Handwired vs PCB amps: what's the difference?
Three amp gurus debate the pros and cons
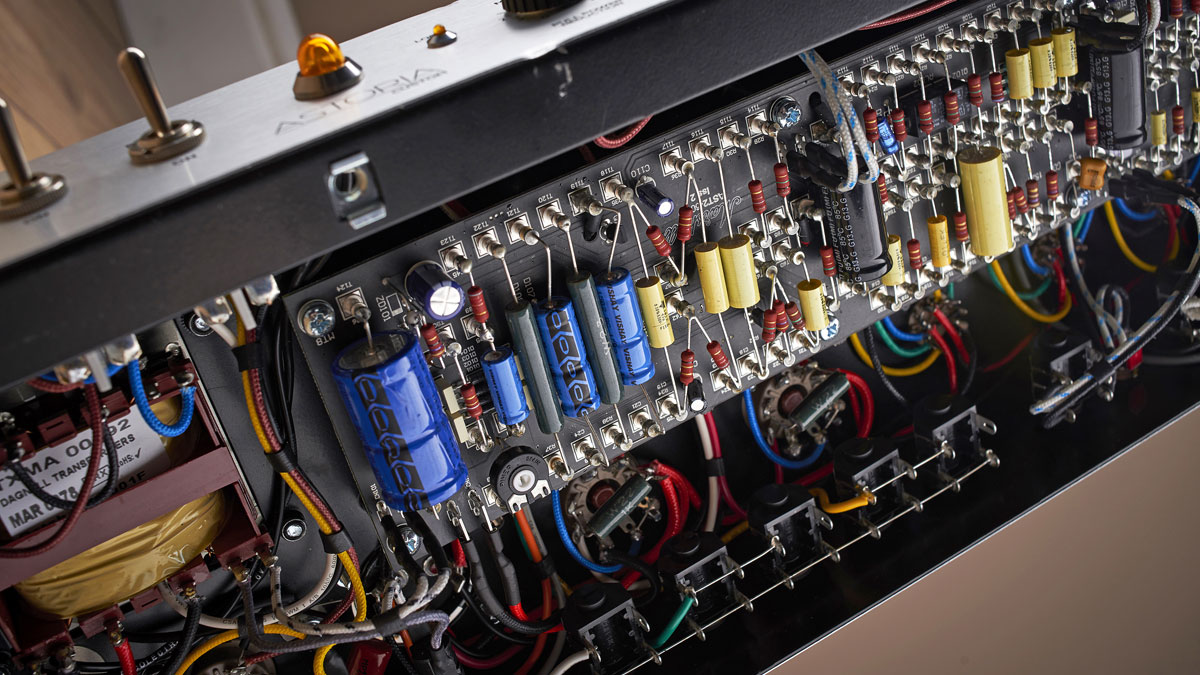
One argument has sparked heated debate among toneheads for decades: which amps sound best? Hand-wired exotica or amps with precision-made printed circuit boards for maximum tonal consistency? We join three amp design gurus to thrash it out...
Some purists argue that amplifiers whose circuits are hand-built by means of point-to-point construction will always sound better than amps built using mass-produced circuit boards, known as PCBs.
It certainly appeals to our sense of craftsmanship to think that the human touch must always yield a better sound than machine-made circuits. But PCB-based amps, if carefully designed and built, can actually perform better than hand-wired amps. Marshall's new Astoria (read our full review), meanwhile, uses a hybrid of both construction techniques.
So which should you go for? As always, it pays to understand the factors that make for great tone and roadworthiness, then make a genuinely informed decision.
Point-To-Point Construction
Let's start with point-to-point. So, what exactly is it? Point-to-point actually covers a variety of different construction methods.
Fullerton-era (pre-1986) Fenders used an eyelet board: a flat piece of fibreboard with rivets punched into it and the components soldered into the rivets.
Point-to-point actually covers a variety of different construction methods
However, the valve bases and front- and rear-panel components were all wired by hand. In contrast, many early British amps used turret or tag-boards, thin strips of Bakelite with a row of solder lugs or turrets running down both sides, which the components were soldered to.
Get the MusicRadar Newsletter
Want all the hottest music and gear news, reviews, deals, features and more, direct to your inbox? Sign up here.
These methods are often called point-to-point, although there's a school of thought that says proper point-to-point actually does away with tag boards and eyelet boards - each component is literally soldered to the next.
This is the purest method of building, but also the most time-consuming. Not only does everything have to be manually fitted and soldered, but each unit has to be tweaked to ensure it matches the prototype for tone and noise performance.
Early examples of Hiwatts and the original Matchless amps were point-to-point. Today, very few commercially available amps are built using proper point-to-point, although Carr is one notable example.
Other builders, such as Divided By 13's Fred Taccone, use uprated versions of Fender's eyelet board.
Printed Circuit Boards
The original idea of printing copper tracks onto an insulating baseboard dates back to the 1920s, but it wasn't until after the end of WWII that printed circuit boards were manufactured in high volumes.
There are dozens of different kinds of printed circuit board, from very simple single-sided ones with copper tracks glued to a base of GRP or similar material, to complex multi-layer types used in computers and aerospace.
The most common types you'll see in a guitar amp are single-sided or double-sided and through-plated, where at each hole for a component lead there's a tiny metal tube that connects one side of the board to the other, with a track on one side and a solder pad on the other.
Once you have the perfect layout, a printed circuit board can reproduce it again and again
When a component is soldered, the solder passes through the tube by capillary action, securely locking the component in place on both sides of the board. This gives an added resistance to failure when a circuit board is flexed - for example, when a valve is replaced.
The most important point for manufacturers, however, is that using printed circuit boards allows automation of the soldering process. Instead of soldering each joint one at a time, you can fit all the components and then pass the board over a bath of molten solder, soldering everything in one pass - a big timesaver.
It's not all plain sailing, however. Some types of PCB don't like repeated heating and cooling. Repeated heating from valve bases and pins and subsequent cooling can cause copper tracks to work-harden, and, over time, tiny fissures appear, slowly changing tracks from conductors into resistors. In high-current locations, the increased resistance eventually results in a burnt-out track.
Additionally, the heat from a valve base is not far off the melting point of some solders, making dry joints more likely. Factors like these are part of the reason why printed circuit boards in some guitar amplifiers had such a bad press in the early days. Today, however, better materials make PCBs more resistant to heat and far less likely to fail.
Also, high-gain valve audio circuits are very sensitive: a change in wire or component placing of as little as one millimetre can sometimes make an audible difference in the overall quality of an amp's tone.
This is, of course, where PCBs shine: once you have the perfect layout, a printed circuit board can reproduce it again and again, with an accuracy that's impossible to achieve with hand wiring. For this reason, many high-end amp makers such as Reinhold Bogner and Mike Soldano use very high-grade PCBs, with extra-thick base material and double- or triple-thickness copper tracks.
As well as these two distinct routes, you'll also sometimes see a blend of both technologies side by side. High-end products such as Tone King's Royalist or Marshall's Astoria use quality printed circuit boards for consistency, with hand-wired valve bases and switches for enhanced reliability.
In our experience, the best results often happen when these different methods are combined in an intelligent, appropriate way.
Matchless amps have an enviable reputation for expert point-to-point construction
Ask The Experts
That's the general outline of the debate. But what do the pros think? We asked three highly regarded amplifier and audio electronics designers for their thoughts…
Adrian Emsley is the designer behind all Orange products, from its highly successful budget Crush line, to the hand-wired Custom Shop limited editions, which are often wired by Emsley himself.
"Printed circuit board and point-to-point amps have several main differences," he says. "One good thing about point-to-point is that you can use big polyester caps and decent-sized resistors. These components also have a big influence on the sound of the particular amp you are trying to make. Point-to-point is normally very easy to service, as well. I tend to use it for the more simple designs as that's where it really works the best.
I tend to use point-to-point for the more simple designs, but there's nothing wrong with a good PCB design if it's done right - Adrian Emsley, Orange
"But there's nothing wrong with a good PCB design if it's done right," he continues.
"A good sorted layout can perform better in some ways than point-to-point, especially in more complex circuits because things tend to be more localised, not to mention easier to fit in. Two-ounce copper for the tracks is definitely the way to go when making tube amps using a PCB. This sounds better, is more reliable and is also more serviceable.
"I always use curved tracks with no corners or cut corners, as it winds up sounding more musical and with less noise. We tend to use PCB track eyelets with any cables being hard soldered to them. We still call this PCB though, not 'hybrid'."
Mark Bartel is the founder and designer for Tone King, one of the world's most coveted boutique brands, and well known for the exhaustive research and development that goes into its products.
"I've designed scores of amps over the past 25 years using both PC boards and various forms of hand-wiring. I prefer to use a combination of PC boards and hand-wiring to achieve the best layout in terms of sound quality plus reliability and serviceability.
"Proper use of well-designed PC boards can offer real, quantifiable advantages over hand-wiring schemes in terms of component placement, wiring length, and wire routing, which translate to improvements in both sound quality and serviceability.
"An important goal of proper design is to minimise wire length and to optimise relative positioning of the components. Many hand-wiring schemes may look beautiful, with the components all in a row, long runs of parallel wires, and nice right-angle bends, but these aesthetic conceits are often the opposite of what good design would dictate from an engineering perspective.
"We've built thousands of amplifiers with PCB construction over the past 23 years, many of which have been in constant touring use all over the world. To date, we have seen exactly zero problems with the boards in any of these amps."
A well-laid-out point-to-point circuit is a thing of beauty; however, it's labour-intensive and skilled work - Phil Taylor, Effectrode
Phil Taylor is a noted authority on the history of the Mullard Valve Company, and the founder and designer for Effectrode, whose unique valve-based pedals are found in the pedalboards of artists including David Gilmour, Peter Frampton and Billy Corgan to name but three.
"If you've ever looked inside a vintage Hiwatt amp, you'll see a fine example of point-to-point wiring where the small components - resistors and capacitors - are mounted on tag or turret boards.
"A well-laid-out point-to-point circuit is a thing of beauty; however, it's labour-intensive and skilled work. Each component must be soldered in position by hand and care has to be taken when bending and forming component leads to prevent stressing and damaging them.
"Contrast this with printed circuit boards, where the wiring patterns are chemically etched into copper foil laminated to epoxy impregnated fibreglass board. The PCB is designed so that the components can be precisely placed in position with minimal or no bending of component leads. This not only prevents component damage, but it also simplifies and speeds up assembly, making it possible to automate the process using machines.
"There are a couple more advantages when using a PCB: they can be designed with additional copper layers for ground and power, allowing the circuit layout to be optimised for low-noise performance and reduce its size.
"Secondly, component lead lengths are kept to a minimum - sometimes there are no leads at all - reducing the number of solder connections, ensuring highest signal integrity and reliability."