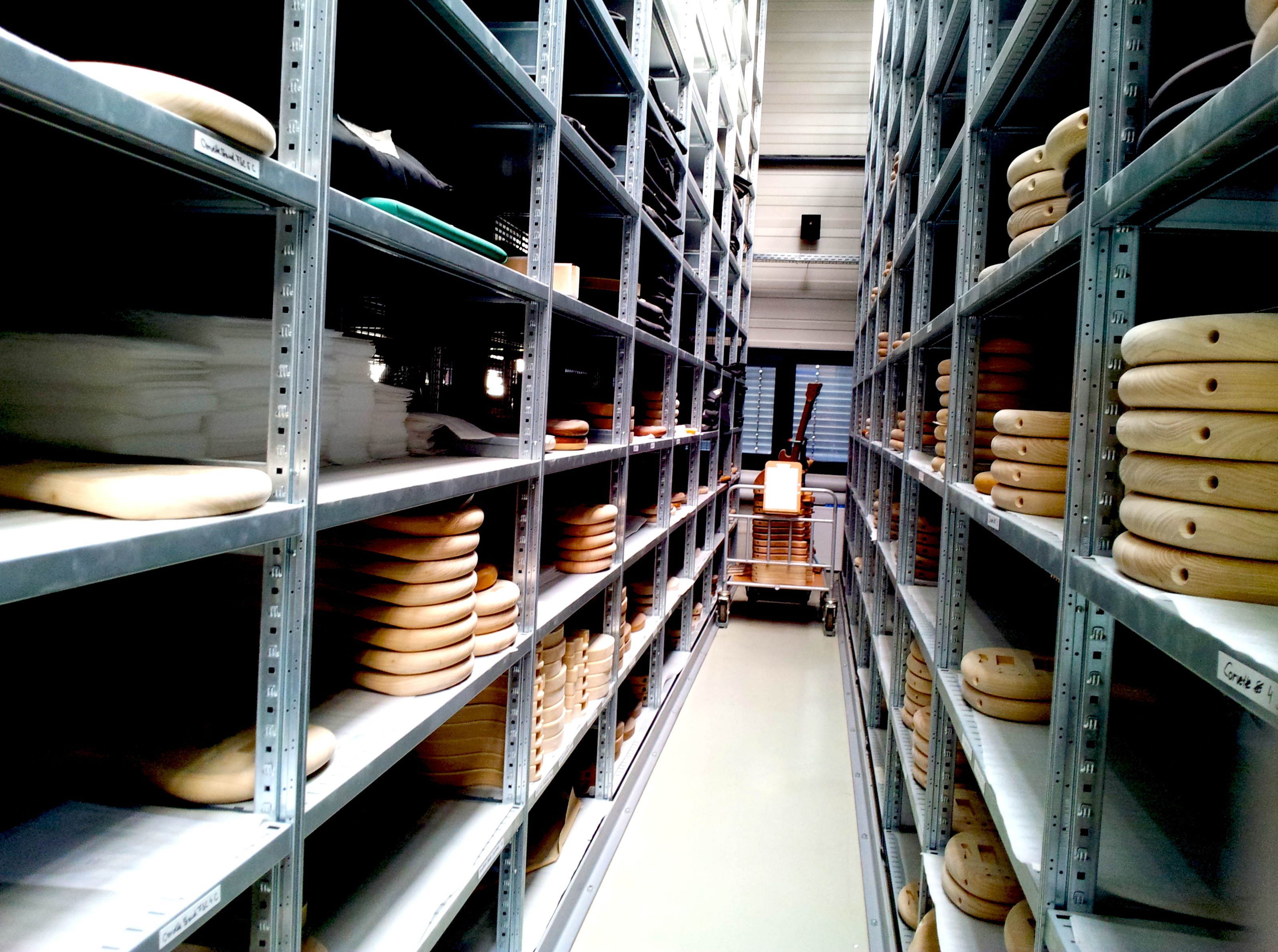
Warwick & Framus Factory Tour
And here’s where bodies are stored while they wait to be processed – it’s like IKEA for guitars!
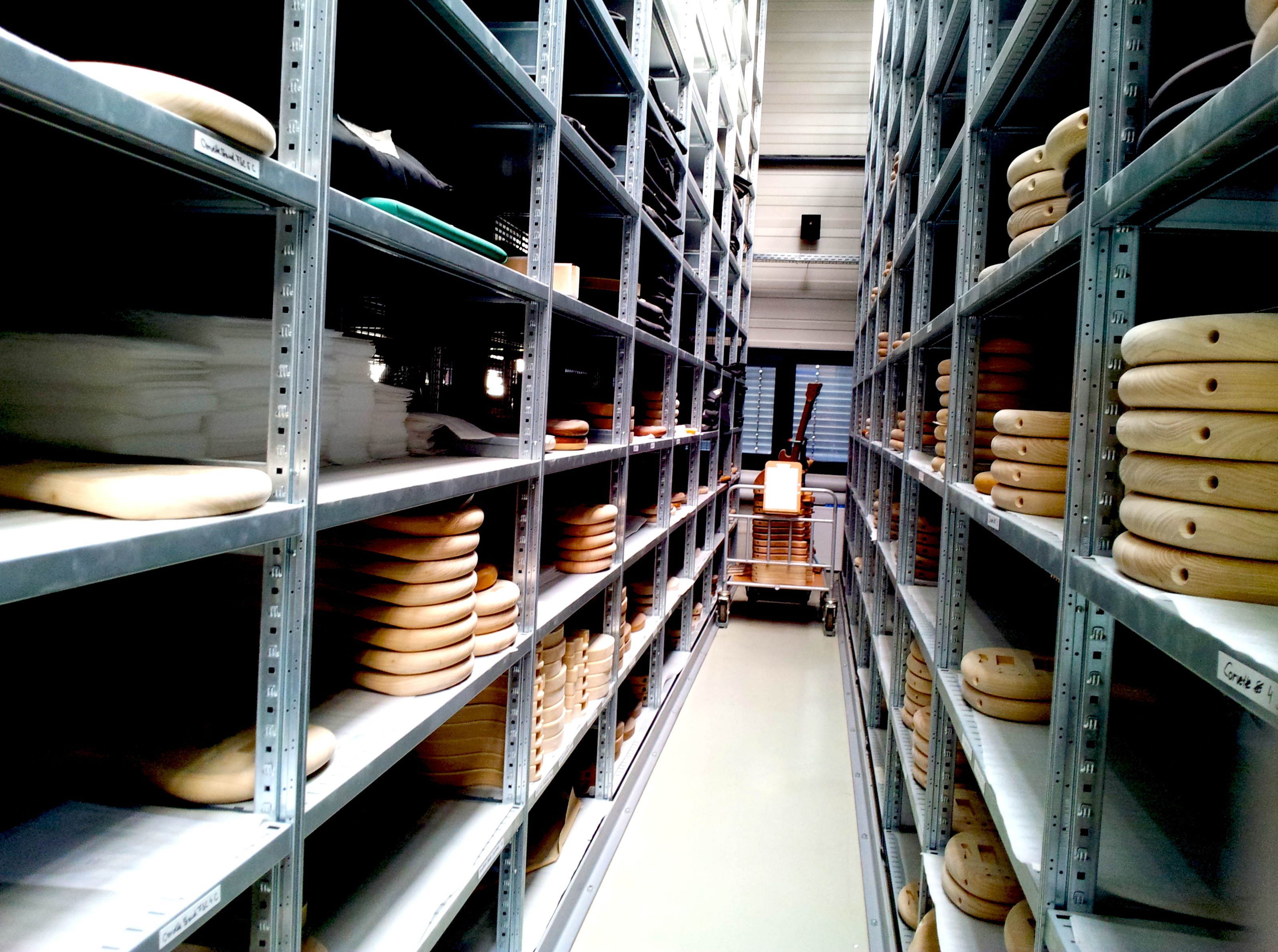
Warwick & Framus Factory Tour
And here’s where bodies are stored while they wait to be processed – it’s like IKEA for guitars!
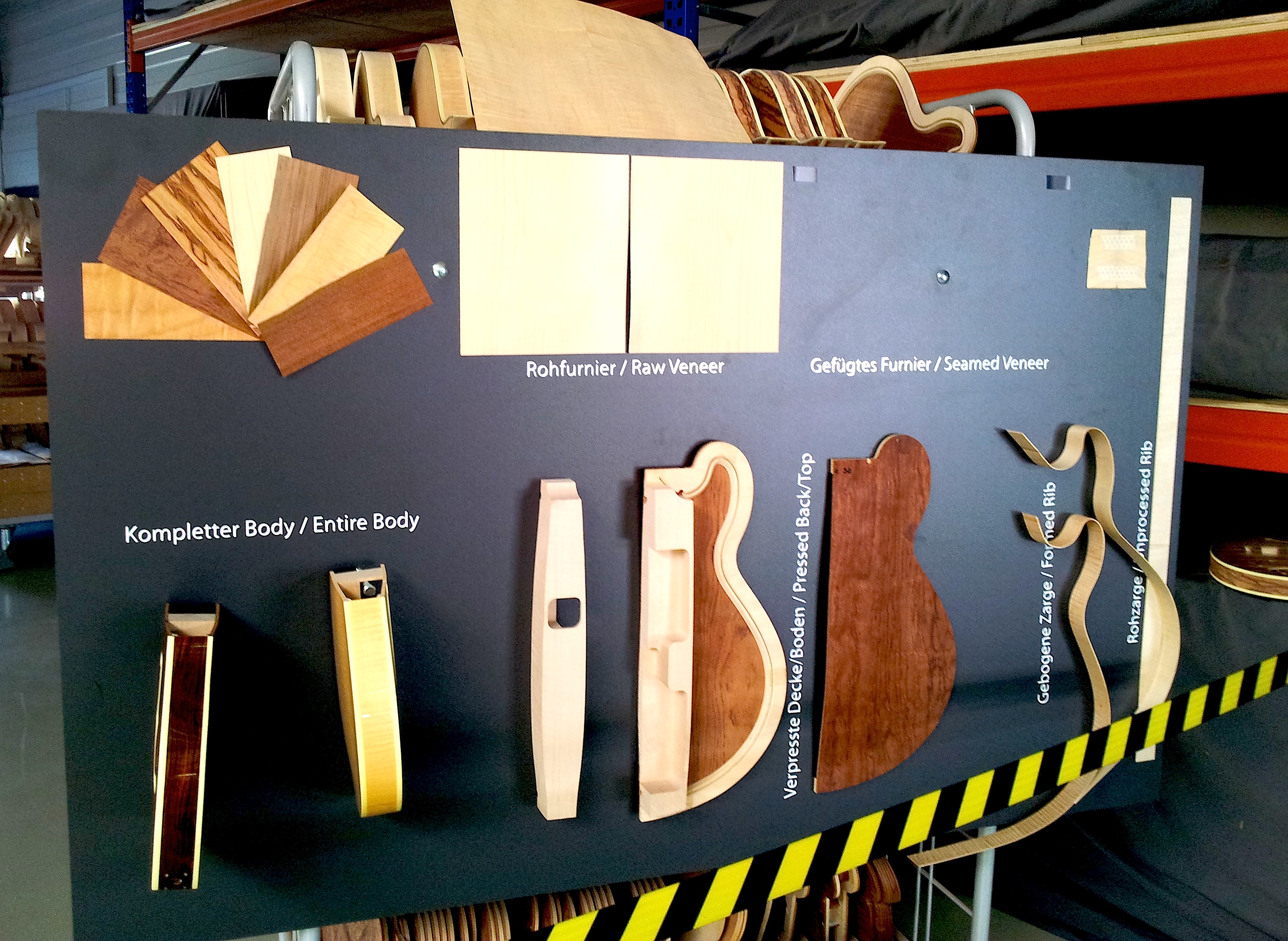
Warwick & Framus Factory Tour
That there display gives a rough idea of the different parts that go into a Framus semi-hollow guitar – it’s a lot more complicated than a solidbody
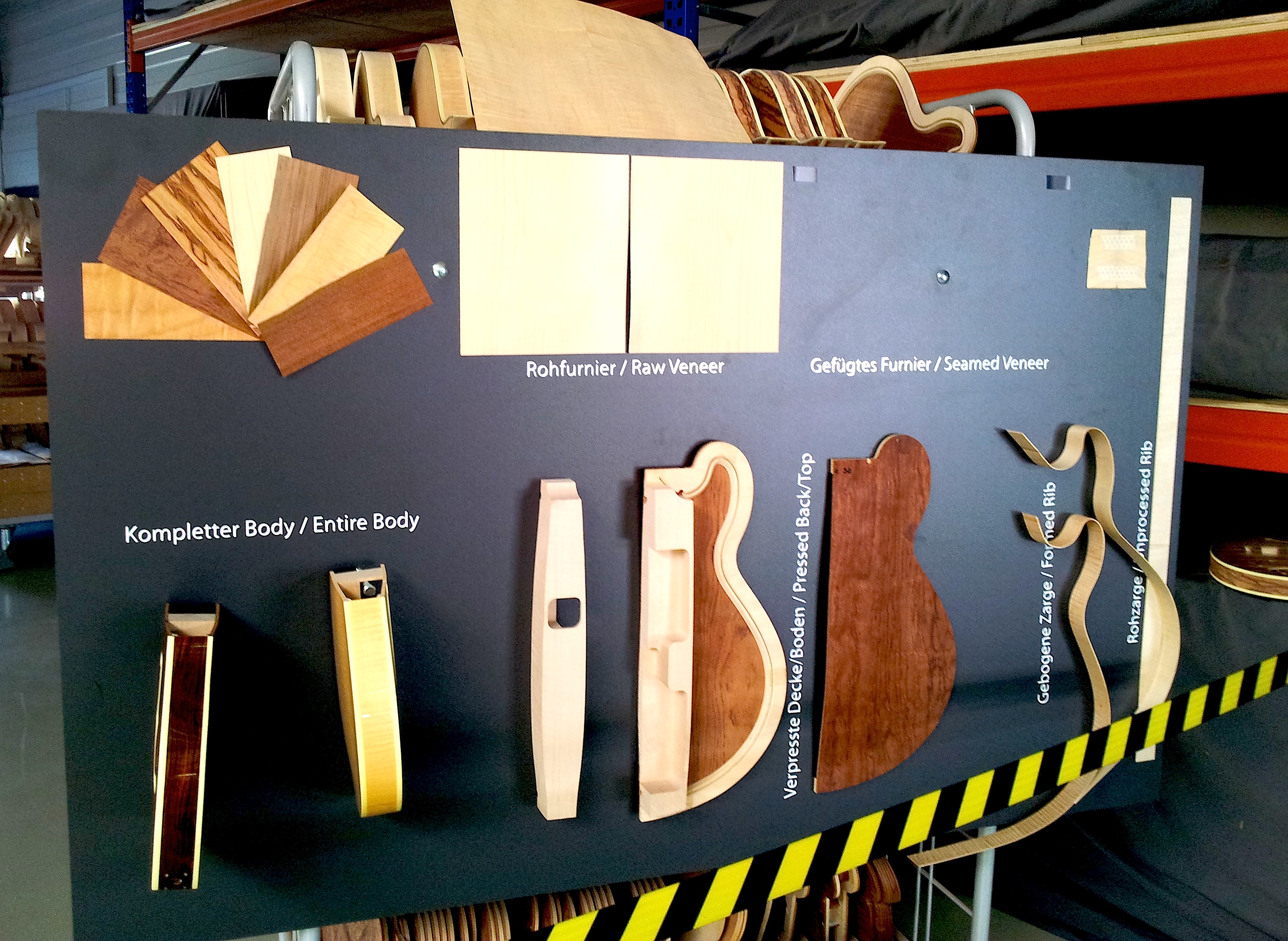
Warwick & Framus Factory Tour
That there display gives a rough idea of the different parts that go into a Framus semi-hollow guitar – it’s a lot more complicated than a solidbody
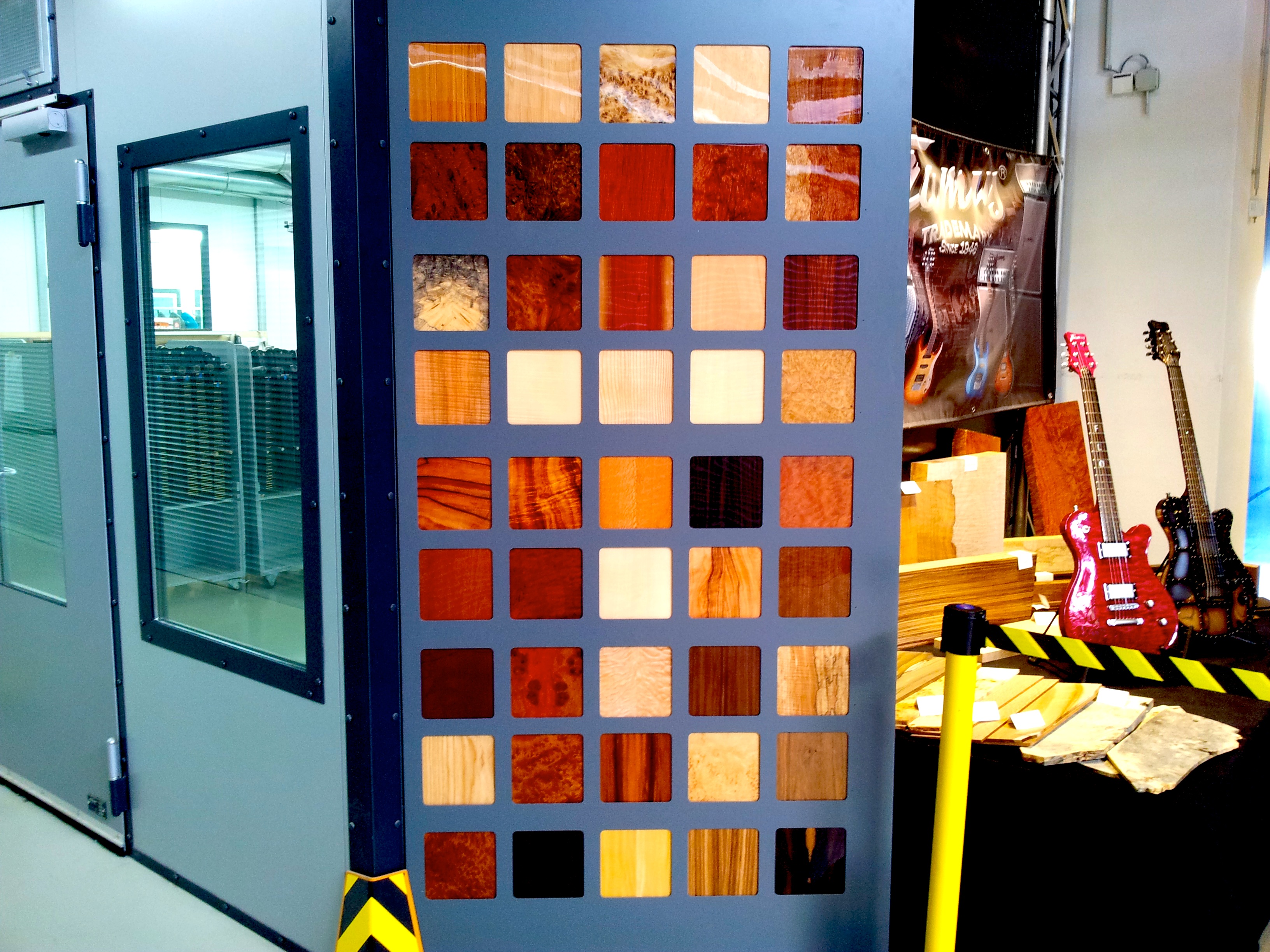
Warwick & Framus Factory Tour
Warwick and Framus use 45 different types of wood for their instruments
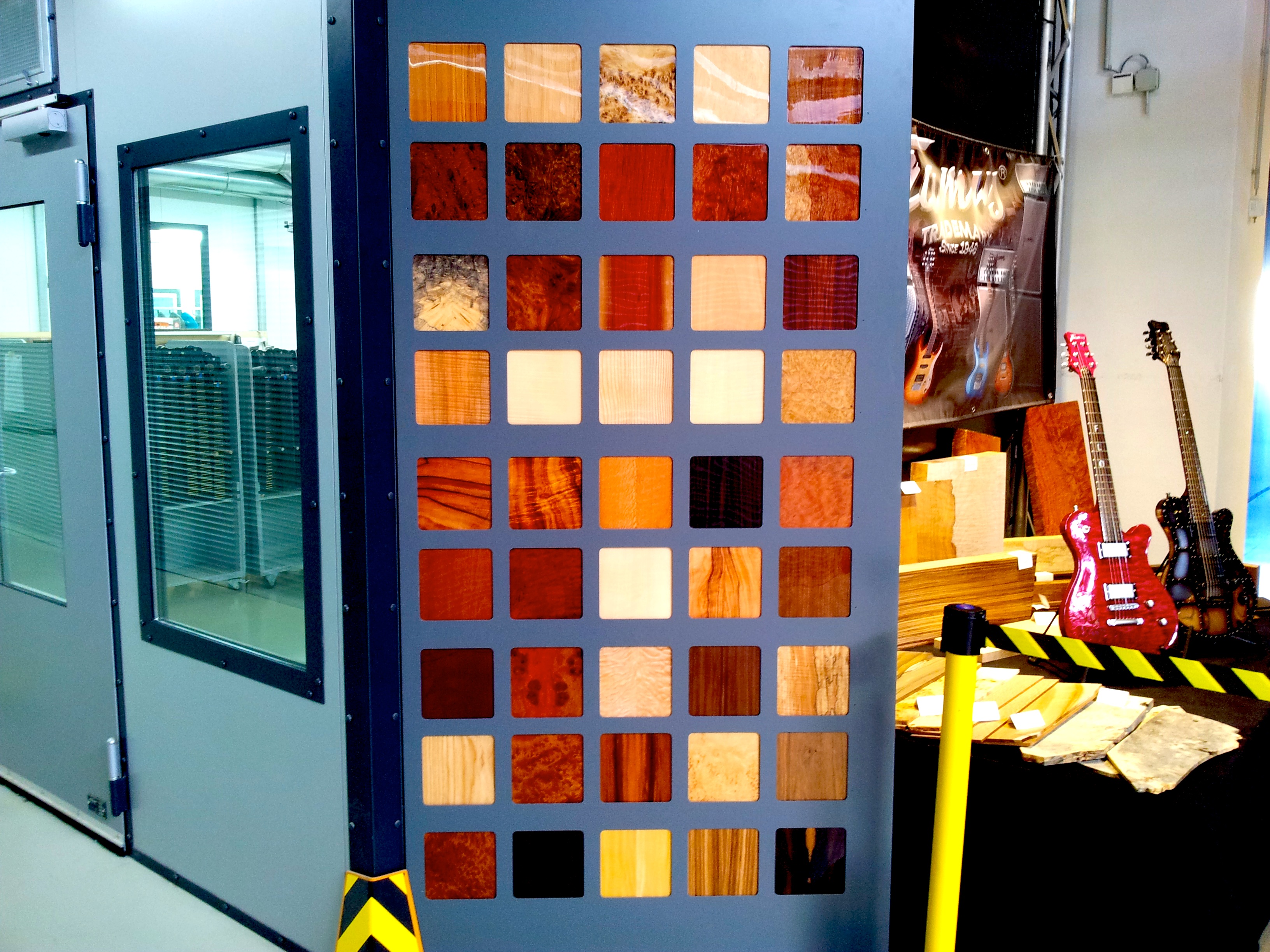
Warwick & Framus Factory Tour
Warwick and Framus use 45 different types of wood for their instruments
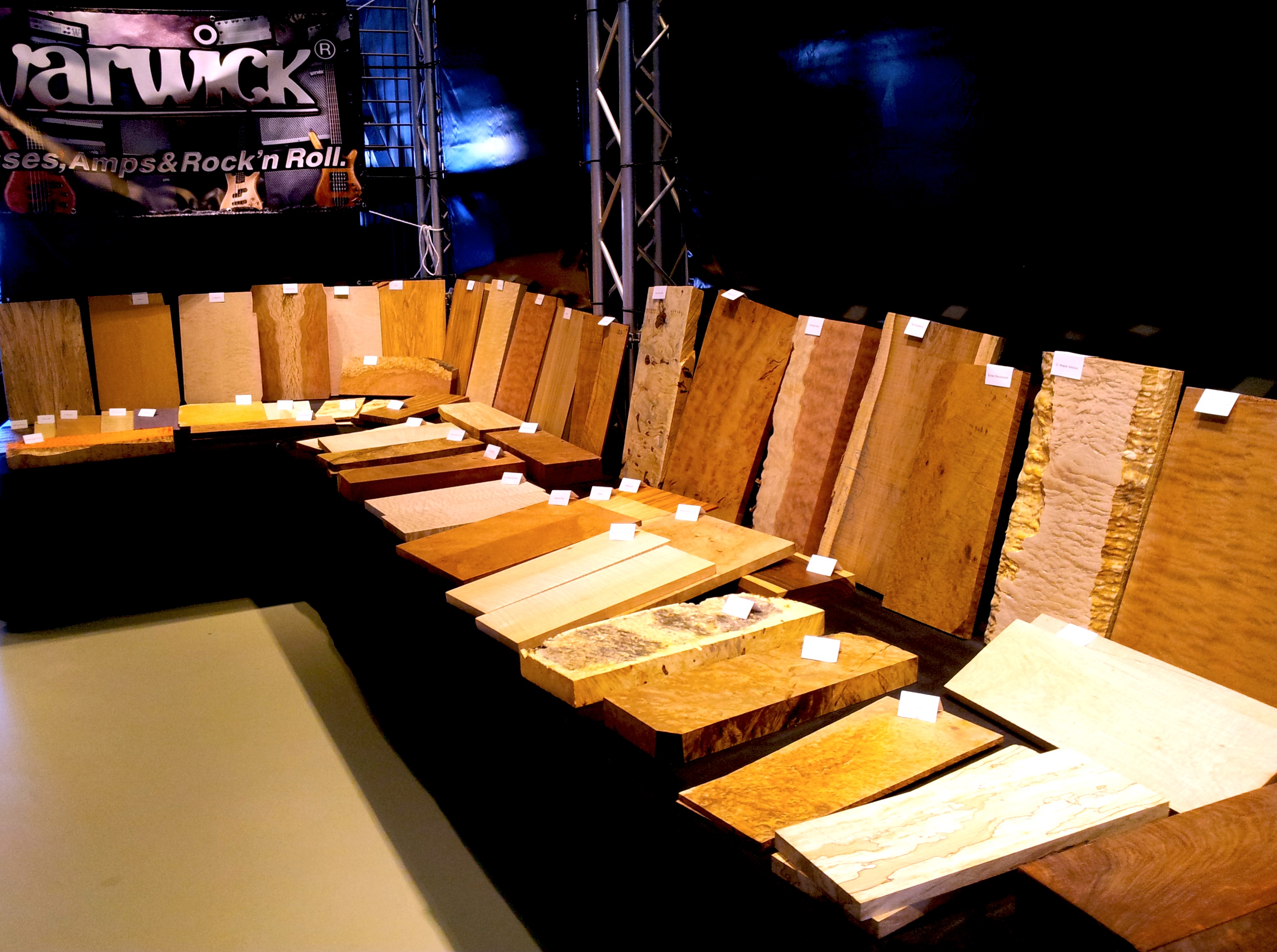
Warwick & Framus Factory Tour
That’s right, forty-five!
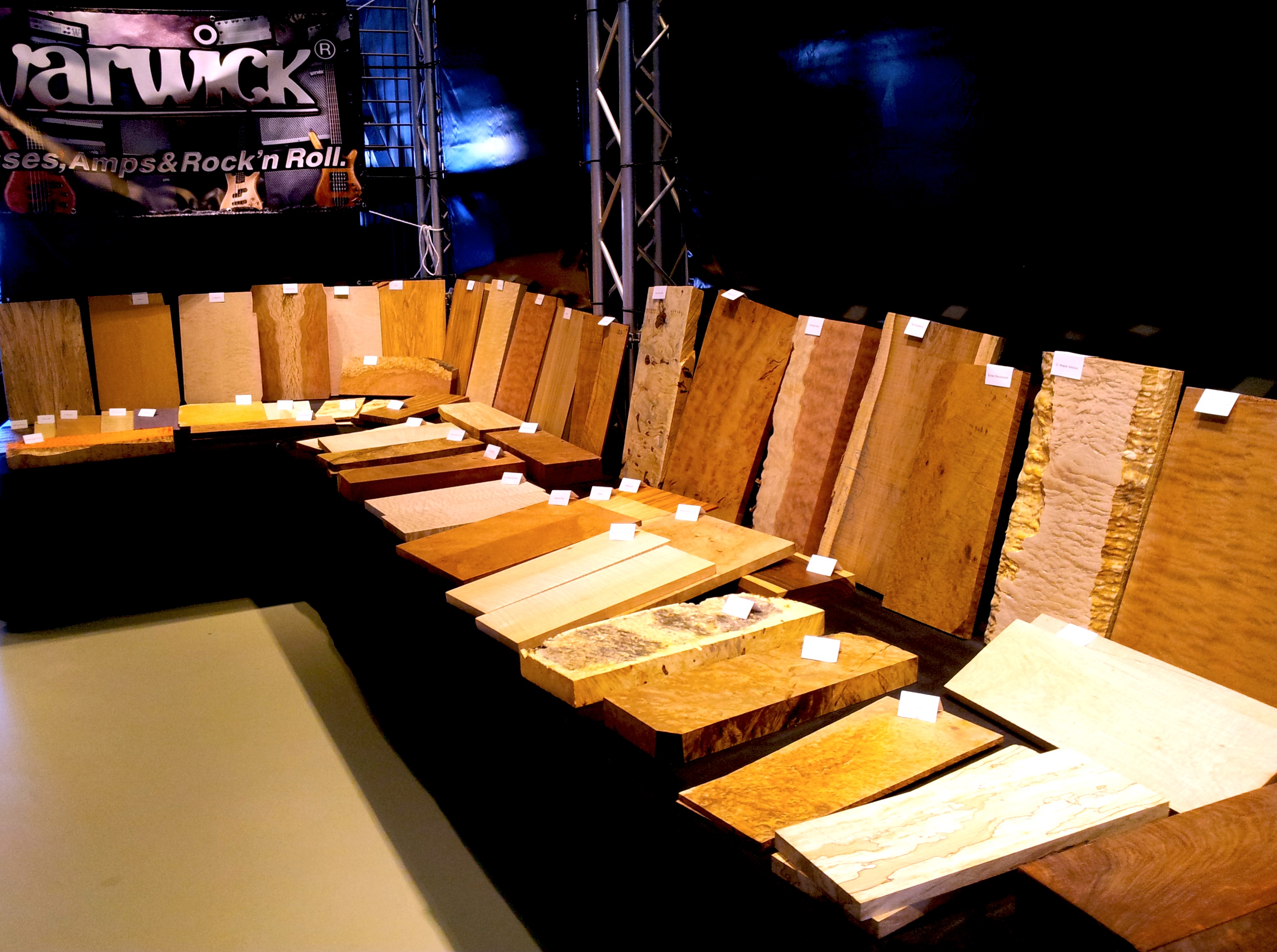
Warwick & Framus Factory Tour
That’s right, forty-five!
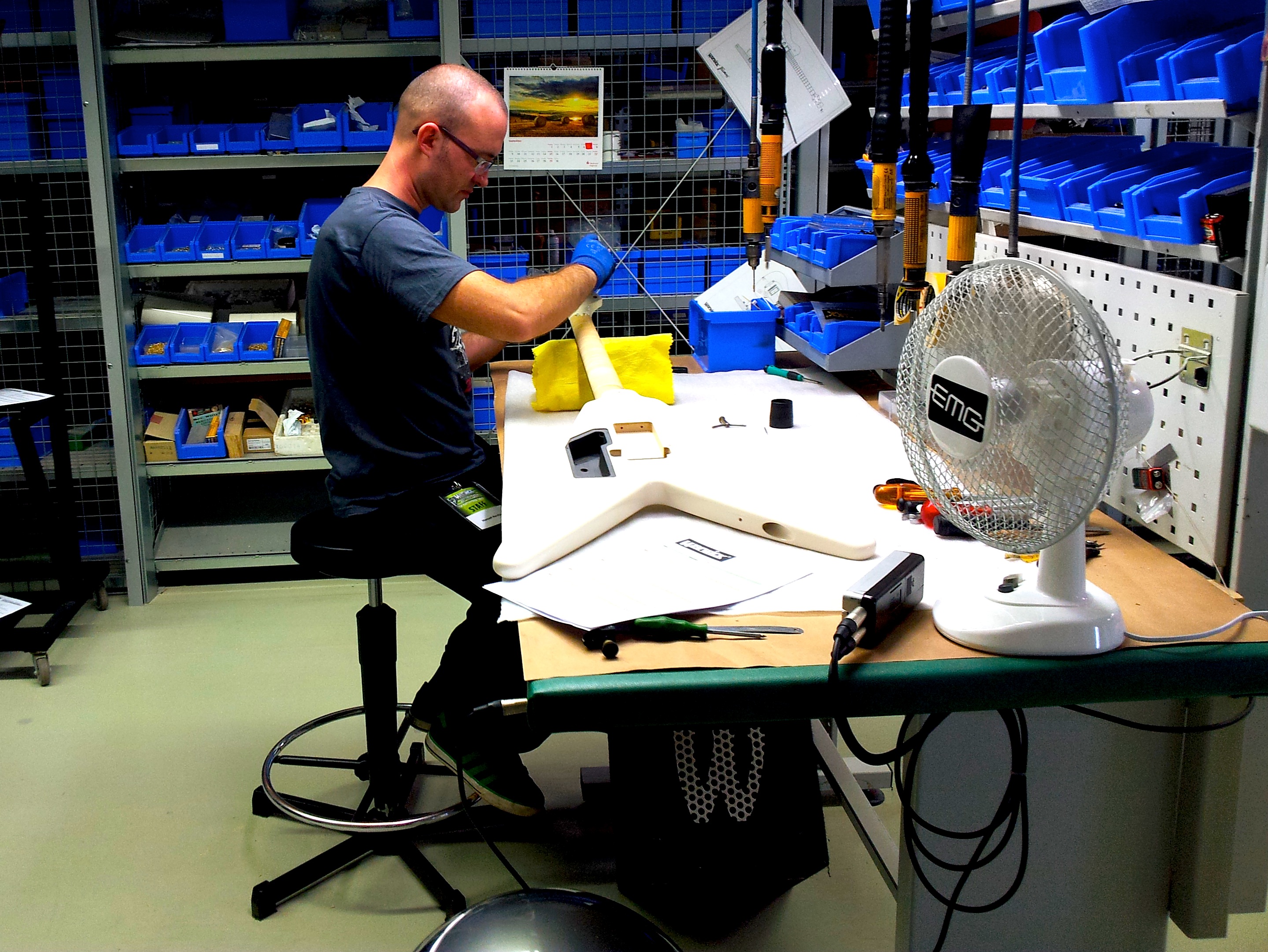
Warwick & Framus Factory Tour
After the lacquering stage, hardware parts, such as machineheads and bridges, are fitted
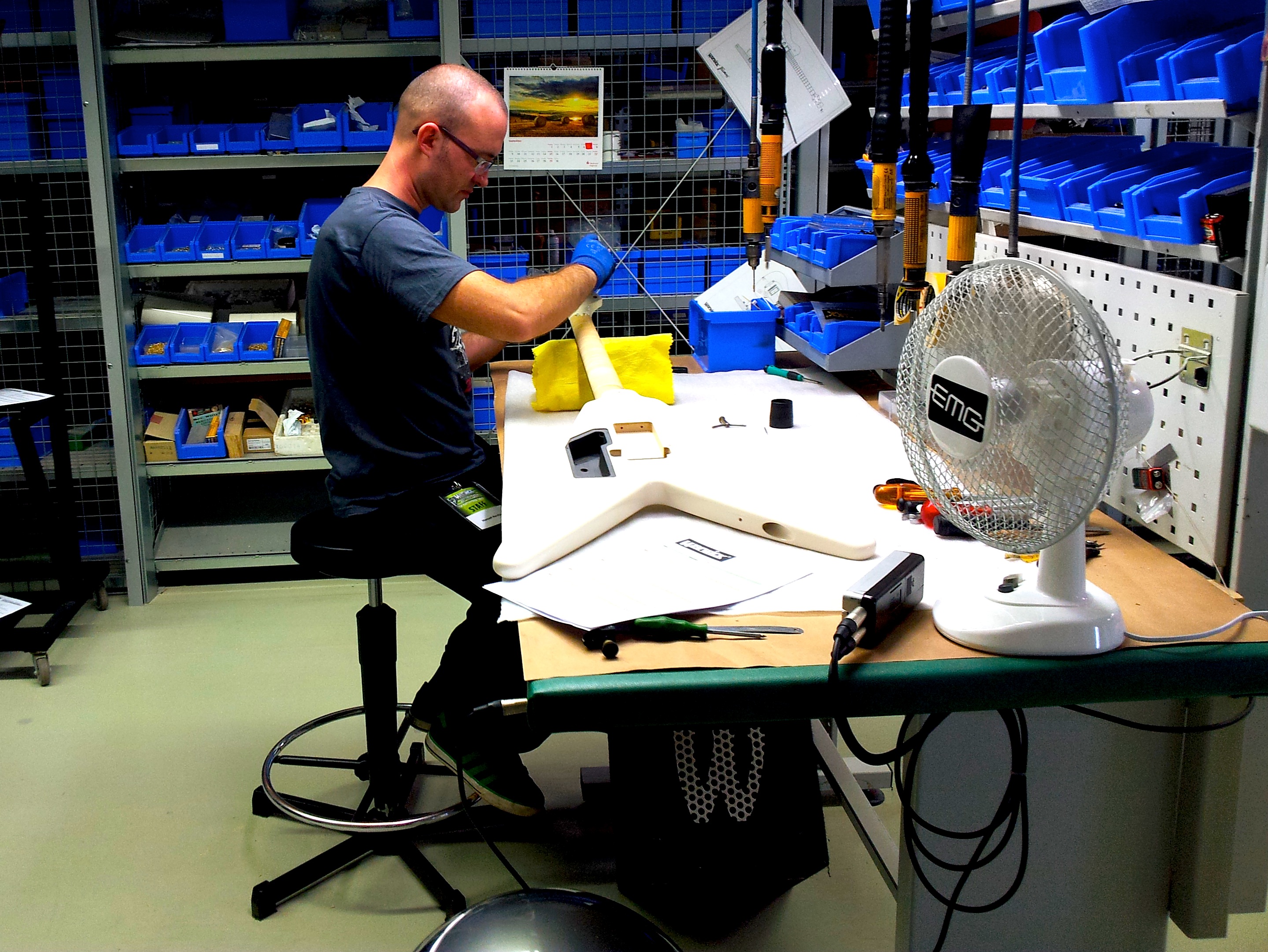
Warwick & Framus Factory Tour
After the lacquering stage, hardware parts, such as machineheads and bridges, are fitted
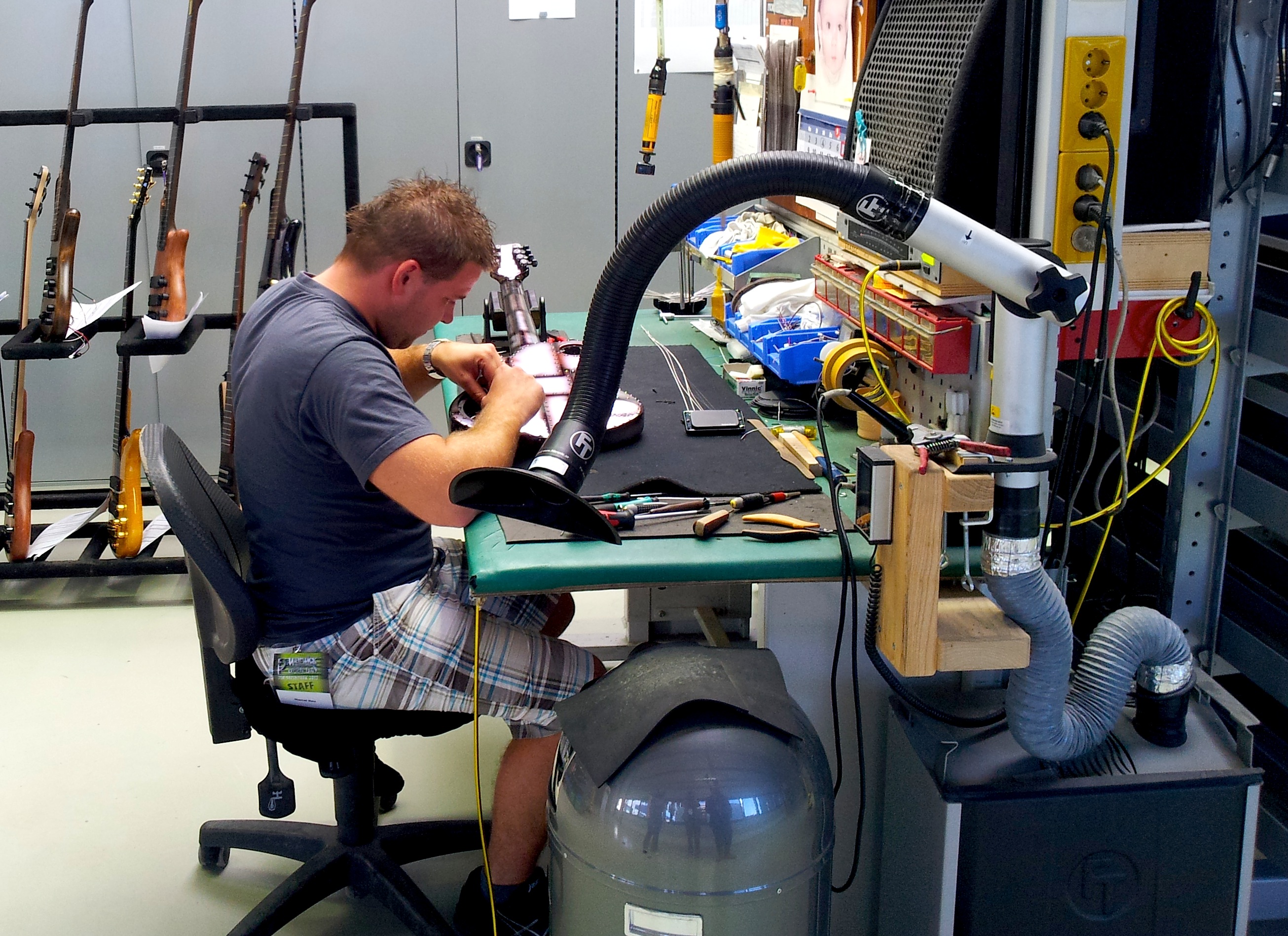
Warwick & Framus Factory Tour
Next come the pickups and electronics
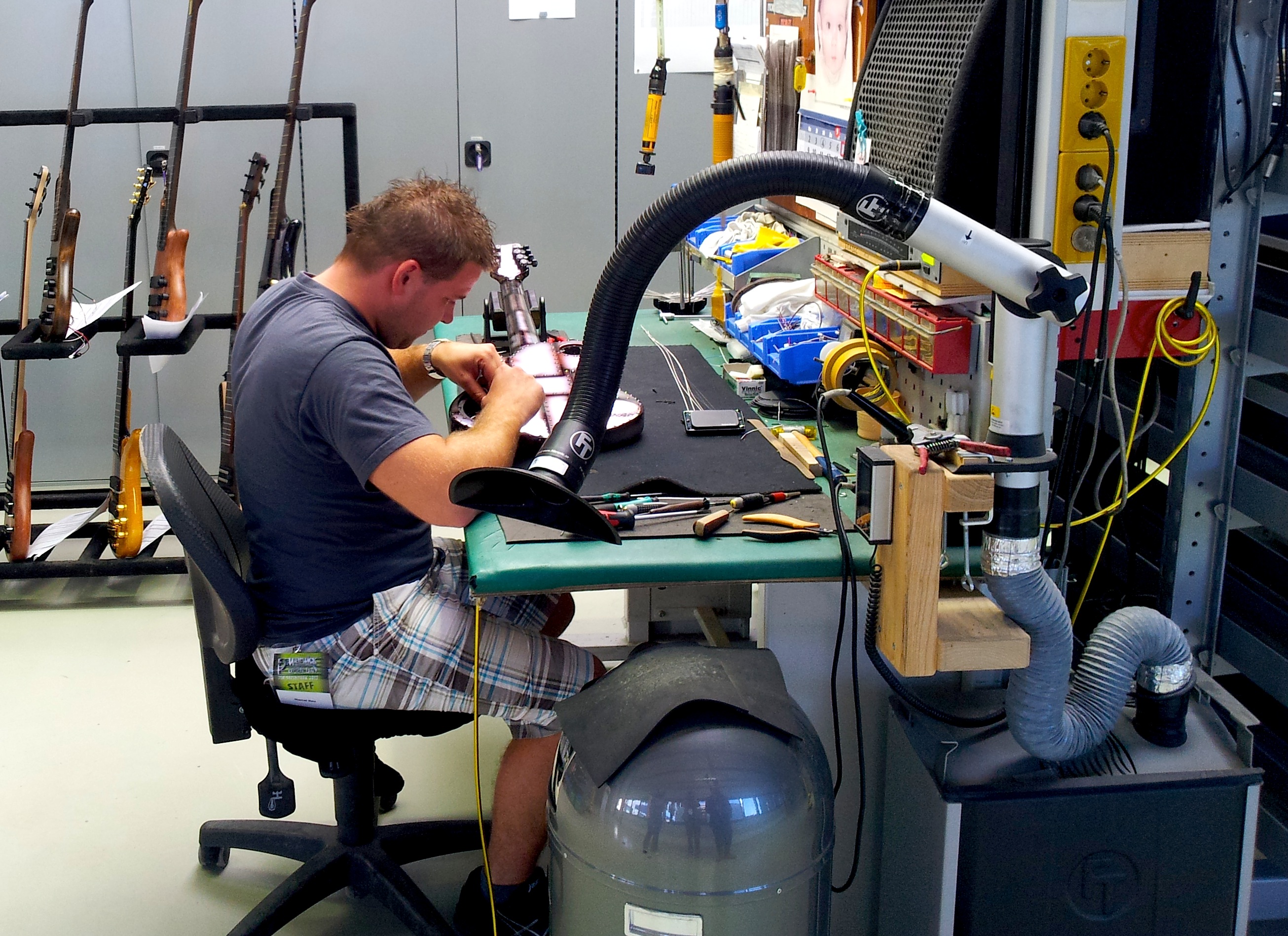
Warwick & Framus Factory Tour
Next come the pickups and electronics
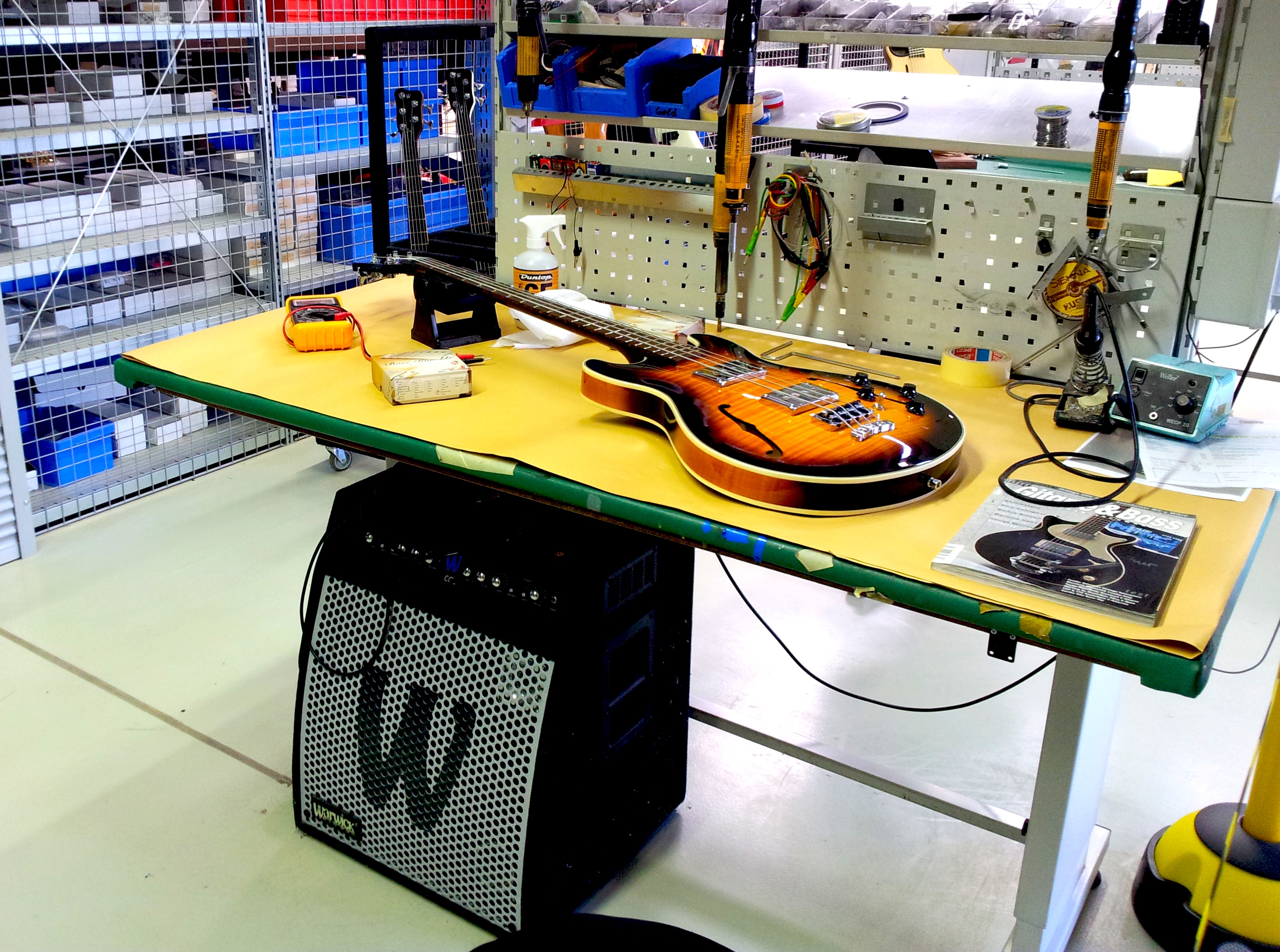
Warwick & Framus Factory Tour
Finally, each instrument is tested for setup and function
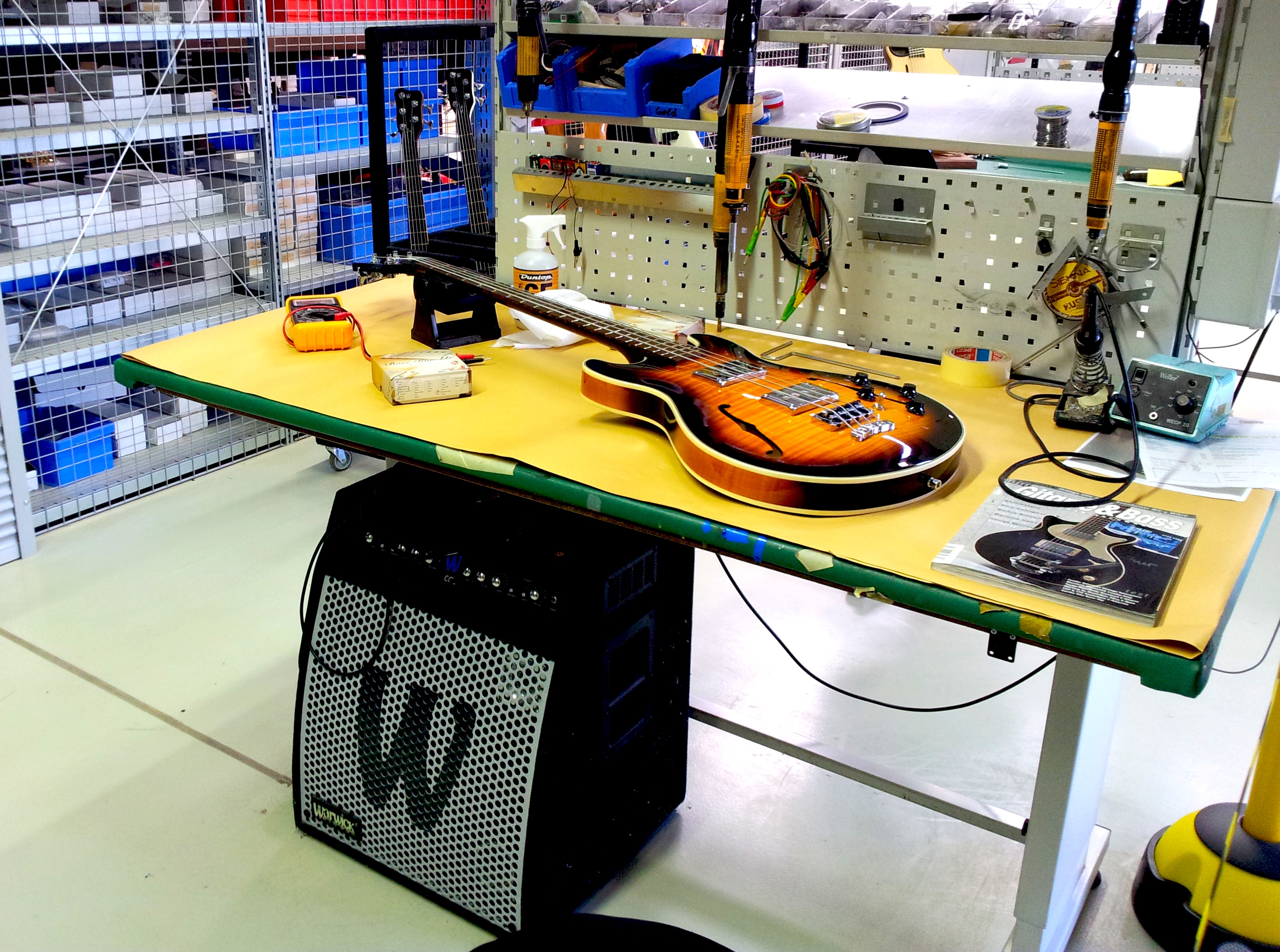
Warwick & Framus Factory Tour
Finally, each instrument is tested for setup and function
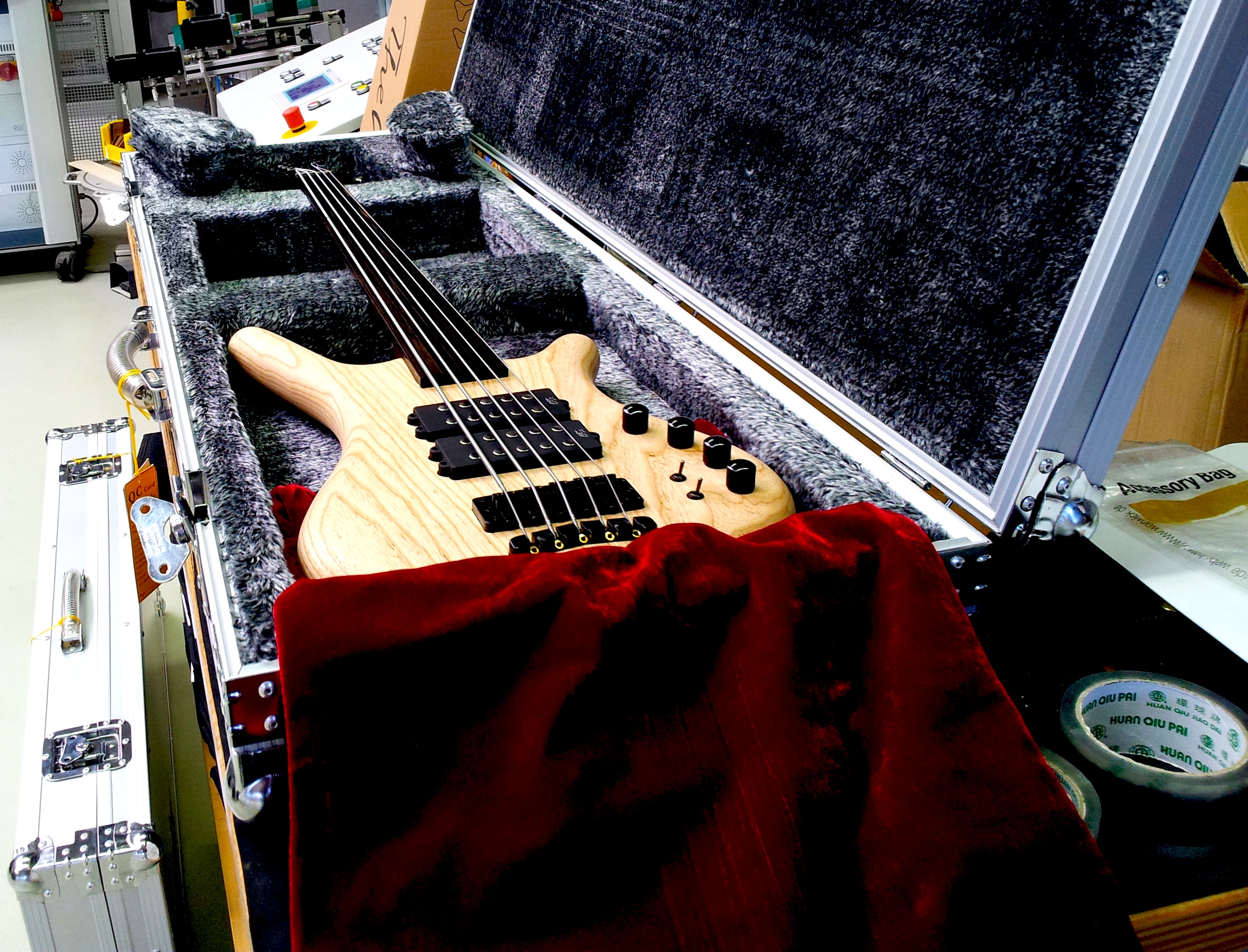
Warwick & Framus Factory Tour
The factory produces around 10 to 15 instruments from start to finish each day
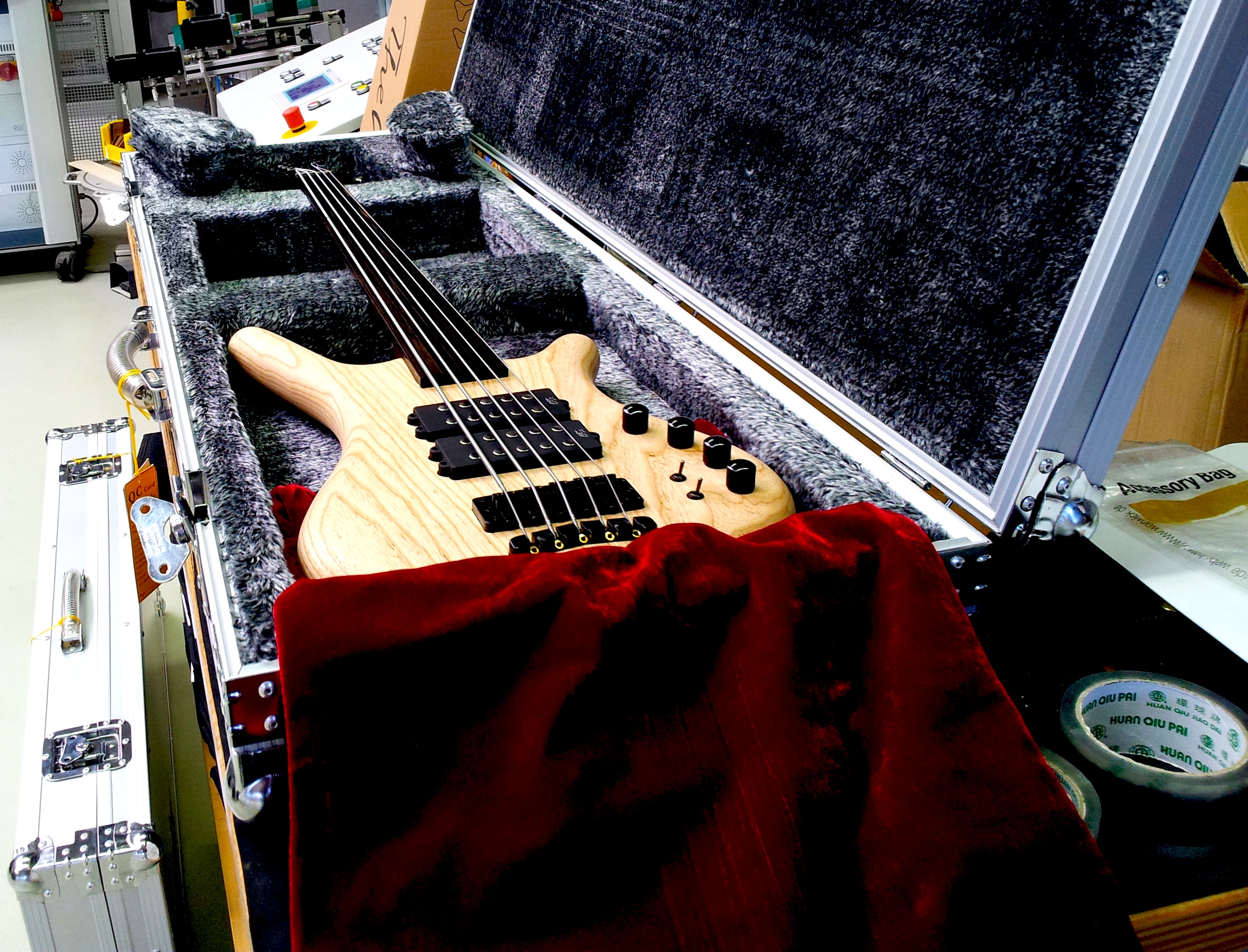
Warwick & Framus Factory Tour
The factory produces around 10 to 15 instruments from start to finish each day
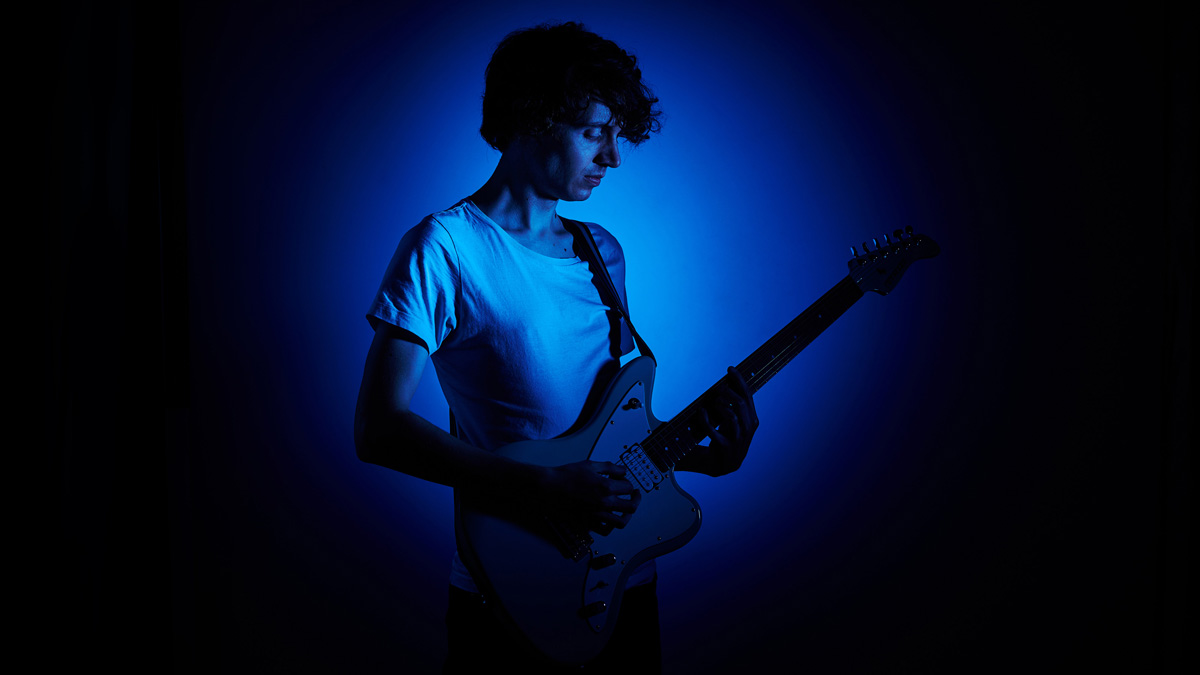
Mike is Editor-in-Chief of GuitarWorld.com, in addition to being an offset fiend and recovering pedal addict. He has a master's degree in journalism, and has spent the past decade writing and editing for guitar publications including MusicRadar, Total Guitar and Guitarist, as well as a decade-and-a-half performing in bands of variable genre (and quality). In his free time, you'll find him making progressive instrumental rock under the nom de plume Maebe.
“A purpose-built solution for bassists seeking unparalleled sound-shaping capabilities”: Darkglass Electronics unveils the Anagram Bass Workstation – a state-of-the-art multi-effects for bass guitar with neural amp model support and a 7” touchscreen
“I don’t think they’re New Order. They don’t sound anything like them”: Peter Hook takes aim at his estranged bandmates
“A purpose-built solution for bassists seeking unparalleled sound-shaping capabilities”: Darkglass Electronics unveils the Anagram Bass Workstation – a state-of-the-art multi-effects for bass guitar with neural amp model support and a 7” touchscreen
“I don’t think they’re New Order. They don’t sound anything like them”: Peter Hook takes aim at his estranged bandmates