We´ve just got out hands on Steinberg´s MR816 CSX and CC121 units, which integrate tightly with Cubase. Steinberg have released Cubase hardware before, but these new devices are the first such integrated hardware created in conjunction with parent company Yamaha, and they offer some exciting features.
The MR816 CSX FireWire audio interface includes the onboard DSP powered REV-X reverb and Sweet Spot Morphing Channel Strip plug-in, plus 8 discrete mic preamps with combination XLR and TRS analog inputs with switchable phantom power per channel, plus digital ADAT and S/PDIF ins and outs.
The CC121 is a dedicated Cubase controller with control of Cubase channel settings, 12 dedicated EQ rotary encoders, and Novation Nocturn-style “point and control” feature that allows you to control whatever you hover the mouse cursor over using the unit´s big knob.
We asked George Yamamoto, Director of Engineering Strategy at Steinberg, and Huey Sekido, Product Planner for Computer-Related Products at Yamaha about creating these exciting new bits of hardware.
Presumably the development of any piece of hardware will involve numerous mock-ups and prototypes before going into final production. Are these made in-house or created as one-offs (or very limited runs) by a factory? Do you use a 3D printer to create realistic mock-ups?
"We make several different shapes of mock-up and at least two steps towards a prototype. Mock-ups are mainly to decide a cosmetic design with respect to the feeling of materials in terms of texture and user interface on the real 1:1 scale. In some cases, it's also to check positioning or conflicts among electric and mechanical parts inside of a unit.
The first prototype is necessary to check if the detailed electric/electronic and mechanical designs are satisfying, and get firmware development started, especially panel operations.
The second prototypes are assembled in the real mass-production line in a factory (these are the so-called pre-production units) to check the efficiency of assembly and make sure that unexpected problems don´t happen in the mass-production phase. There should not be large design changes from the second prototype (pre-production units) to the mass-production unit for an efficient and a well scheduled development. Therefore, we are always trying to fix all found or expected problems within the phase of the first prototype checking, and we usually have prepared well enough that we can move smoothly through the later phases of development and production.
We don´t normally use a 3D printer to make mock-ups, but are now using 3D CAD in many cases for prototype designs, because 3D CAD is very useful to analyze things in advance like heating conditions or the problematic twisting of parts with emulated external pressure, and so on."
Computer music hardware often integrates tightly with the software, which must present an extra challenge in that the software has to be developed alongside a piece of hardware that isn't yet finished. What's the solution to this problem? Do the programmers work with prototype hardware, or by using some sort of virtual version of the hardware in its place?
"That's definitely an extra challenge. Working with prototype hardware or using a virtual version depends on each situation of the development of a product or function.
It means our development is using both case by case, but with MR816 CSX/X and CC121 this time, those integrated functions were made with prototype hardware. Even if the full prototype hardware is not in time to start firmware/software development and in the case we cannot use any virtual tool, there are still ways to start them earlier. For example, a solution would be making the main circuit board just around the CPU much earlier than other components or modifying it to use some similar and former product's board.
And also, hardware development on the whole needs earlier decision-making on detailed specifications or functions (i.e. panel layout and its operation together with Cubase) than a purely software product. This meant that for these new products with their many deeply integrated features, collaborative discussions and cooperative work between the two teams at Yamaha (hardware related implement) and Steinberg (inside of Cubase) were also necessary. The time and resources for this development were extensive, and we believe that both the concepts and the actual implementation of integrative functions have worked out very well.
Anyway, release timing of a product to the market is the key, as is achieving a relevant timing of release and our development team is always thinking what the best way would be to make it on time."
Hardware has to be designed to strict regulations, for example EU safety regulations. What kind of testing is a product subjected to before it's able to hit the shelves?
"A typical test might be the measurement of the level of signals emitted by the unit. We cannot avoid each electric/electronic part emitting some signal to the outside, and there are strict regulations that set border levels in each frequency. If the test result is over the border, we must reduce it. Another example would be a protection to a high voltage part. The part of circuit whose voltage level is high should be shut in so that a customer can´t touch it from the outside of a product."
If you´d like to learn more about how hardware is made, check out the Burning Question article on the topic in CM131, on sale on the 24th of September.
Get the MusicRadar Newsletter
Want all the hottest music and gear news, reviews, deals, features and more, direct to your inbox? Sign up here.
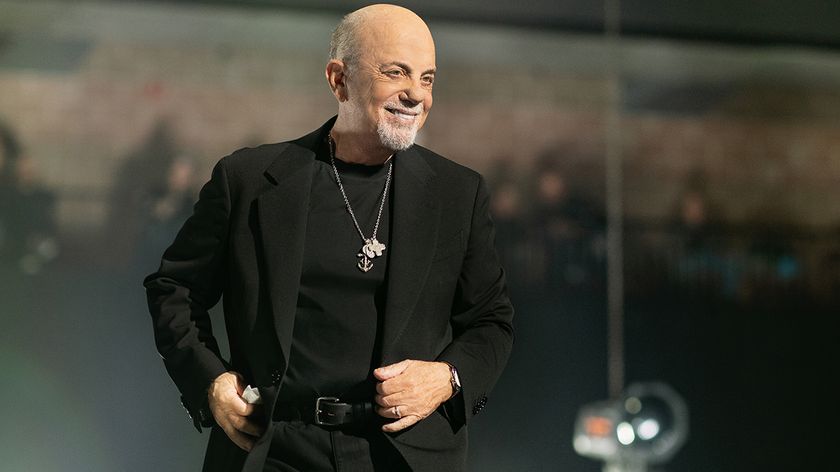
“For those who think they know Joel’s story, as well as those who are not as familiar, I believe this two-part film is both a revelation and a surprise”: New Billy Joel doc is on the way
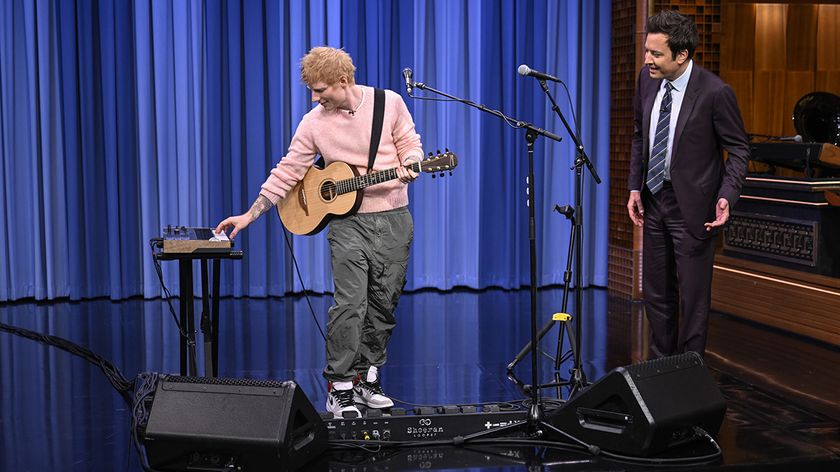
“At the time, I wasn't, like, the coolest kid, and people didn't want to be in a band with me”: Ed Sheeran explains why he started using looper pedals, then demonstrates one by performing a number one hit that he wanted to give to Rihanna