Inside the British Drum Company with Al Murray, Ian Matthews, Keith Keough and more
An exclusive glimpse into the world of the newest face at the forefront of the drum world
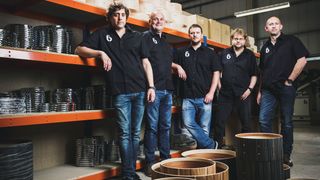
Inside the British Drum Company
It’s blazing hot summer’s day in Stockport – no sign of rain in Cheshire, and how often can you say that?
In the offices of the British Drum Company the positive atmosphere is heartening. Main-man and master drum builder Keith Keough says, “We purposely put this team together. We wanted these particular people.”
His co-director, Al ‘the Pub Landlord’ Murray, is more colourful. “This is like Charlie Bucket’s Golden Ticket and I have won the factory and he is Willie Wonka! Make no mistake, what Keith is doing is really brilliant and the fact we have this deck of incredible people with their different approaches and abilities – we have all won the golden ticket.”
This is like Charlie Bucket’s Golden Ticket and I have won the factory and he is Willie Wonka! - Al Murray
Those people are Kasabian drummer Ian Matthews, design engineer Alan Kitching, and marching band specialist Stu Warmington. You can’t imagine a more lively, committed team. Aside from these five partners, respected music industry veteran Dave Hunt (also a percussionist) is sales manager. And Keith has a small team of skilled sidekicks down in the workshop.
First is fellow artisan Tim Boyle, who’s been with Keith through the past decade. Then there is shell building specialist Duncan Tawse, while Vicky Batrak does part-time assembly work.
We’re here to see exactly what the excitement is about and to achieve a long-held ambition to build a snare drum with Keith. It’s something we have talked about for years, back to when Keith had his first company, KD (Keith Davidson) Drums. He was a key figure in the new wave of UK custom drum builders – Noonan, Highwood, Guru, Jalapeno, Liberty, VK and others – who started to emerge around the millennium. These companies’ drums have proved as good as any in the world.
In a nut shell
Keith has an enviable reputation as one of the best drum-shell builders around today. With his fine-woodworking background in cabinet-making he is forever experimenting and refining his shell-making and finishing skills.
We have examined thousands of shells over the years and Keith’s always stand out as among the best.
He has, for example, the ability to construct shells with ultra-thin plies which are strong, stable and accurately round. a 12-ply shell might be as little as 4mm thick. People may think the glue stifles the shell, but Keith says it’s the other way round. With the two secret types of adhesive BDC uses, “the glue is harder than the wood, so if anything it is the wood dampening the glue”.
Another nifty off-shoot of the BDC process is that plastic laminate wraps can be treated the same way as an outer wood veneer – ie: cut and placed in the mould first, so the wrap is perfectly adhered to the shell and fits right up tight to the bearing edge. It’s part of the shell, not an addition. this also means the overall shell diameter remains that of the mould. Whereas adding a wrap to a finished shell increases the shell diameter, fractionally distorting lug rod angles and so on.
“We make our plies in-house from single-leaf veneers to our special lay-ups,” Keith reveals. This allows BDC to investigate any feasible horizontal and vertical ply formulation, using many species of timber, both familiar and rare. “horizontal plies produce higher tones because of the strain and pressure the wood is under when bent, while vertical plies give a deeper, darker tone as this is closer to the wood’s natural form.”
Such considerations (and there are many more) are just the start, the crucial basis of the shell, but then BDC may insert reinforcing rings, cut bearing edges to various angles, with sharp or rounded profiles. Then there is the finishing using special blended oils, natural and environmentally harmless.
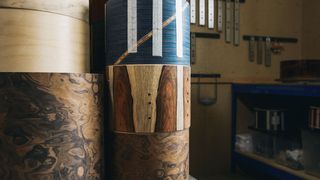
Enter the landlord
For several years up until last summer Keith built drums for Premier. He was responsible for bringing back UK hand-built drums to our most historic drum company. When that association ended things fell into place remarkably quickly, with timely help from Al Murray.
Al actually started drumming around age nine, playing orchestral percussion at school, “Because my school was straight-laced and frowned on drum kits. I played in some bands after university when I was starting out in stand-up and I realised I wasn’t – and we weren’t – good enough. The advantage of stand-up is you don’t have to split the money and drive the band around!”
Compering some clinics for Steve White in 2002/3 got Al back into playing properly. “I have played a lot more in the last five years and I still have a band. I am fascinated by drumming and love it but I know my limitations! But when I ran into Keith two or three years ago I immediately thought, if this door opened...
“This time last year I popped up to see Keith to collect a couple of concert toms he’d made for me and we got into a ‘what’s going on’ conversation. I said if you want I’ll talk to my accountant, and that is what we did. And then the team came together.
“I was in Edinburgh for the Festival last August and the boys came up and we sat down and discussed what we were gonna do and looked at some simple things like the badge. Are we all on the same page with the aesthetics? Because that’s a really big thing to get right. We drank on it that evening and never looked back"
The plot thickens
“The thing about launching a company like this is that you have to know you are drawing on the exact areas of expertise and the people are credible,” Al adds.
To that end, the first thing Keith needed was an engineer. Luckily, he had already worked with just the right person. “I can build drums but I am not an engineer,” Keith explains. “I needed Alan (Kitching) to draw them all up.”
Alan introduces himself: “I do all the design work, the engineering, on cad [computer-aided drafting]. I make sure it’s all working for everybody, turning it into something we can manufacture. My background is in industrial/product design, but I’ve been a drummer since my early teens and have been making prototypes and so on. I also have a company called Bullet and Kitch that makes drum pedals.”
Ian Matthews is well known as the drummer with top band Kasabian. “I met Al in about 2005,” he remembers. “Then I bumped into him on [Jools Holland’s] Hootenanny and at the Q awards in 2010/11 where we had a laugh and swapped numbers.
“The following year I went up to the Scottish Drum Fair as a solo clinician. We were all booked into this hotel in Falkirk and afterwards we had a few beers and I met Keith who was also there. We got on like a house on fire, stayed up till 6am talking, and have stayed in contact since. I got Keith into the V Festival [August 2015] which was just after these guys had had their get-together and I realised I have got to do this.
“It took me by surprise, but it was a no-brainer. To not just play the drums but to be involved with the design and development is an amazing opportunity any drummer would love to have.”
So Ian’s role is much more than just an endorsee. “I am the drum kit boy, representing the company when I go out onto the big stage with Kasabian. But also my role is as a barometer for drum kit players. I play a lot of styles."
Al adds, “That is the thing Ian brings – someone on the frontline, recording enormous records using our equipment in the studio. He’s not some niche drummer either; he’s a drummer for everybody. That is something we are really proud of. Again it speaks of our ambition, we are looking to the mainstream, not to be a custom house for custom drummers.”
Keith agrees, “Over the years I have learned that we don’t want to be a custom maker saying, ‘You can have this shell with this lug and this finish,’ etc. We want to be a mainstream brand. When we launched last November we’d only had two months to get off the ground. We had to use generic lugs, but in the process we have tooled up, so we will soon have all the drums, from marching to orchestral, looking like one big family.”
The use of generic lugs and fittings is widespread all around the world. Nothing wrong with that – and some generic parts, like metal hoops, are unavoidable. But BDC’s ambition to be a major mainstream manufacturer demands an all-embracing brand identity with distinctive cast lugs and unique hardware solutions. That cannot happen overnight. It requires extensive thought and investment.
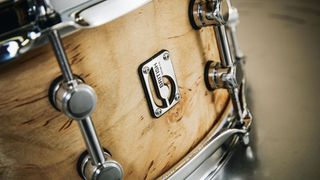
Marching to their own beat
At this point the BDC team shows us prototype lugs and other hardware innovations in development. Every aspect of kit design is under intense scrutiny. For example, we see variations on 3D-printed ball-shaped floor tom leg feet which permit resonance in all directions, not just up and down.
There is already the charismatic stencil badge, but perhaps most significant for brand identity is the final lug design. Keith describes this as “between Ludwig and Beavertail”. Featured first on the company’s Bluebird snare – available soon – the lug has Ludwig imperial ridges on a flared bow-tie casting. there are single-ended and double-ended variations in various sizes.
Engineer Alan explains the team’s approach. “We’re aware of all the different drum lugs out there and with our own lug design, if we came up with something that was too strikingly new and different it probably would date, so we wanted something that was hopefully timeless.”
“A lot of manufacturers fall down on the aesthetics,” adds Ian. “So we also have to make the drum kit look right: ‘This is the kit you want to be seen with.’ I played the drums in front of 52,000 people last weekend [King Power stadium, Leicester City’s Premiership celebration] and 130,000 people two weekends before. And those drums absolutely worked, there is absolutely nothing lacking. [We got] positive feedback from the finest engineers in the country, working for us.”
Stealing a march
The name British drum company was chosen in part because of its attraction to the marching band scene. Keith reveals, “The main target was the marching world. British drums are huge in China, they are mad for the British. And in Northern Ireland marching is massive.”
This is where Stu Warmington, a long-serving royal marine, comes in. Stu explains that the plan is to cover all three areas of the marching world: traditional, pipe bands and drum corps.
This involves different drum styles: “Pipe bands use high tension drums with fixed top and bottom snares; drum corps have high tension with fixed bottom snares, but also use multi-toms and quads and multi-tuned bass drums. The traditional area is a military style of drum which can have single or parallel snares.”
The attraction of producing a whole bunch of drums for a band is obvious. Stu explains, “Once you have the drum, they all have the same heads and snare strainer, etc.” But once again, BDC is determined to come up with superior designs.
Keith’s shell construction mastery scores here. “The main thing is the weight,” he says. “We have designed this shell that’s 12 plies but just 4mm thick. It is really thin and light but super strong.”
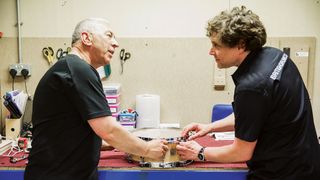
United ambition
Spending time with the team, witnessing their undeniable enthusiasm, there’s an excitement, ambition and work ethic clearly shared by all. The name, British Drum Company, is a bold statement of intent.
Keith modestly offers, “We did not want it to be Keough Drums, tied to one person. It’s not about me. If I were to leave I would want it to carry on.”
Nevertheless it is Keith’s pre-eminence in shell building – the heart of the drum – that has led us here today. We have championed new British drum builders who have sometimes had a hard time of it when competing with the perceived glamour of American boutique marques – more often than not consisting of bought-in Keller shells and generic hardware with bling finishes.
People thought Ludwig and Gretsch were dead but look what has happened with them. Opinion can be turned in just a few years. There’s no reason we cannot do that here.
But Ian, a hitherto DW endorsee, points out the Americans have gone through the ringer too. “DW saved the American drum industry from the [omnipresent] Japanese. And people thought Ludwig and Gretsch were dead but look what has happened with them. Opinion can be turned in just a few years. There’s no reason we cannot do that here.”
Al adds: “There was a period in the UK where no one could speak any good about any UK manufacturer at all. There was almost an appetite for disaster – the rumour would be, ‘They are about to go under,’ – like they almost wanted it to happen. It would be no bad thing to buck some of that trend.”
Last word to Keith: “We will do cajons, marching drums, practice pads and we also have cool things like polishes. By the end of the year we will have our own lugs across all our ranges. It will all look like a family. That is a crucial statement of intent. In 10 years time, who knows?”