How to install new guitar tuners
Electric Guitar Week: Equip your electric with locking tuners for improved tuning stability
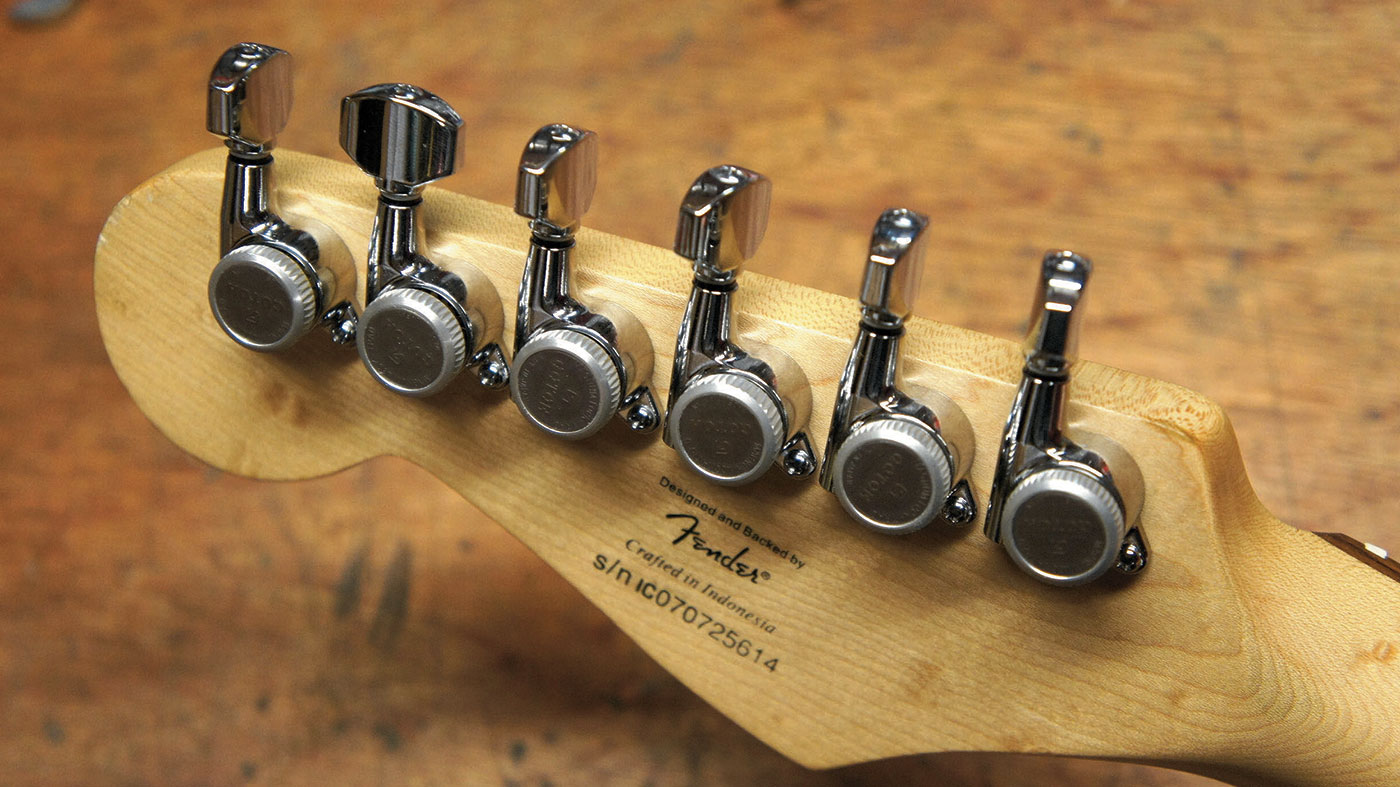
Introduction
ELECTRIC GUITAR WEEK: Upgraded machineheads can improve ropey tuning, here’s how to properly fit them like a pro.
As with most guitar parts, the tuners that come on your guitar are often not much to shout about. A nice shiny set of machineheads can help out with your guitar’s tuning stability and offer a smooth tuning experience. However, the tuners themselves are not entirely to blame for the guitar’s tuning stability.
In brief, the tuning stability checkpoints are: string wrapping technique, tremolo or bridge, string ball ends, the tuners themselves and friction points. The friction points are string retainers, the nut and the bridge saddle tops. Now we think of it, this deserves a dedicated article on it…
So our point was that the tuning machines/tuners/machineheads (call them what you will) are only part of the equation. Now cheap tuners don’t help one bit as the quality of the gearing lets them down. This lowly Squier Affinity was a very deserving candidate for some fancy-schmancy Gotoh locking tuners. Stay tuned and we’ll try and keep it staying in tune.
Electric Guitar Week is brought to you in association with Fender. Check out the Electric Guitar Week hub page for more tips and tutorials.
Skill level: Intermediate
What you need:
- Lovely new set of tuners
- Set of strings
- Masking tape
- 1.5mm drill bit Drill
- PH1 screwdriver
- Set square
- 10mm spanner
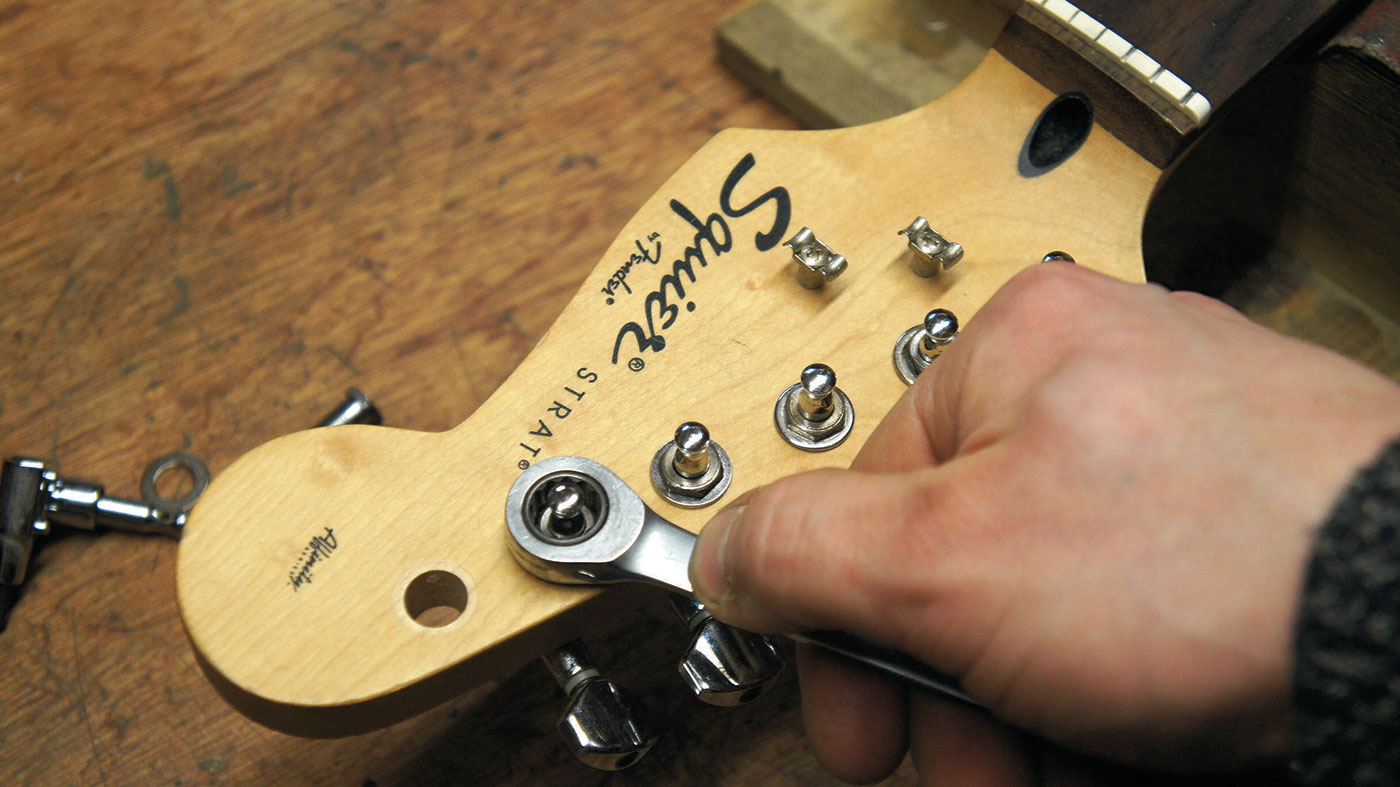
Step 1
Let’s whip off the old ones. This lovely 10mm ratchet spanner is just the trick.
Your tuners may be different but these ones have a nut on the front only. Watch out in case you have the fiddly mini screws on the back, and spend a bit of time researching the shape/fixings of the tuners you need.
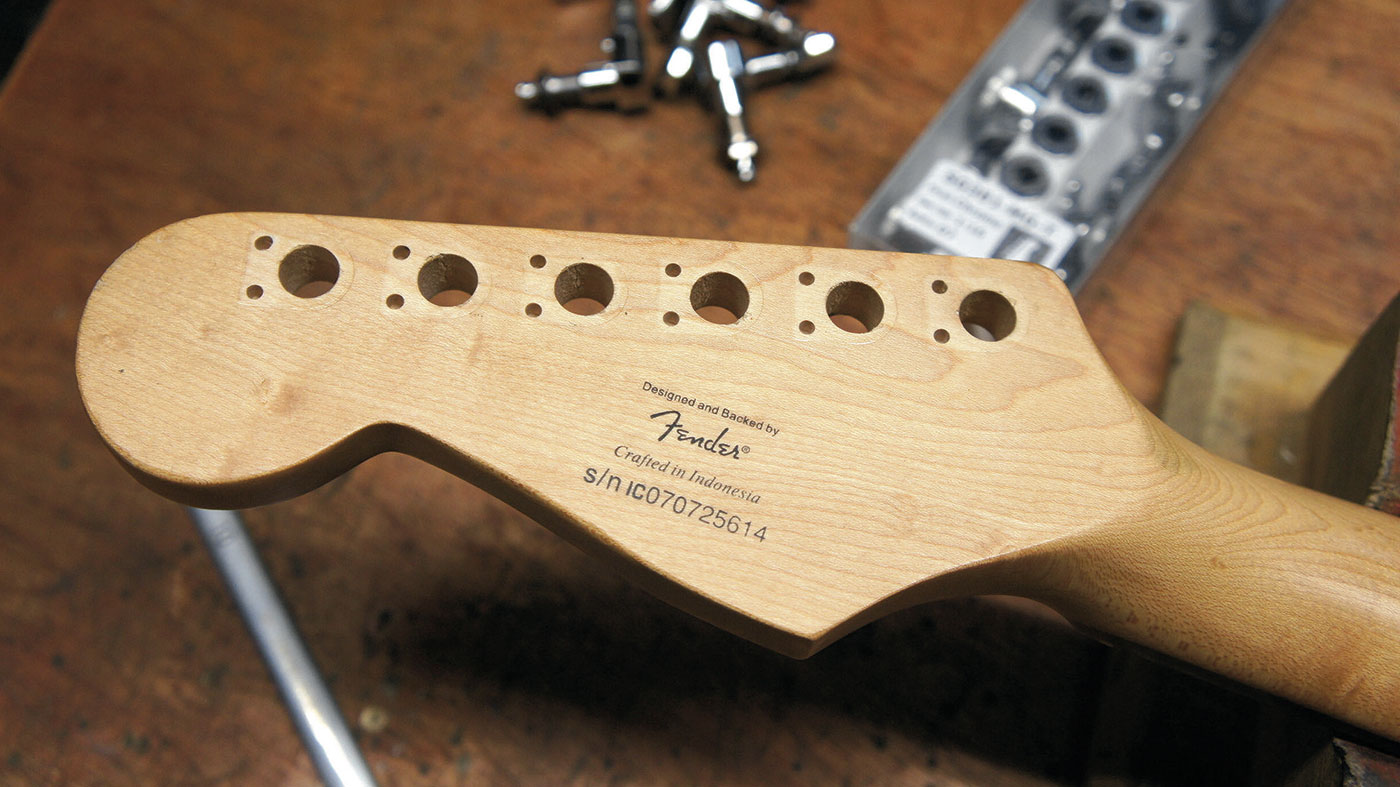
Step 2
Here’s the nude headstock. The type of tuner we have taken off features two locating pegs with the corresponding holes.
While we could have swapped them like-for-like, we’ve intentionally chosen new tuners that will cover up all the old screw holes. Have you spotted the sun tan the maple has gotten too?
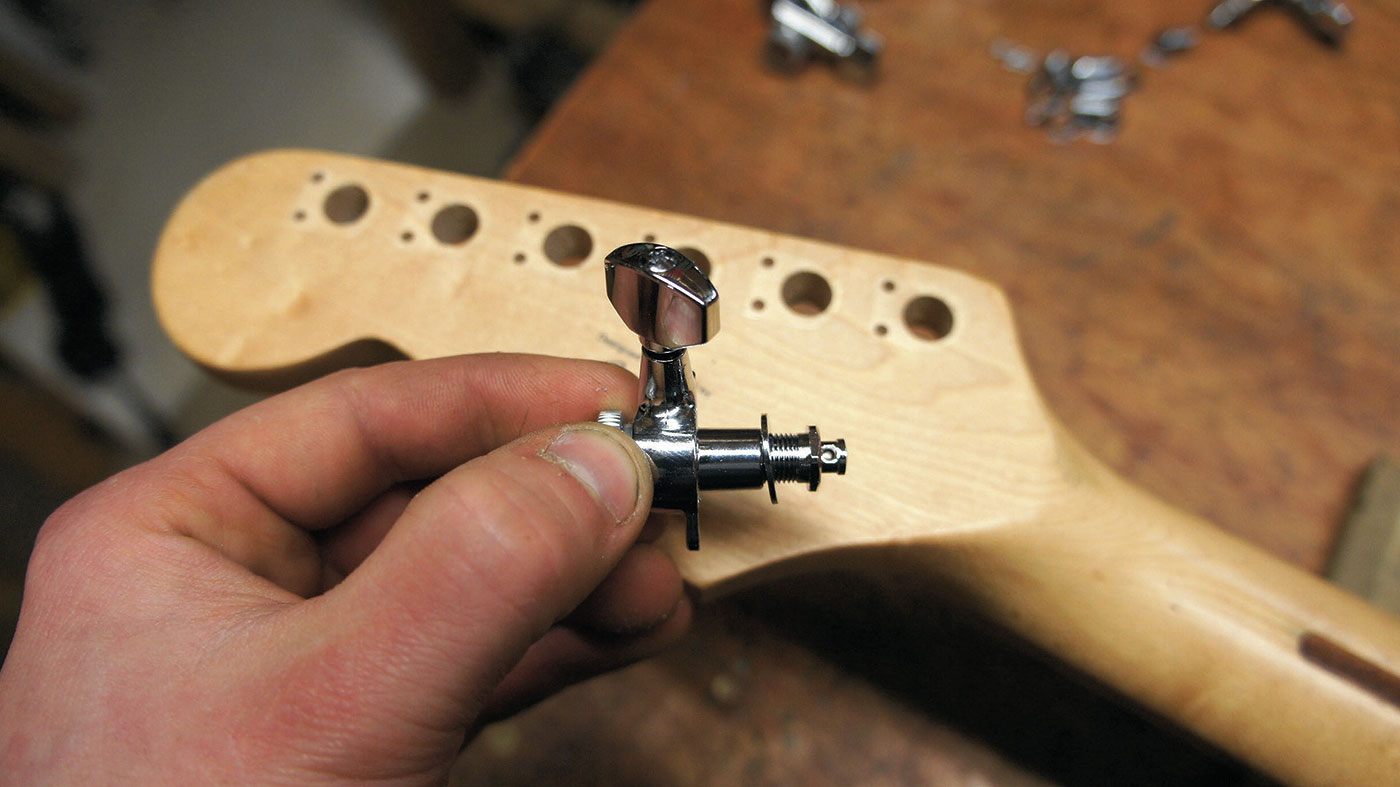
Step 3
A simple thing but it’s often done wrong; this is the order you’re going for with the fixings: nut, washer, headstock then the tuner itself on the back.
These Gotohs had a nice looking side to the washer and a dull side - place it nice side out of course to show off your wares.
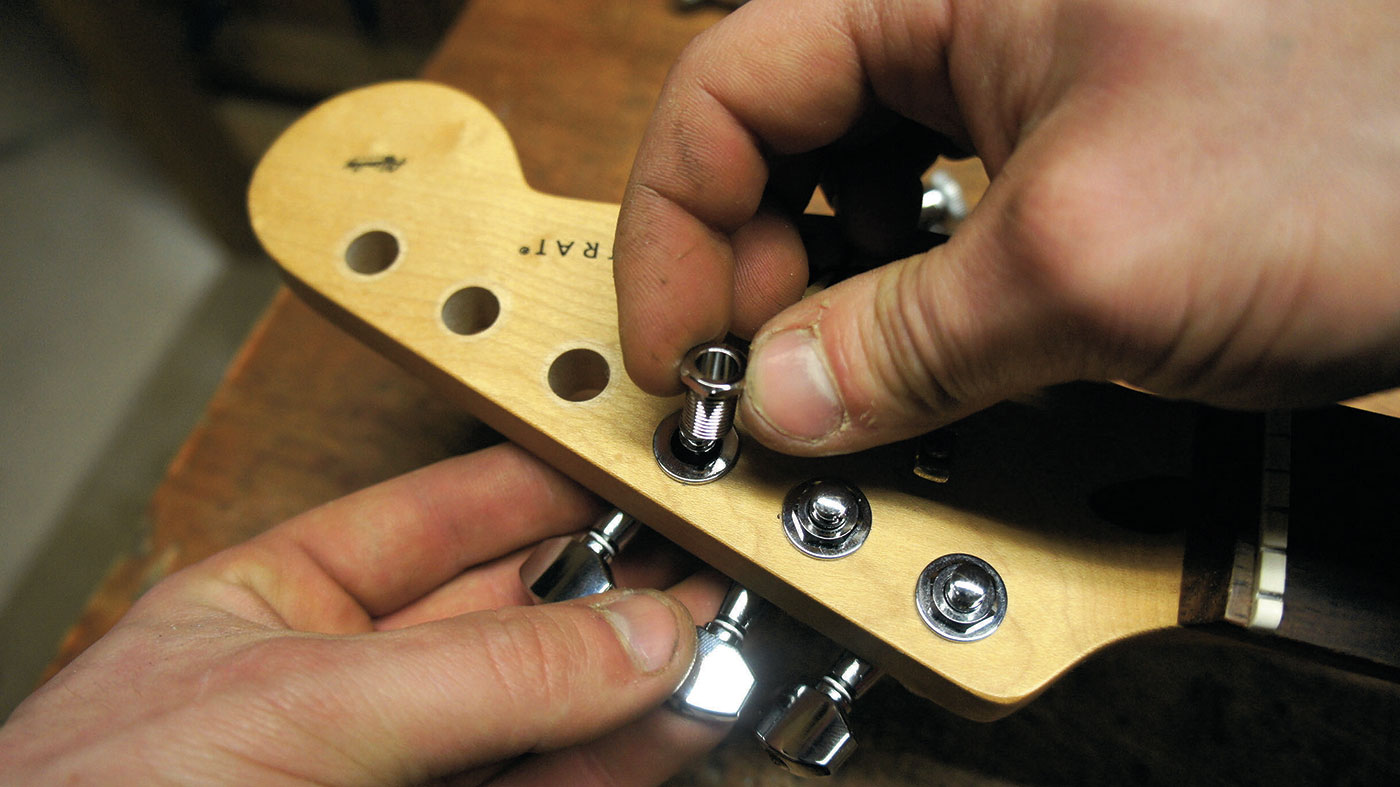
Step 4
Bung them on. For now we’re just doing up the 10mm nuts (and washers) finger-tight and not worrying about them being crooked.
These Gotoh tuners are also ‘staggered height’ - some are taller than others to compensate for the angled headstock. The taller ones go nearest the nut and the shortest near the headstock tip.
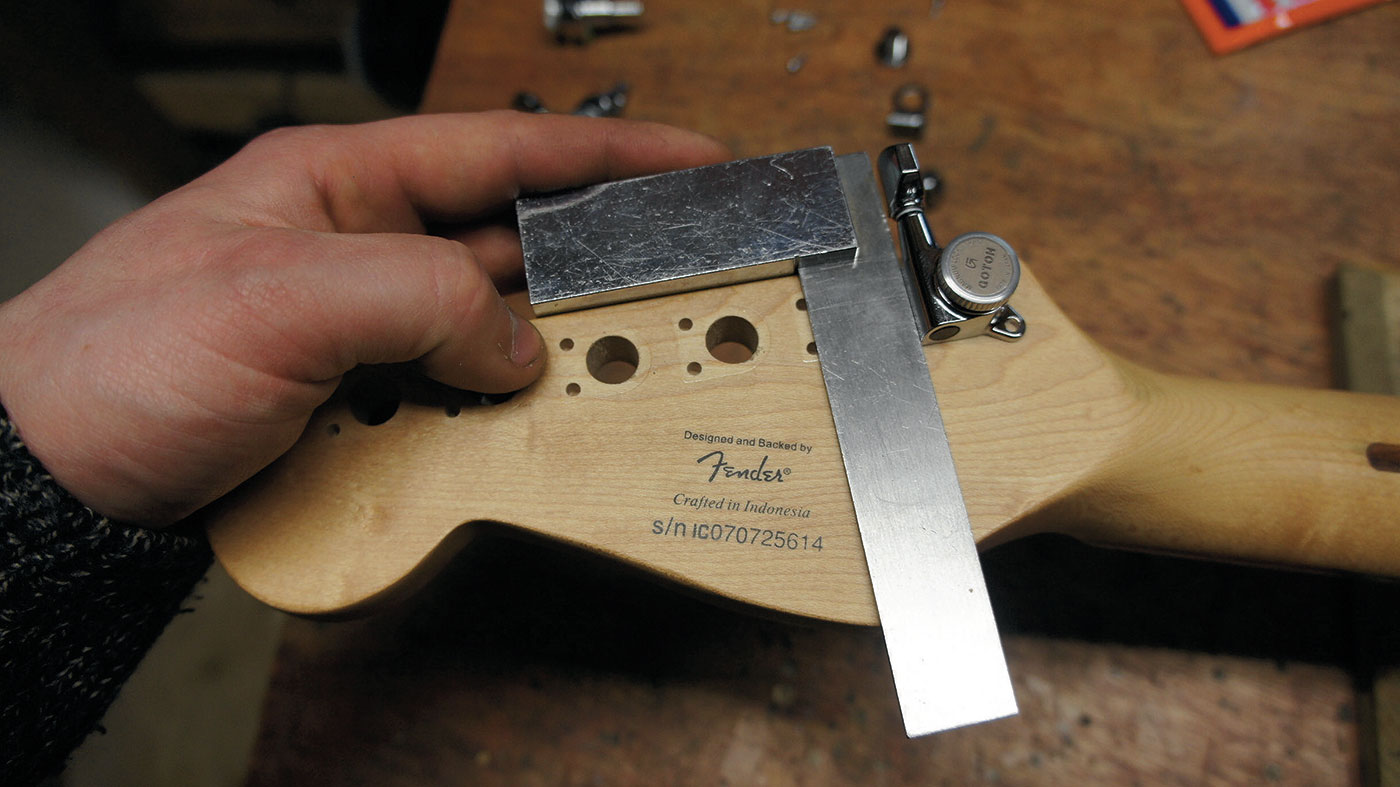
Step 5
Jack’s Super Hack: use a set square to get the alignment bang on!
It looks really crappy when tuners are installed wonky so make sure you’re not one of those bodgers. Use the main body of the set square against the headstock top. On a Strat type guitar of course they want to be 90°.
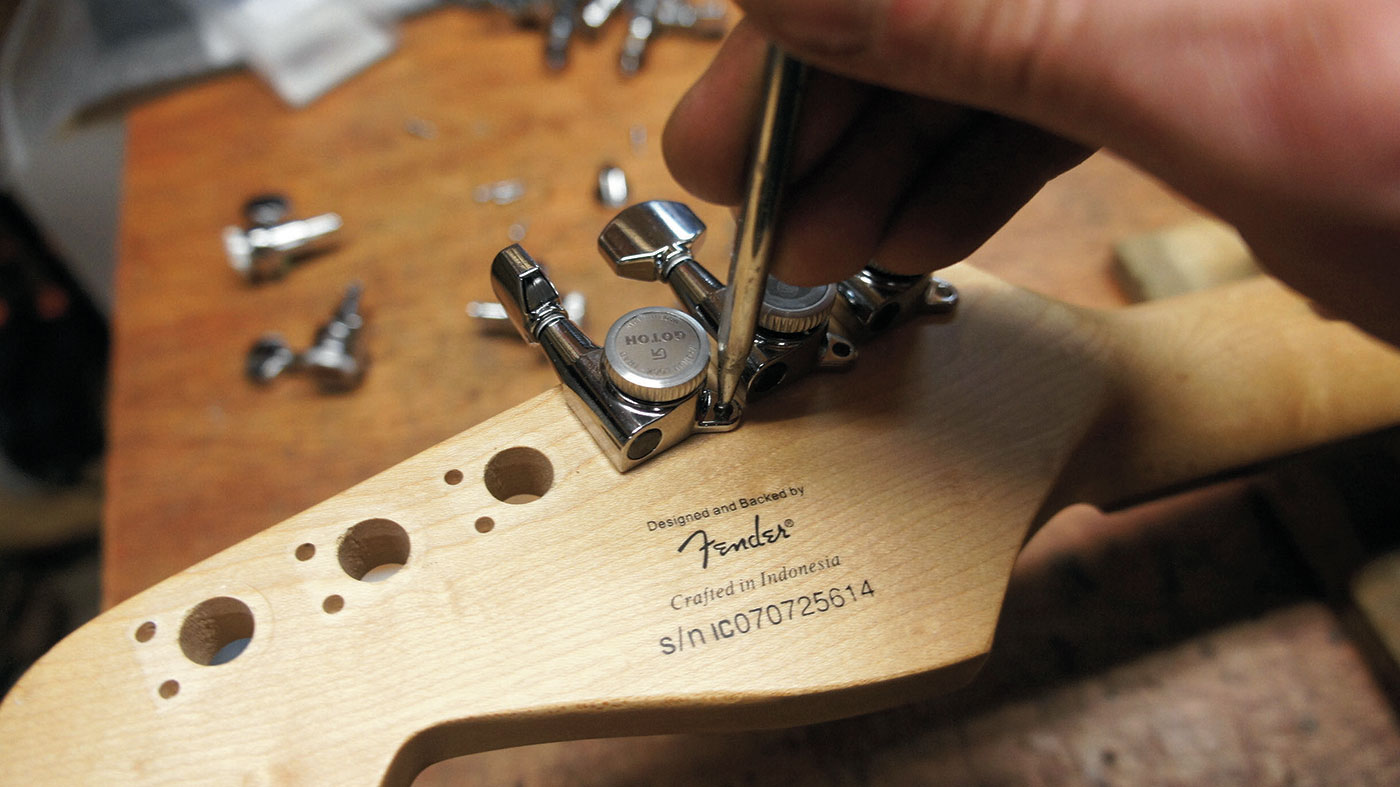
Step 6
Having lined up the tuners perfectly, fetch your jabbing implement and get jabbing. Be careful not to disturb the tuners whilst you’re a-jabbing.
This will be the location of our screw holes. If you don’t have a jabber (the real name for it is an awl) you can use a longer screw or knitting needle etc.
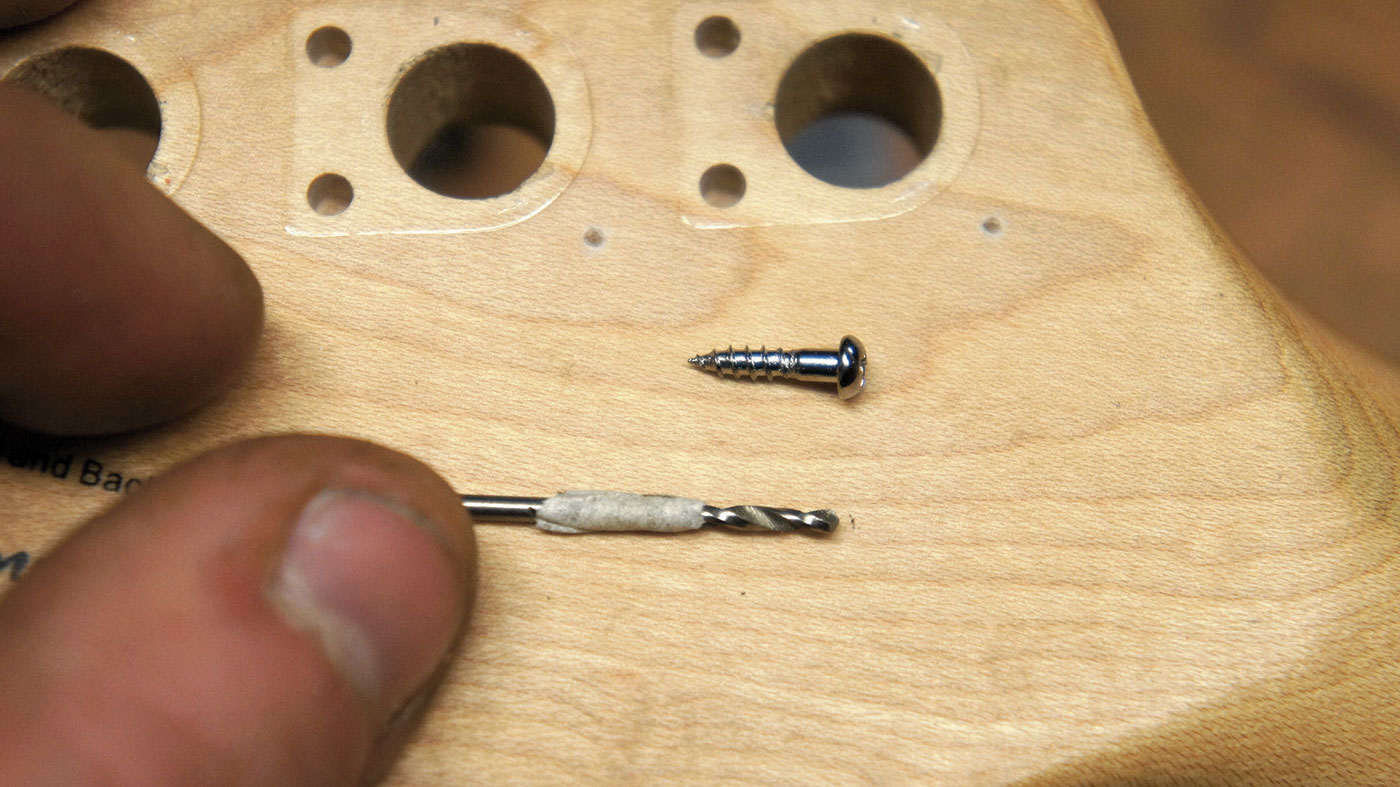
Step 7
Now you have marked the location of all the screw holes, let’s drill them.
The big no-no is drilling all the way through - stick masking tape on the drill bit to mark the depth. Maple is very dense timber so a 1.5mm drill bit for a 2mm screw is a good pairing. If you drill too small a hole the screw will likely shear off.
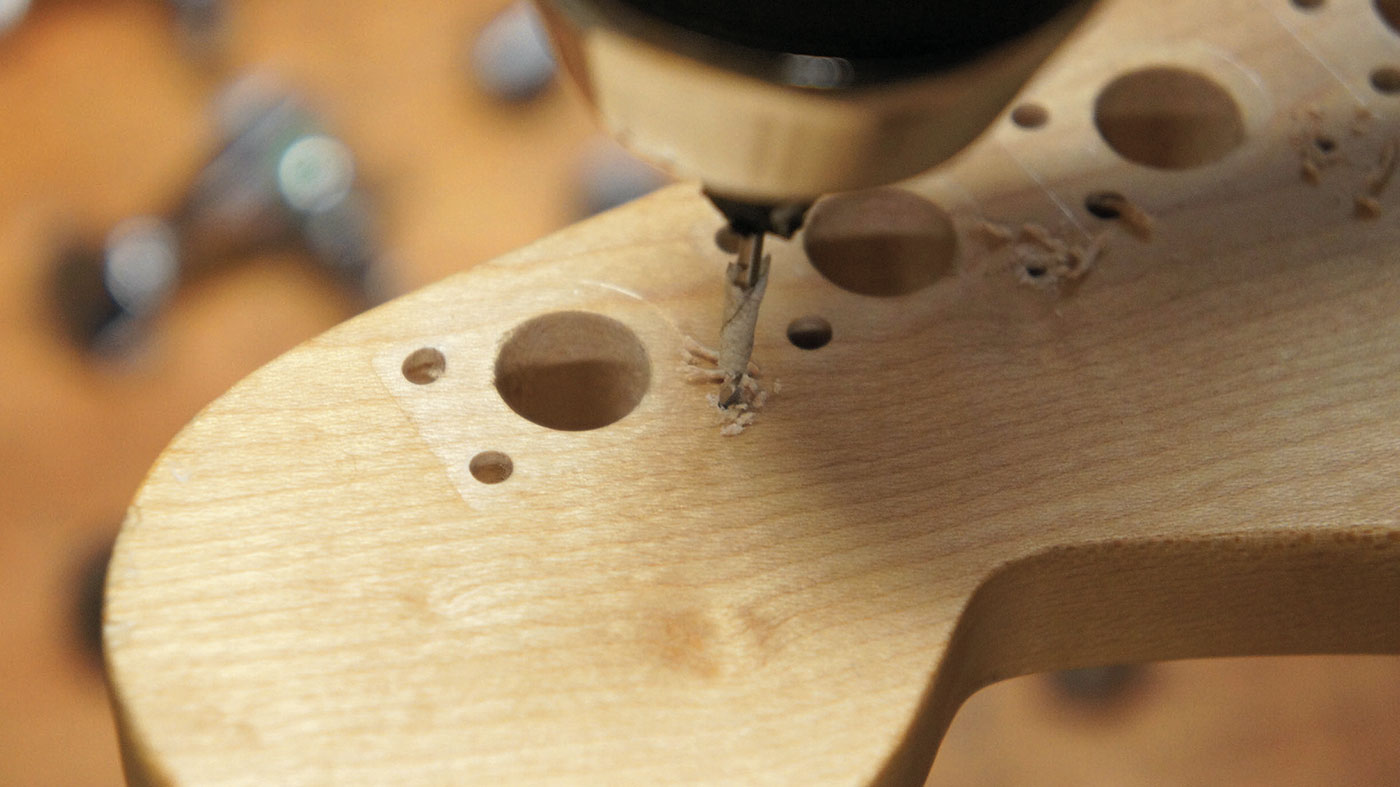
Step 8
Steady your hand and drill into the headstock. Remember that maple is a dense wood and very unforgiving.
So be careful not to drill too deep and be extra careful not to snap off the drill bit in the maple. You don’t want to have to excavate a broken drill bit.
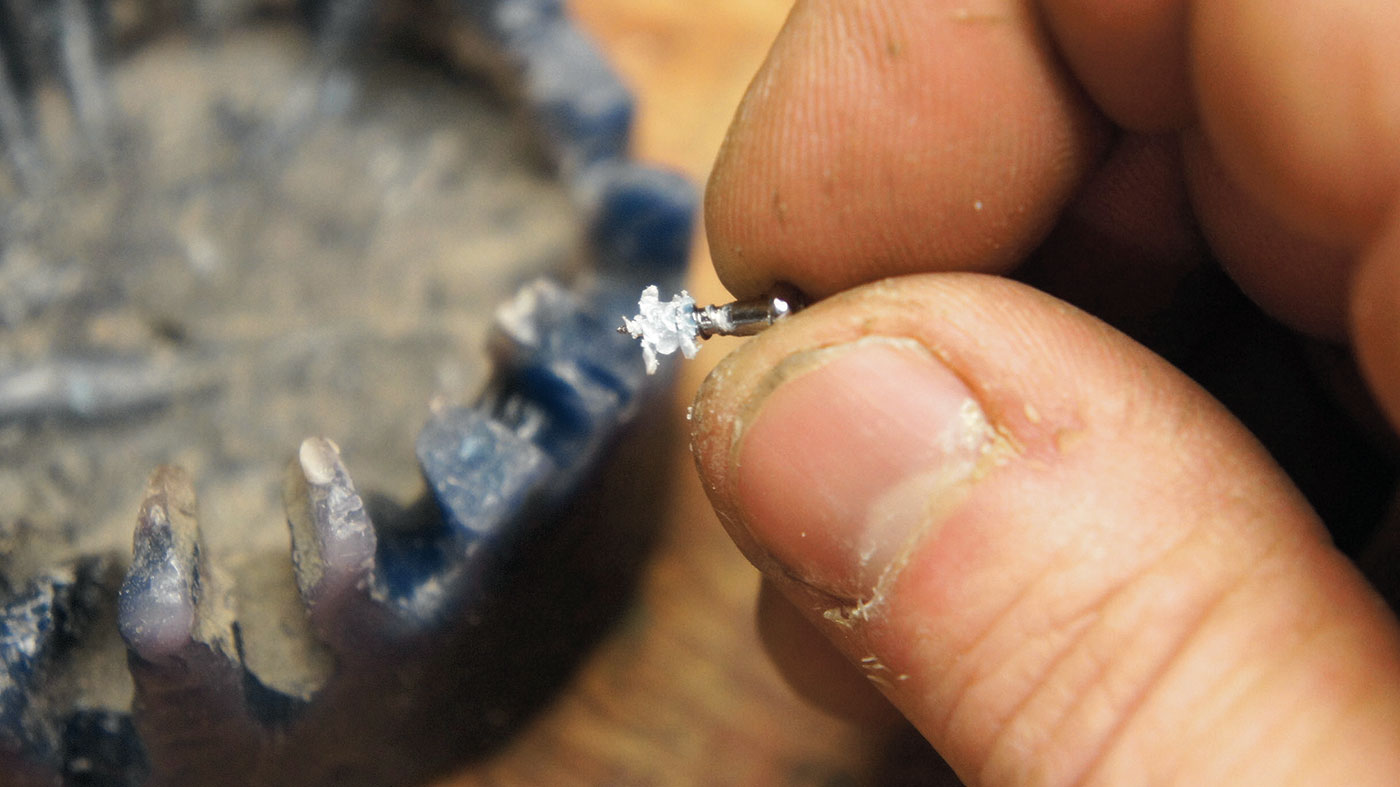
Step 9
Replace the tuners and finger-tighten the 10mm nuts on the front again.
Use a candle to lubricate the threads of the teeny-tiny screws. This will ease them in and ’cos it’s not oil it won’t stain the maple. If you don’t have a candle handy, a bar of soap will do.
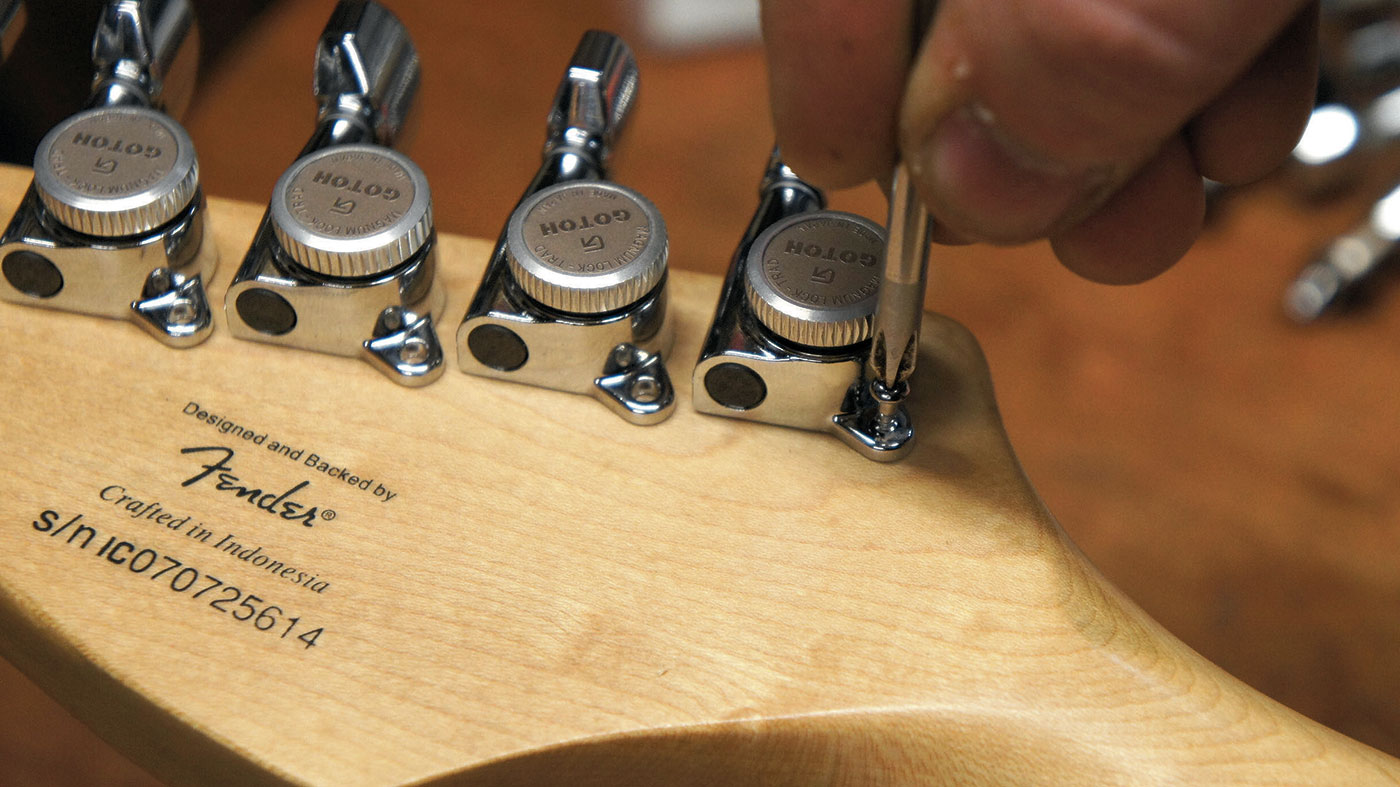
Step 10
Screw them in using a PH1 screwdriver. Blow off the excess wax as it crumbles away.
We recommend a hand screw driver as you can feel the torque and, more importantly, you can feel when to stop. As these screws are so small and fiddly they don’t need much persuasion before they break or strip. Go easy on them!
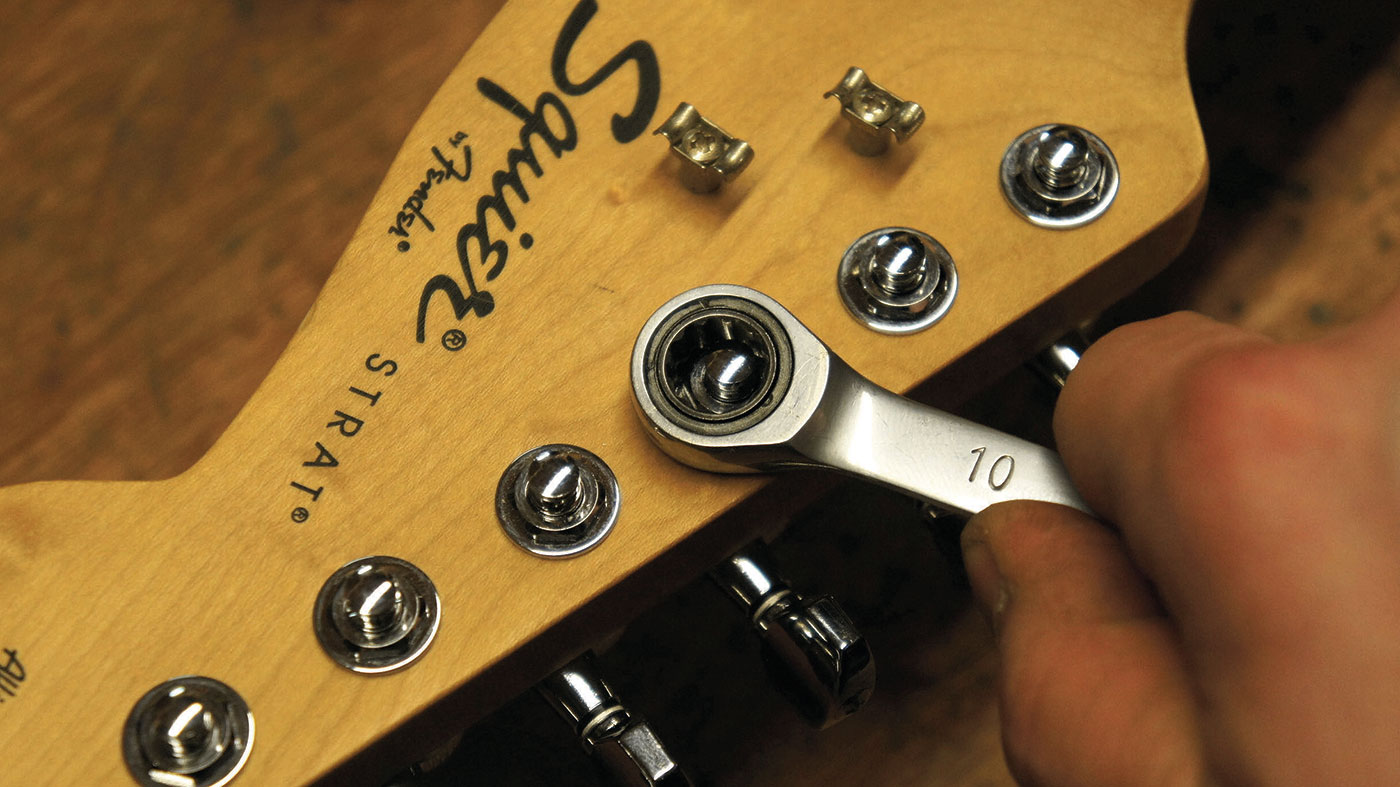
Step 11
Nip up the 10mm nuts on the front with your spanner, being careful not to slip and scratch the headstock face or your lovely chrome-coated nuts.
These are responsible for the machinehead’s stability but, again, don’t overdo it. These 10mm fellas can be quite delicate despite them looking pretty hench.

Step 12
Give the alignment on the back one final check and then string her up!
These locking tuners don’t need any string winds, so pull the strings tight, do up the thumb wheel locks on the back and then tune. We always recommend stretching your strings in even with posh tuners. That should do it!
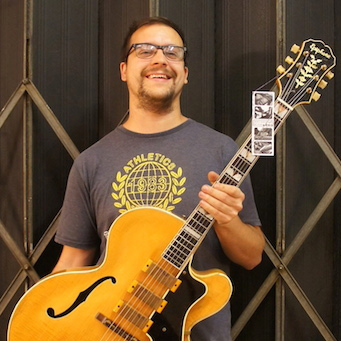
Jack runs an independent guitar setup and guitar repair service in Manchester, England. He serves the musicians of the Northwest of England, working on electric guitars, bass guitars, acoustic guitars and more. Jack has been writing the Fix Your Guitar column in Total Guitar Magazine since 2017.
“‘Would you like to tune your guitar?’ ‘Oh, no thanks, I’m trying to give up’”: The Tunerette is the healthy option for Clapton and Keef fans looking for that cigarette on the headstock look – and it tunes your guitar
"Offers a huge amount of options for all players of stringed instruments, and provides the highest accuracy available for any clip-on tuner": Peterson Stroboclip HDC review
“‘Would you like to tune your guitar?’ ‘Oh, no thanks, I’m trying to give up’”: The Tunerette is the healthy option for Clapton and Keef fans looking for that cigarette on the headstock look – and it tunes your guitar
"Offers a huge amount of options for all players of stringed instruments, and provides the highest accuracy available for any clip-on tuner": Peterson Stroboclip HDC review