The Workshop: Joseph Lukes Guitars
A look inside the London-based maker
Luke Joseph Sharples has been building guitars for five years having studied musical instrument technology at the London Metropolitan University. He has since set up his own workshop in South Bermondsey, London.
Luke developed his skills under the watchful eye of Nick Blishen and, knowing how important it is for new builders to emerge, he hopes to expand his business and take on his first batch of apprentices by 2015.
As a maker, where do you draw your inspiration?
I'm really interested in art and I think that it provides a great source of inspiration when it comes to guitar making. I value clean lines, flowing curves and minimalist design. I think the design of something should represent the person who created it but also the people who play it. I would say that a lot of other makers also inspire me; I love the versatility of the guitar and how one instrument can be represented in a myriad of ways.
How did you come to make your first guitar?
The first guitar I produced was a parlor style guitar, similar to the old Washburn designs. I used Redwood for the top and Indian Rosewood for the sides. It's covered in purfling and ebony binding and really became an exercise in guitar making techniques. The parlor currently sits proudly in the corner of the workshop as a reminder of where it all started. I still add elements to it now and essentially use it as working design canvas.
What is your preferred style of guitar to play, and make?
Want all the hottest music and gear news, reviews, deals, features and more, direct to your inbox? Sign up here.
I've always loved the grand concert size as it's versatile and embraces many styles of music. I took into account these factors and decided that I want to put my mark on the world of acoustic guitar. I would have to say our grand concert is my favourite to make - I made a guitar that truly represents me and what I want to play.
So are you just focusing on the grand concert size or are there any plans to add more body shapes to your output?
At the moment I'm concentrating on the grand concert design which I'm viewing as the flagship for Joseph Lukes. I think it's far more important to build one quality guitar model than having an extended range of varying sizes. In my opinion the grand concert is the perfect acoustic guitar size to start with as it is versatile and provides great tonality. Of course the instrument is customisable and I encourage people to make it their own. Wood types, inlays and beveling options help to make each instrument completely unique. As for other plans I'm actually in the process of designing an acoustic bass which I'm going to prototype later this year. A baritone, a ukulele and a 12-string grand concert are also all definite future builds I intend to pursue.
Are your guitars are (generally) free from any mother-of-pear and superfluous aesthetics? I guess you like to let the woods speak for themselves?
Of course! There's such a wide of variety of beautiful wood types that they really do speak for themselves; tonally and aesthetically. I'm not anti-inlay, not by any stretch of the imagination, but I do think that good design is often synonymous with minimalism. With the grand concert, I strived to use geometric design coupled with an array of striking woods. There is a lot of scope with the instrument to add inlay and I definitely intend to explore that avenue but the key to the design is in its clean lines and beautiful shapes. I especially like the fact that, depending on the wood type used, each instrument has a completely unique character.
Tell us a little more about the grand concert model you build…
I wanted to design something that I couldn't put down and couldn't stop looking at. I love functional design, I love geometry and I love minimalism. If something is part of a guitar design, it must have purpose. Jazz instruments and the jazz era inspire me, so I think the design for the grand concert reflects a lot of these factors. It's lightweight, ergonomic and feels great to play. It excels in fingerstyle but is comfortable with any style. The extra resonance generated by the increased soundboard area is great to record with and the sound port design, which is definitely becoming more popular, gives the player a true monitor of the sound they project. The neck of the guitar is slender and easy to work with and an oil finish really makes the instrument very playable.
I think innovation is a really important part of guitar design. The aim is to blend innovative, unique designs that are produced using the most traditional luthiery methods, and then the techniques. Continuing to make the same 'standard' guitar designs just because they have become the expected or accepted guitar styles was something I wanted to strive to get away from. Designing a sound port and removing the sound hole are ideas that, although not new, represent a change in the guitar. Besides representing a historical design change, leaving the top of the guitar intact allows for greater resonance and tonal quality. I think there are some fantastic companies, especially in the US, who are exploring the possibilities and I really felt like that was something I wanted our grand concert to be part of. The bridge and fretboard design incorporate clean, geometric shapes providing a stark, complementary contrast to the curviness of the body shapeand headstock. Really, high-end guitars are not only musical instrumentsbut also pieces of art. I wanted the guitar design to reflect this.
Do you have a preference for a particular tonewood, or wood combination, for your instruments?
With Joseph Lukes, the ideology of the company means that each instrument is completely unique. I love that fact that each guitar has a unique build, a unique tonewood combination and they really become their own entity. I do have a set number of woods that I view as classic combinations and these essentially make up the base product. Mahogany and rosewood with Sitka spruce or western red cedar is always a good starting point. Personally, I like Dalbergia family woods as they give the guitar a vibrant, punchy sound which can then be combined with a spruce.
How do you source such wood?
At the moment, being a small company, I'm lucky enough to be able to source the woods one guitar at a time. Unlike the companies with a much larger output, I can afford to look specifically at what's required for the build and buy in minimum amount, thereby reducing waste, our impact on the environment and, most importantly for the customer, allowing me to incorporate the most beautiful examples of each wood into the build. In the future I'll probably look to incorporate milling facilities into the workshop that will allow Joseph Lukes to control its own waste from lumber purchase and ensure that the most sensible and most effective material management is achieved in-house.
With woods becoming more scare, and the CITES and Lacey Act, how do you see guitar building in the future… Are you looking for sustainable material alternatives?
I think the acoustic guitar is slowly splitting into two types. You have the guitar built from traditional materials and the guitar built using new materials which, quite often, doesn't include very much solid wood. There are some really interesting examples of guitars made with laminate constructs, carbon fibre and 3D printing. These are all viable options however don't necessarily make the guitar more sustainable, just merely more sustainable when compared to the use of solid wood. The more traditional route is also interesting, as companies will become more restricted with the woods they can use and eventually this could impact how large a company can become in relation the original integrity of their instrument. I seeJoseph Lukes as a traditional material company and, owing to our size, it means we can remain as such for a lot longer.
How do you go about keeping a green conscience when using certain woods?
I think it is extremely important to be environmentally conscience. In today's society it is frowned upon to not be as such and I think it is about time companies had responsibilities for their actions. I think CITES is extremely important and should certainly be adhered to by everyone who uses wood in their products. I don't believe that woods such as Brazilian rosewood and certain Madagascan woods should be used under any circumstance, and the old excuse of "it was pre-dated" doesn't mean the wood necessarily was. As it's very hard to be sure, I would rather not use it. There are some phenomenal woods out there that are not only tonally exceptional, but also not as scarce. while Brazilian rosewood is a draw to people, I do wonder whether a certain amount of this draw is purely owing to its taboo nature.
What construction methods and techniques do you favour?
"Handmade" has become quite a buzzword in the industry. I see it plastered on everything right alongside "artisan". Placing those words on products doesn't mean they are and it's only a matter of time before consumers realise that is the case. I think Joseph Lukes was born from this frustration. From the outset I decided that I wanted to use only hand tools and only the most traditional methods to ensure that each guitar is unique and of extremely high quality. Consumerism is becoming more and more transparent and I felt that implementing these methods and showing the consumer exactly what it takes to produce a guitar is an important message to send. Guitar makers have an incredible art; it needs to be preserved through education and without diluting it into something unrecognisable.
Which type of heel joint do you use, and why?
I personally favour the set neck, although not for the reasons which I hear most makers stating. I looked closely at heel design and the differing theories within making and concluded a larger heel does aid tonal transfer from the neck to the body, essentially allowing the whole guitar to resonate as one but the actual join is really quite subjective. I know bolt-on is a popular choice and set is often seen as being a true makers mark. It's probably the most hotly debated forum thread on earth. I'll throw myself out there and say, to be honest, there is probably very little in it. I choose to do the set neck as I enjoy making them. I use a mortise and tenon join instead of a dovetail and just really enjoy the process.
Tell us a little bit about the bracing pattern that you use for your guitars?
The bracing pattern I'm currently using is a little bit of a hybrid. I found that by removing the soundhole it wasn't simply a case of reinforcing the top where the hole used to be. The increased surface area allows for far more movement and thus, far more resonance. Although resonance is certainly something I strive for when making guitars, there can also be too much resonance. It took several months and several bracing pattern prototypes to optimise all the factors required in a guitar top. The result is a hybrid pattern, which incorporates the fingerboard support from double X-bracing and a four-strut lattice to maximise the top's movement while providing an extremely strong support to the guitar. The hybrid bracing also incorporates some of Michael Kasha's theories regarding its positioning and how to essentially create the perfect guitar top.
How do you go about getting a consistent thickness for the back and tops of your instruments?
As with the bracing, the thickness of the top also plays a really important part in creating the perfect resonance and tonality. The top's thickness varies from the treble to bass side to maximise the plate's response to frequency. The bass side is a whole millimeter thinner than the treble with a gradual increase through the centre of the top. As you can imagine, graduating such a curve takes time and patience and, as with the ethos of the company, is done completely by hand. I use an extremely sharp 4 ½ Clifton jack plane to take the stock down and then use a cabinet scraper for the more precise intervals. Finally, I implement the good old scraper blade for any spot thicknessing before finishing the whole top through to 400 grit, ready for bracing.
What's the most enjoyably part of constructing a stringed instrument?
I love every stage of it. The feeling of completely building a guitar is one that's hard to beat. Working through each process and seeing them all come together into a functioning object is a fantastic way to earn a living and, to be honest, I enjoy the adventure. There are stages in the build that go exceptionally well and then there are stages which can take longer than expected and any maker that tells you they haven't ran into these problems in a build is a liar. It's extremely easy to slip up, especially if your attention lapses for even a second. The misplaced use of a chisel or glue squeeze-out are certainly common issues but I personally think dealing with these is all part of the challenge and, ultimately, serves to make you a better and far more rounded builder.
Do you offer the customer a fitted pickup - which do you recommend for the best amplified acoustic sound?
Yes, the option of a pickup is one of elements that a customer can incorporate in their build. The grand concert has a brilliant voice and I thoroughly love to hear it acoustically. I personally recommend the Fishman Matrix Infinity as I use one in my grand concert along with a stage microphone. It's a versatile pickup and although I know it's not everybody's favourite, with our guitars it creates a really unique sound. Other pickup types are available and I find it's best to discuss it at the build consultation to ensure the guitar is tailored completely to each customer.
What's on the bench at the moment? What's next on the agenda?
Well I have just completed an African mahogany grand concert with Sitka spruce top and rosewood binding, and I'm currently working on an Indian rosewood with western red cedar and curly maple to be completed mid-February. They are both base model instruments and are truly great guitars. I've also started working on an exotic wood grand concert which has black cocobolo/Dalbergia granadillo back and sides, a Sitka spruce top and bloodwood binding. It should make for a fantastic guitar and add a really stark contrast to the more classic looking base models.
How long does it take for you to fulfill a custom build order?
Each guitar build takes over 250 hours and with custom builds I aim to complete this within six months. Each year we set out to create a limited number of instruments and, at the present, as I am the only maker, there will be 12 guitars produced in 2014. I hope to increase this in 2015 but, as our instrumentsare completely handmade, I don't anticipate this figure ever increasing exponentially. I believe it takes time to create something of high quality and I think it would be hypocritical to say we believe in quality handmade builds and then produce guitars in triple figures.
Luthiery is often associated with an older generation, yet you're obviously not in that demographic. What does the industry look like for youngsters wanting to get involved with luthiery, and what advice would you give to them?
Luthiery has long been associated with an older generation and I think, to a certain extent, it has been happy to stay that way publically. That isn't to say that there aren't many young luthiers, I just don't think that guidance and direction is too available and they become a little lost in the social demand for a "real career". I believe wholeheartedly that guitar making and the artisan trades as a whole are a viable option for any youngster's career, and with determination you can achieve whatever you want. The 21st century is rife with social platforms on which to sell yourself and your art form, and couple that with advice from the older generation and an awfully large bookcase of guitar making literature, I think getting involved inluthiery is a more than sensible decision.
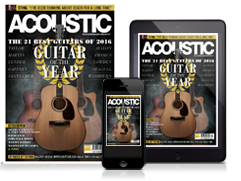