12 steps to building a British Drum Company snare
We build our very own BDC snare!
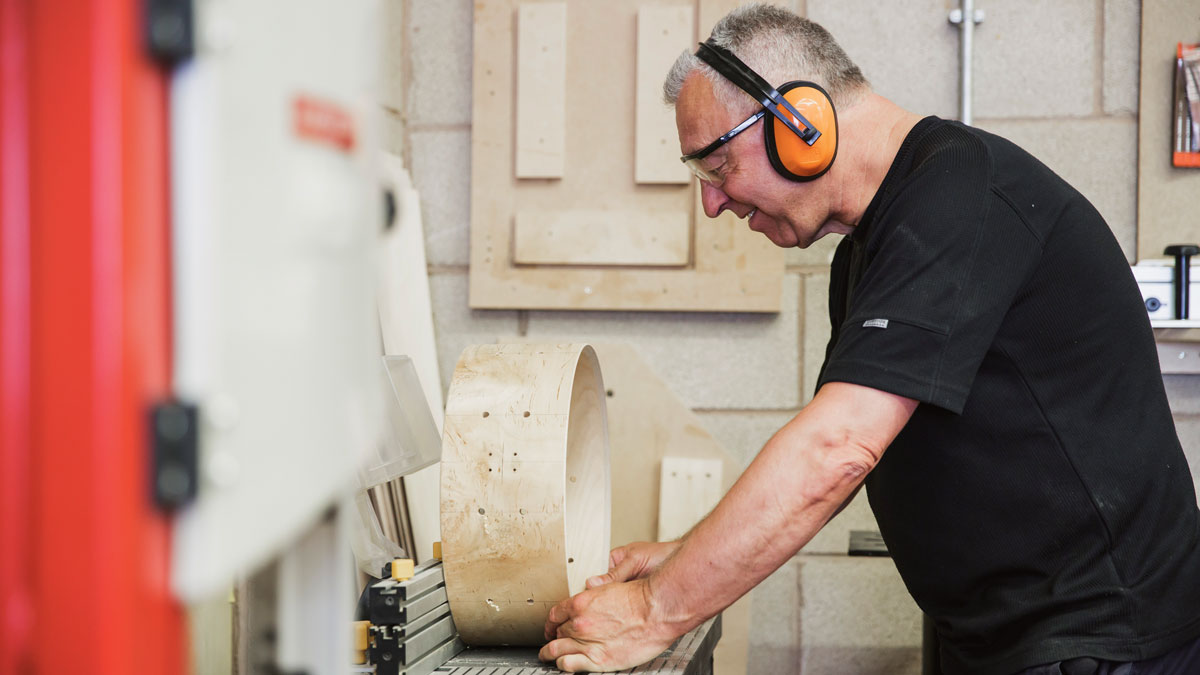
Building a BDC snare
The British Drum Company was launched late last year by a crack team of industry professionals.
Amongst this A-Team of drums and percussion are Kasabian’s Ian Matthews, master drum builder Keith Keough comedian (and accomplished sticksman) Al Murray, marching and expert Stu Warmington and engineer Alan Kitching.
So, when we received an invite to head up to the firm’s HQ, meet the team and make our own snare drum, well, we couldn’t say no.
What you see on the pages that follow is the making of that very snare, as we present the 12 steps to creating a British Drum Company Merlin snare drum.
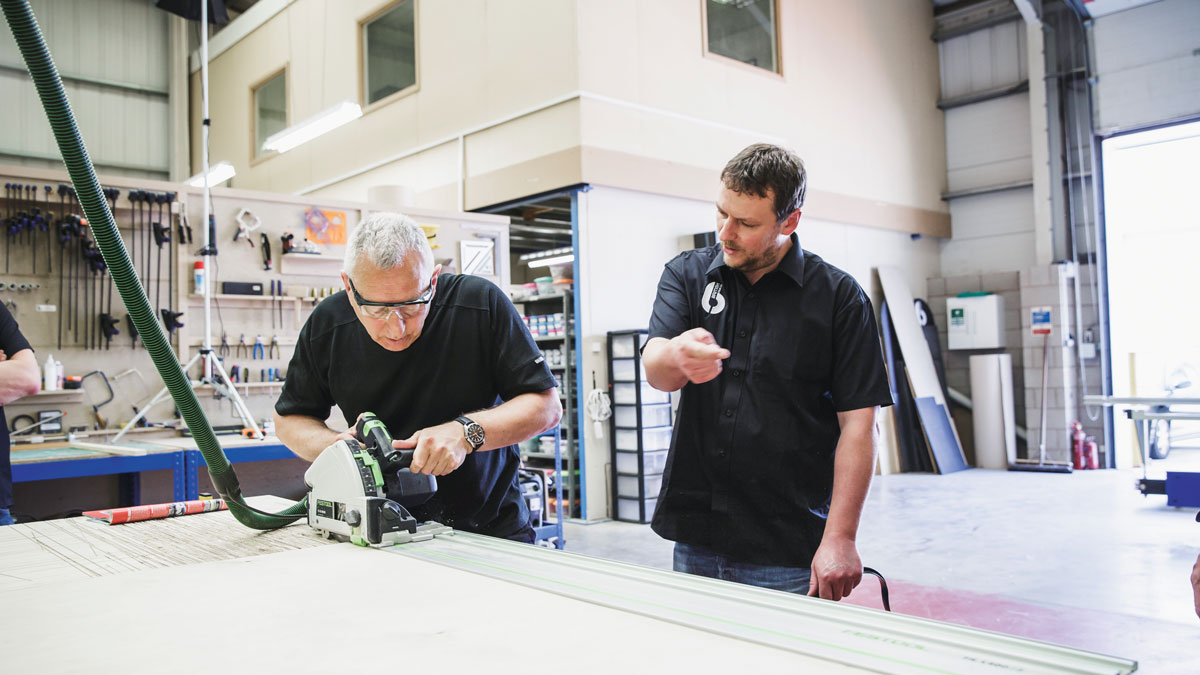
Cutting the shell
Lengths of plywood are cut down to roughly the depth of the finished drum (around 6" for the 51⁄2" drum) using the impressive table saw.
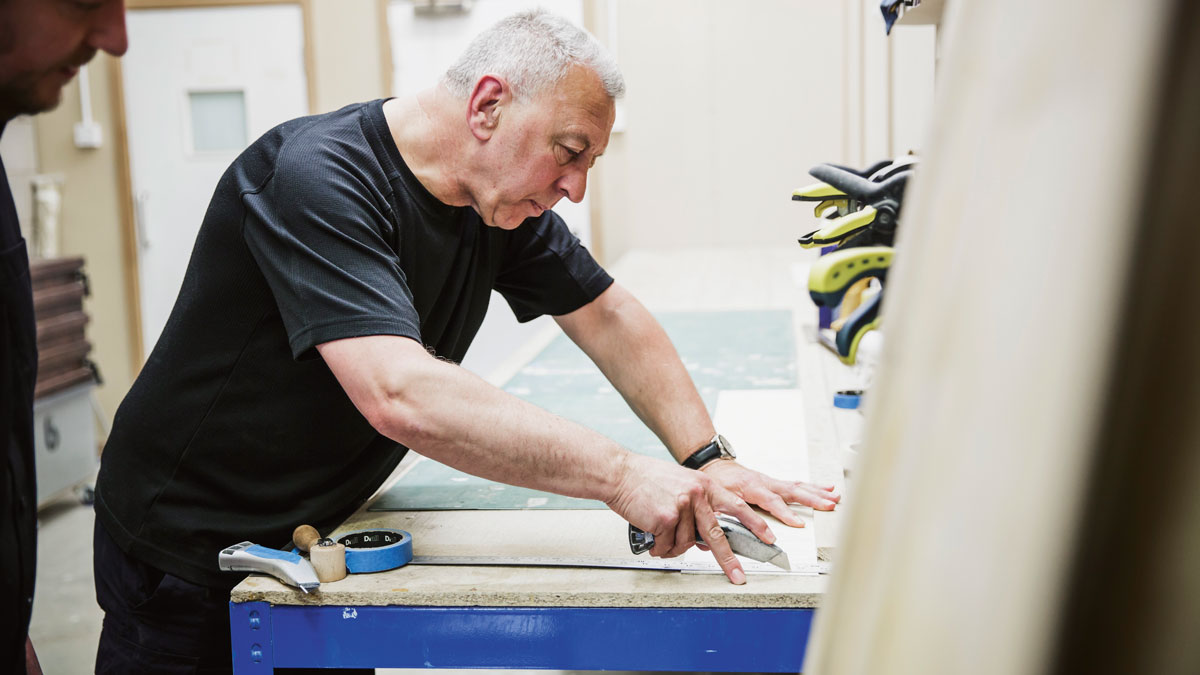
Measuring
Each individual 3-ply or 2-ply length of birch or maple (or final veneer) is placed on the measuring bench and using a fixed steel edge ruler set to give a 5° diagonal seam is sliced off using a craft knife, which gives the cleanest of cuts.
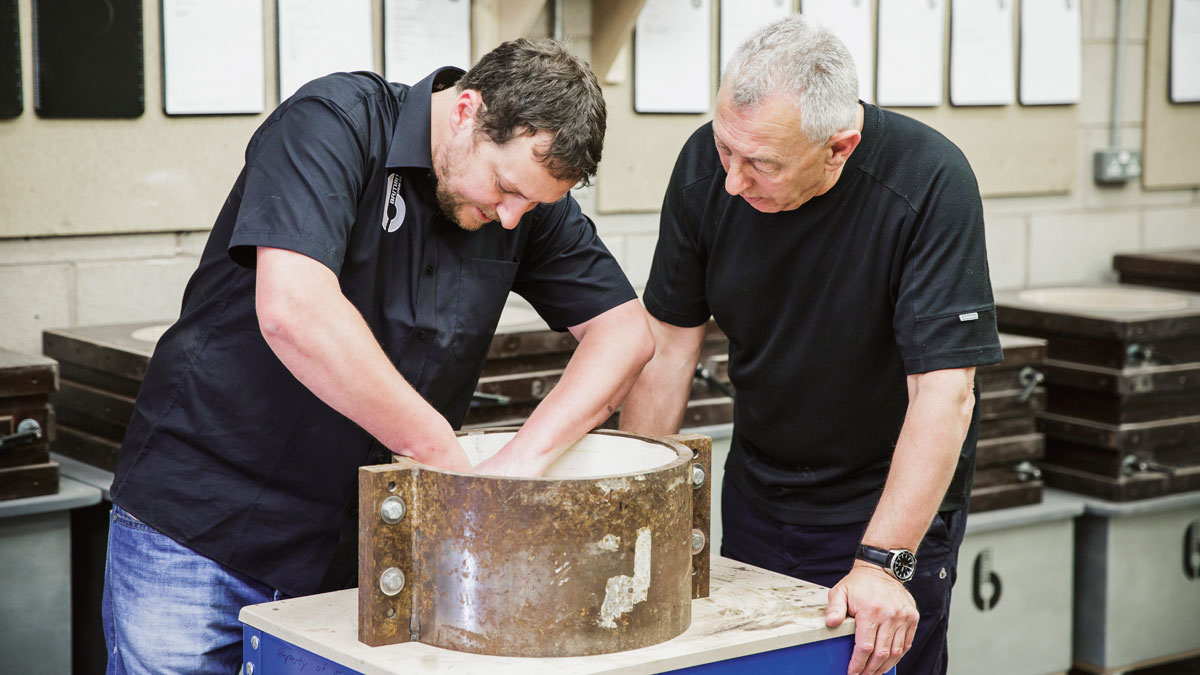
Steel moulds
Keith demonstrates the tricky technique of slipping the individual plies into the super-heavy steel mould.
This involves getting the sheet the right way up, holding one end in place while the other is bent in an ‘S’ then snapped into place.
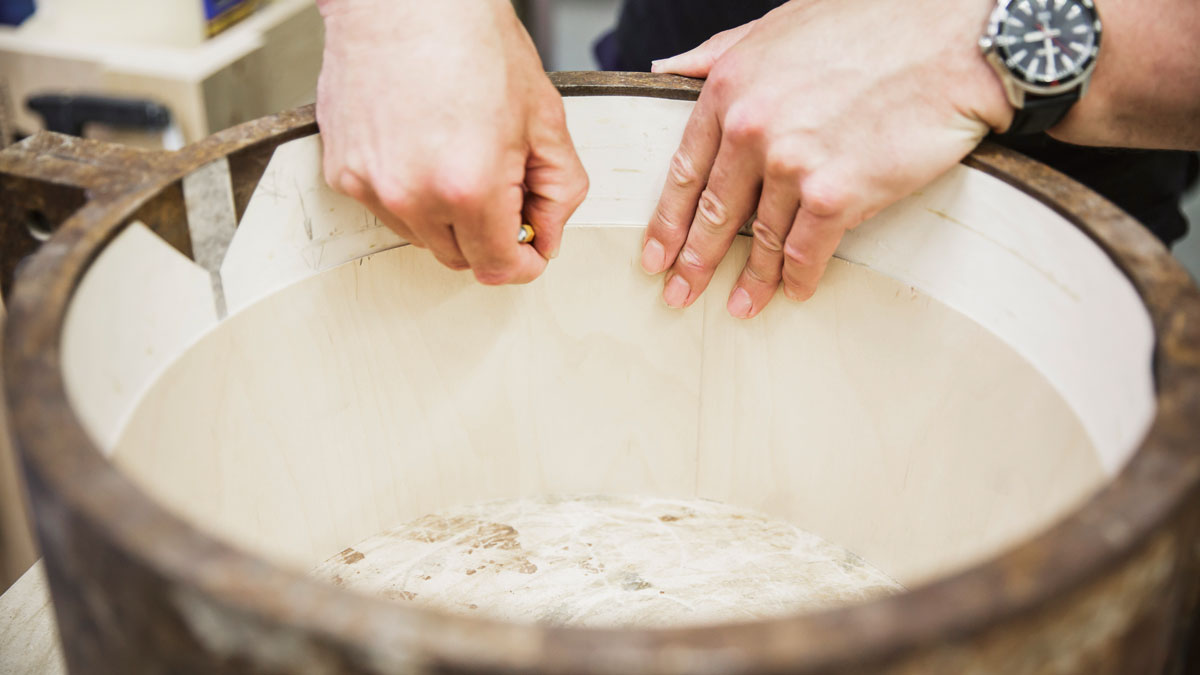
Slicing the ply
The amount of ply to be sliced off is marked in pencil on the inside of the overlap.
The length of the sheet is deliberately fractionally oversized and may need shaving one more time for a super-tight fit. Overlaps are inserted at 90° to each other each time, ensuring joins are staggered around the shell.
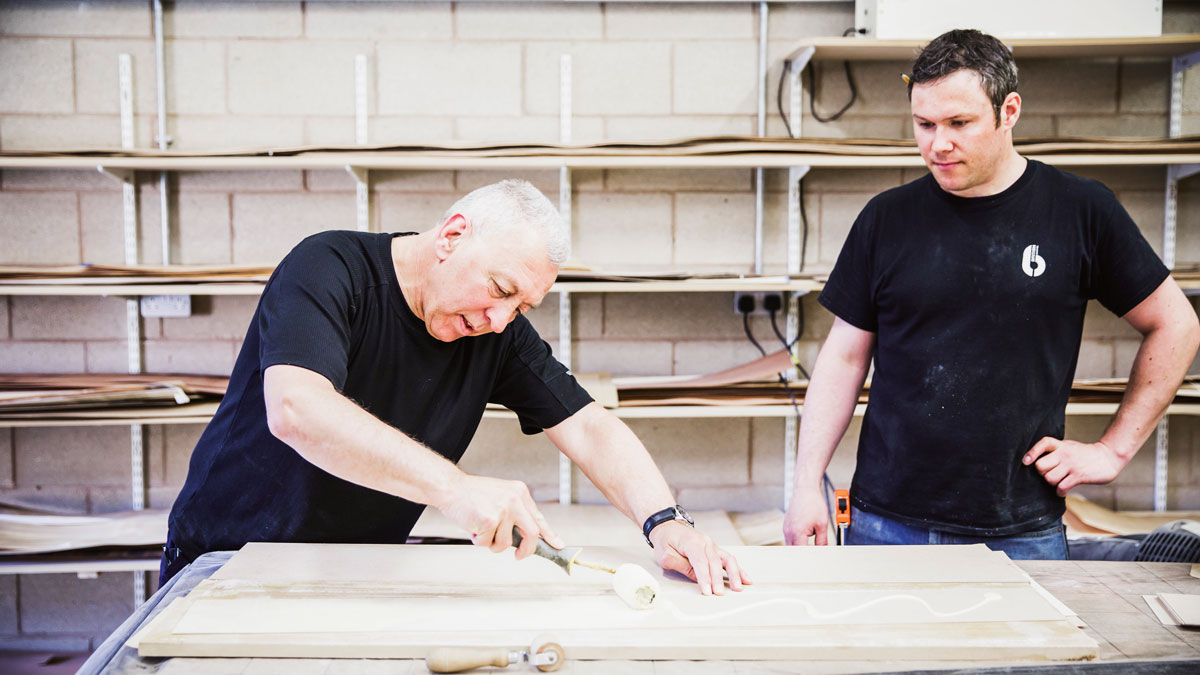
Adhesive
Overseen by shell-specialist Duncan Hawse, Geoff now rolls on the adhesive ready for the ply sheet to be placed back in the mould.
Once all the plies are in place an air bag is inserted and inflated and the shell left over night to settle.
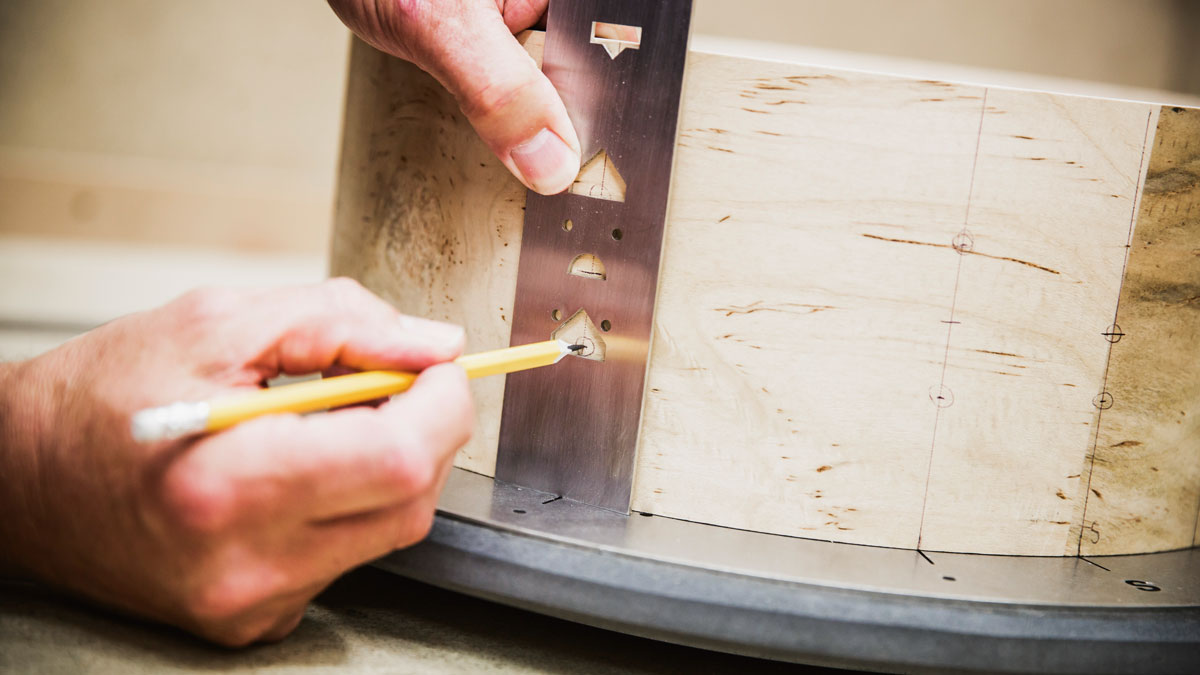
Layout mats
BDC design engineer Alan Kitching has made a complete set of marking-out templates from stainless steel, one for each size and type of drum. He has also made circular stainless steel layout mats.
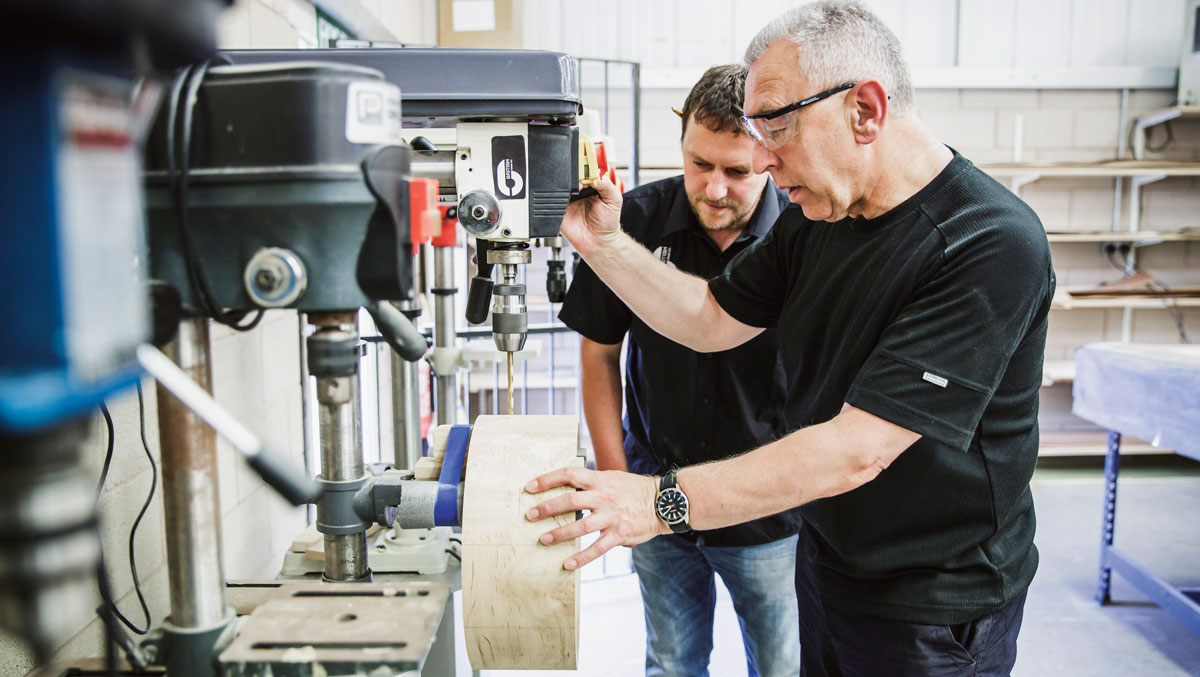
Drilling
Six permanently mounted drill presses are each fitted with the correct-sized bits for making lug mounting holes, air vents, badge screw holes, etc. Again, this is done by hand. No room for mistakes or a shell will be ruined!
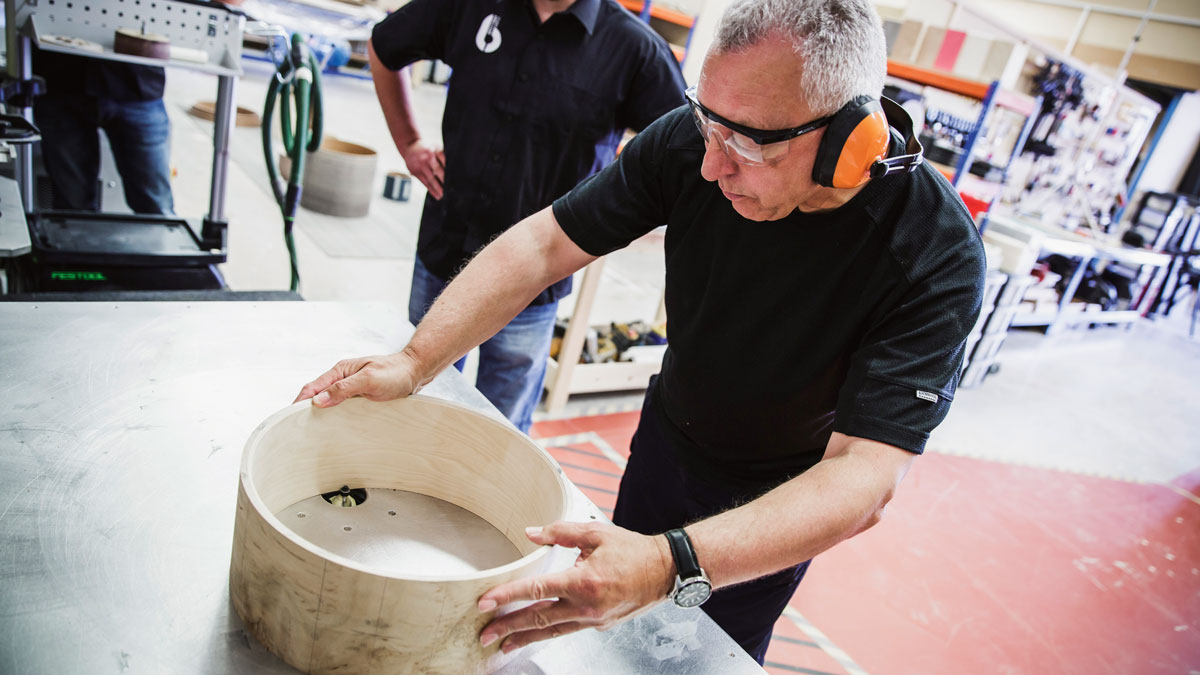
Bearing edges
The 1.8mm deep and 63mm wide dips for the snare beds are cut into the bottom of the shell on both sides. The snare beds are smoothed to a continuous shallow dip using a flat metal file held horizontally.
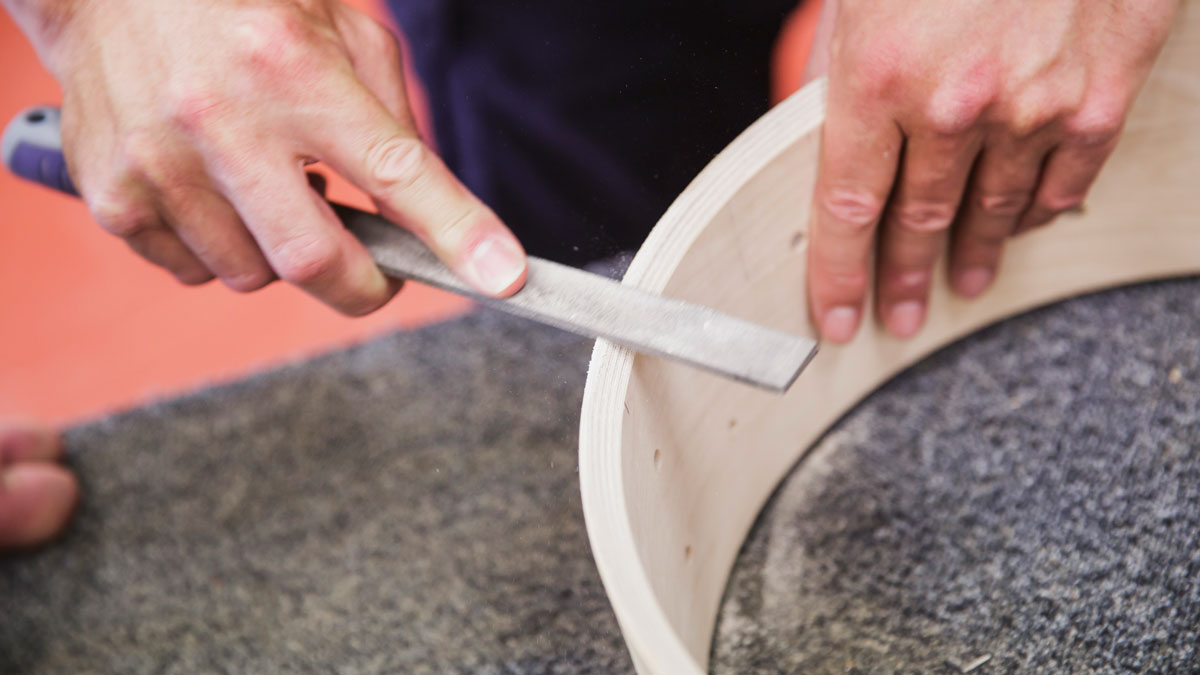
Snare beds
The 1.8mm deep and 63mm wide dips for the snare beds are cut into the bottom of the shell on both sides. The snare beds are smoothed to a continuous shallow dip using a flat metal file held horizontally.
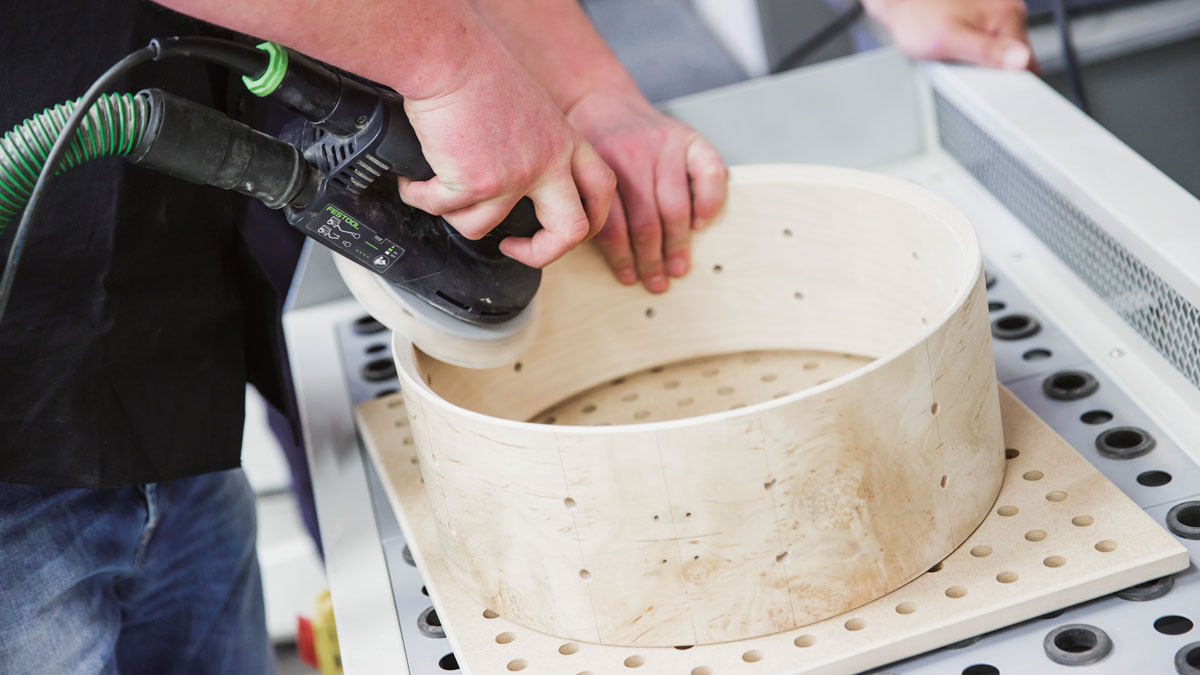
Sanding
The shell is sanded using a random orbital sander. A glass-smooth finish is achieved using progressively 180, 240 and 1200 grit sanding discs. Shell is sealed with BDC’s secret concoction of environmentally friendly oils, protecting and bringing out the unusual wood grain.
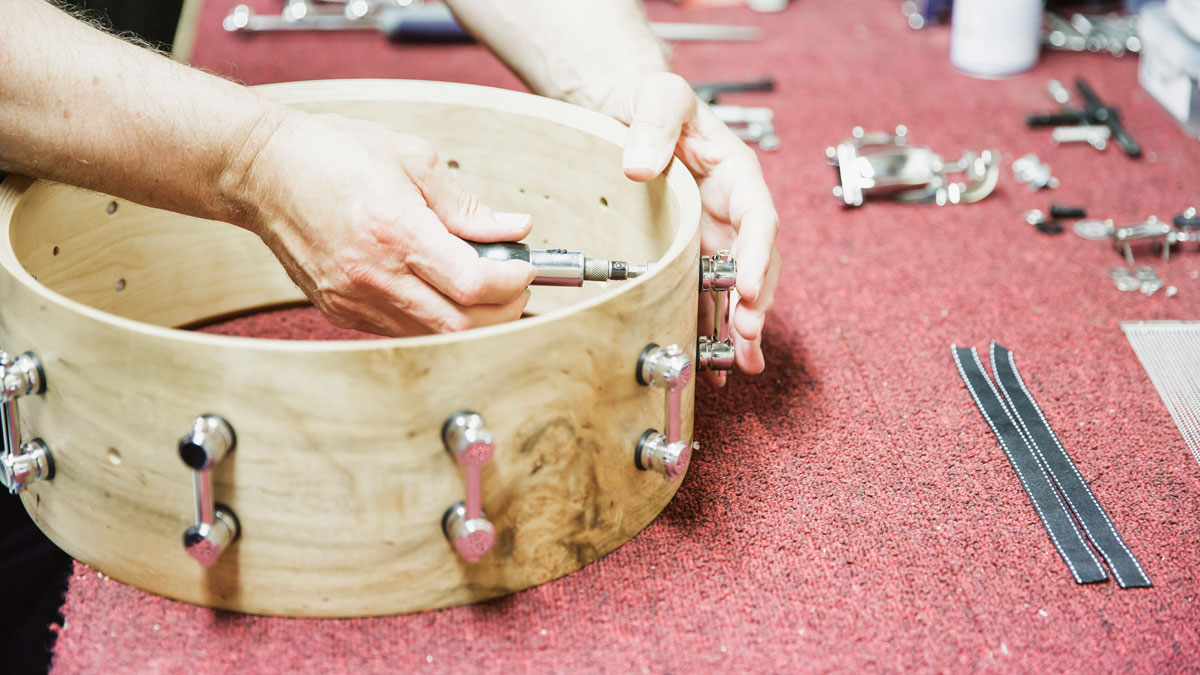
Hardware
All the metal hardware parts, including the 10 solid brass tube lugs, strainer, air vent, etc, are fixed to the shell, and the British Drum Company stencil badge is mounted.
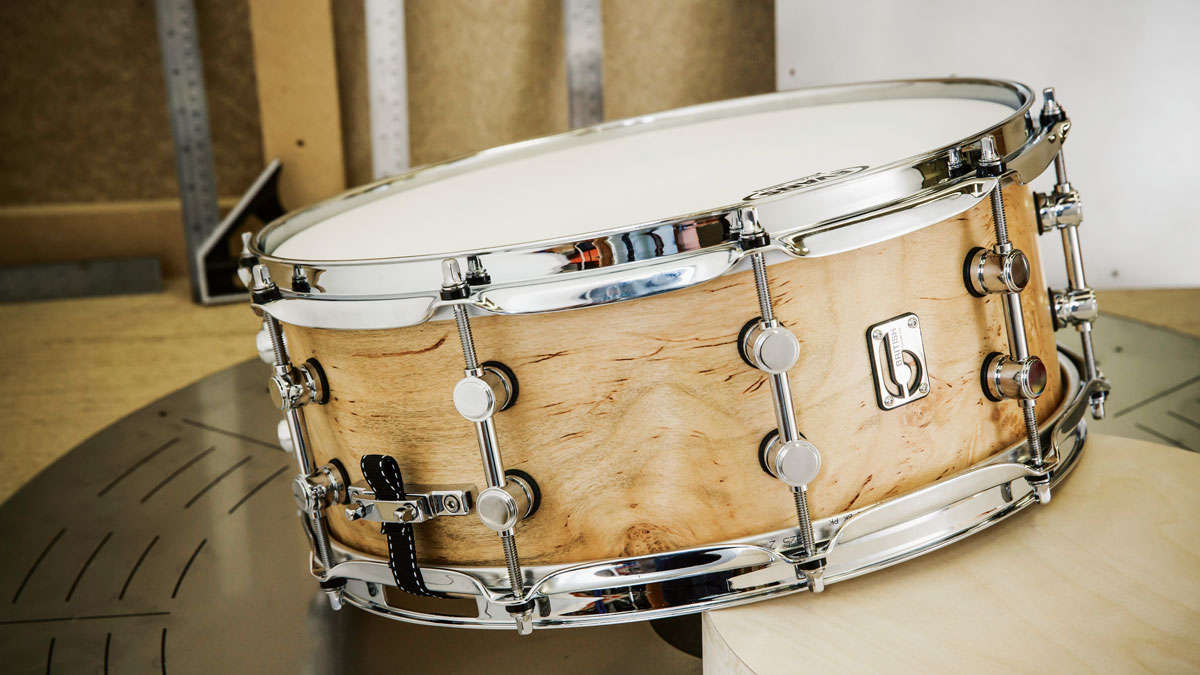
The finished product
The finished Merlin 20-ply birch and maple snare with its Sweet Spalted Gum outer veneer
finish is ready. She's a beauty, right?!